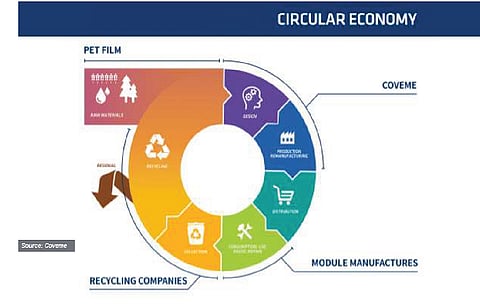
Sustainability has always been a topic in solar and, of late, is getting increased attention. It would be more of a concern when the solar modules reach end of life, as modules contain considerable amounts of polymers that eventually require safe passage for disposal.
As a first step towards module waste recycling, DTF, in cooperation with Coveme, have launched a range of backsheet films with 33% recycled content which won the Intersolar AWARD in 2021. The development was possible due to the LuxCR process which breaks down the waste material to the starting monomer— the building block for all polyesters — removes contamination, and then rebuilds it into a PET film for PV or any other application, said DTF's PV marketing manager Steven Davies. It is like upcycling the PET waste and blending it with 2/3 virgin material to make PET films used in backsheets. The key here is to make the recycled product's properties identical to one made with 100% virgin material. Additionally, the product also reduces the carbon footprint by 10%, according to Davies.
Coveme's role in the supply chain is a vital one. It takes the PET films made from recycled content and converts them into backsheets to be used by solar module makers. "We absolutely believe that sustainable product design and circular economy models are becoming a must and requests coming from the market confirm this," said Coveme's COO Monica Manara. As a matter of fact, the company is already offering a 1,000 V DC backsheet with recycled polyester film, which according to Manara has undergone the same qualification test and proved to be equal in performance, as well as in reliability, as the company's standard backsheets. The company also concluded the development activity for a 1,500 V DC version, which is currently under internal evaluation, and expects it to be successful as the earlier one. As a step further, Coveme has also finished a feasibility study of a circular process for the recovery of the PET-based backsheet at the end of life of the solar module. "We proved that the polyester can be separated from the module, taken back into a monomer state and used again for PET film production," said Manara, adding, "A closed loop so to speak" (see Quick Rise In Backsheets Material Prices).
Endurans also highlights the sustainability of its Endurans HP product range, which is "fluorine free" and according to the company has a 30% lower carbon footprint compared to fluorinated backsheets made using the lamination process. It has a positive impact on waste treatment and associated costs at the end of life of modules, said Endurans' global communication and branding lead Annet Hoek (see Solar Backsheets Directly From Resin).
According to Borealis' business manager for solar, Alper Muraben, PP is highly recyclable, which is done so in a very large scale; and Borealis, with its wealth of experience in recycling, is focusing on circular economy for plastics. He further emphasized that the all-PP backsheet is a mono material — a common word in packaging. The packaging industry itself is moving away from multilayer packaging; for example, paper on the outer side and plastic on the inside pose problems in sorting and recovery as part of recycling. Based on the experience with other applications Borealis has, mono materials have shown to have the best yield in recycling. Not only the final product, even during the manufacturing, the waste from trim on the edges can be fed back into the extruder. "Mono materials will be preferred in the future," he underlined (see Variants Of Transparent Backsheets)
The Text is an excerpt from TaiyangNews' recent Market Survey on Backsheet and Encapsulation Materials, which can be downloaded for free here.
An overview of the survey was presented during TaiyangNews Conference on Reliable PV Module Design. To learn more about the conference and view the presentations click here.