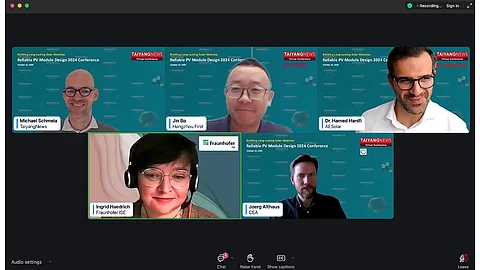
Day 2 of the TaiyangNews Reliable PV Module Design 2024 Conference discussed solar module reliability in and outside the factories
Leading solar cell and module manufacturers, including LONGi & GCL, along with encapsulation market leader Hangzhou First shared efforts on their part
German module maker AESOLAR provided insights into the reliability of solar car ports
Representatives from the quality control, testing and certification segment, including Fraunhofer ISE, said testing all various technologies and materials is ideal but neither cost-effective nor feasible
After an insightful day 1 discussing concerns and solutions around reliability aspects for solar modules during the TaiyangNews Reliable PV Module Design 2024 Conference, day 2 continued the discussion as new technologies and products make a beeline in the global PV market, especially in times of record low prices.
Fraunhofer ISE’s Head of Group ‘Degradation Analysis and Modelling’ PV Modules, Ingrid Haedrich shared the reliability aspects from the German institute’s Testing and Calibration Laboratory (CalLab).
For TOPCon solar cells, its early testing program focused on UV and moisture ingress faults. According to Haedrich, glass-to-glass (G2G) TOPCon modules exhibited higher degradation in short-circuit current (Isc), along with a decline in the fill factor (FF) in damp heat (DH1000) aging tests. Notably, glass-to-backsheet (G2B) versions exhibited even worse degradation.
Since then, it has changed the setup as more field results have also started coming in for this technology.
Haedrich shared the results of Fraunhofer’s moisture testing, which concurs with the test results of other laboratories that show TOPCon as being particularly susceptible to moisture with an average degradation of 1%.
She also showed that the industry’s shift towards thinner glass in larger modules has led to unexpected breakage in the field, particularly for modules with glass under 2 mm thickness and those larger than 3 m².
The institute finds that several modules measure below the power output labeled by the manufacturers. Its calibration lab analyzed 954 modules and found an average deviation of 1.3% below labeled power, even though some improvement was seen in 2024. She shared that while big companies do make the effort to come to the testing labs or cross-check the label value, smaller installers don’t have the resources to do so as it is too expensive for them. This variation then impacts trust.
Haedrich pointed to the need for standardized testing to maintain reliability across the industry. She also stressed the importance of collaborating in testing to ensure lab results match the field performance.
LONGi’s Product Marketing Manager Dante Zeng shared the full lifecycle reliability for the company’s latest offering Hi-MO X10, based on its proprietary Hybrid Passivated Back Contact Cell (HPBC) 2.0 technology.
Wafer selection and the right encapsulation help integrate reliability at the cell design stage to prevent microcracks. LONGi uses its in-house developed advanced thicker TaiRay wafer for HPBC 2.0 with integrated bypass diodes in each cell that prevent localized overheating to deal with hotspots.
While the TaiRay wafer lends durability to the module, the zero-busbar (0BB) structure evenly distributes stress across sub-grids, decreasing the risk of cell damage, he said.
The new LONGi module also comes with an anti-dust feature wherein it has done away with one side of the frame so that the dust can naturally slide off. This brings down maintenance costs, stated Zeng.
Compared with TOPCon modules that experience UV degradation due to the use of aluminum oxide (Al₂O₃) in the diffusion layer on the front side, Zeng said HPBC 2.0 modules use bipolar hybrid passivation on the back side which effectively brings down heat stress. These also have a 1.5°C lower operating temperature than TOPCon. These features extend module life.
Zeng also underscored the financial health of the company as crucial for customer trust and support over the long term.
The Technical Support Director, Europe at GCL-SI, Rojen Malachi, shared the company’s manufacturing integration, quality control and innovations in his presentation.
He drew a direct correlation between module reliability and investment, sharing how GCL-SI improves efficiency while reducing costs. The company operates a fully integrated production process with 420,000 tons of FBR silicon, 58 GW solar wafer, 20 GW n-type cell, and 30 GW solar module capacity, all based in China. This reduces its dependence on outside suppliers.
Additionally, GCL is increasingly automating manufacturing to ensure high-quality products with fewer chances of human errors, thus contributing to the reliable performance of modules. GCL-SI uses 24 robots in its production processes. This ensures uniform inspection of glass, cells, and backsheets, minimizing human error. Robotic machines are also used for stringing, layup, outgoing bar handling, glue cleaning, and assembling the junction box.
Their use lends consistency and reliability to the modules produced. The Chinese manufacturer is now also integrating AI systems into manufacturing processes. Malachi shared that the company uses AI-powered vision systems to inspect modules at various stages, such as after soldering, before and after lamination, and during the soldering process.
With advancements in this space, Malachi said one can expect even more innovative applications in the solar industry in the future.
GCL-SI also has an in-house lab, equipped with advanced testing equipment, credited by global certification authorities. It has tests for wet-leakage, water spray, module breakage, dynamic load test, hail test, etc. that help ensure module performance and durability.
The company uses Laser Enhanced Contact Optimization (LECO), and Super Multi-Busbar (SMBB) technology as part of its technical improvements on TOPCon cells. These enhance cell efficiency by reducing power loss, and increase its conversion efficiency by 1% to 1.5%, shared Malachi.
The use of non-destructive cutting (NDC) minimizes cell spacing from 2 mm to 0.8 mm, which enhances energy yield by reducing electrical resistance, he said.
Hangzhou First’s Sales Director Europe Bo Jin listed high degradation under damp heat for TOPCon, and moisture sensitivity for HJT as some of the major challenges for module reliability. He also recommends various packaging solutions for both G2G and G2B options that help improve their reliability.
The company analyzes different encapsulation materials for resistance to yellowing, adhesion, and PID.
For TOPCon modules, his company offers encapsulation solutions that focus on combating moisture-induced degradation (MID), while for HJT modules it emphasizes on UVID.
Specifically for TOPCon, he recommended the use of a PolyOlefin Encapsulant (POE) on both sides of the cell to improve its resistance to PID. He recommended using multilayer construction called EPE-EPE and EVA-EVA for more cost-effective applications, but with slightly less PID resistance.
For G2G TOPCon modules, POE-POE encapsulation is optimal, but for G2B, POE on the backside is seen to minimize moisture ingress, thus improving reliability, according to Bo.
He added that the use of a UV light conversion film can boost initial efficiency by 1.35% than the UV cut-off film, and the power loss is <1% in the 1st year. Overall, the cumulative power generation of the UV light conversion film is significantly higher than that of the UV through film, especially during summer.
Hangzhou First currently operates 6 production bases in Thailand, Vietnam and China with more than 380 GW of encapsulant and over 50 GW of backsheet production capacity.
Delving into a quickly growing application for modules, Technical Director of AESOLAR, Dr. Hamed Hanifi, discussed the company’s Horizon carport modules in times of growing demand for cost-effective electric vehicle (EV) charging solutions.
Hanifi emphasized that solar-powered EV charging solutions significantly lower costs, providing up to 16 times the savings compared to traditional fuels. At the same time, users benefit from reduced energy costs and faster return on investment (ROI) on their PV investments.
AESOLAR presents Horizon carport modules in 2 variants of 475 W for Germany, Austria, and Switzerland, and 590 W for the other markets. These offer up to 22.3% efficiency with M10 wafer cells and a 30-year performance guarantee and product warranty considering that these are installed overhead on carports.
Hanifi said the company conducts stringent testing for these modules under extreme temperatures, humidity, UV exposure, and mechanical loading to ensure resistance to degradation. These are also tested against impact and mechanical load standards using pendulum and weight drop tests. The Horizon modules have a narrow width to reduce central stress and increase durability.
Residential as well as commercial consumers form the target audience for these modules. AESOLAR expects to secure DBT certification for these modules by Q1 2025 for the DACH region.
CEA’s Director QA and Engineering Services, Jörg Althaus presented case studies to show the concern areas for solar module reliability, dividing these into 3 broad categories of challenges related to junction box soldering, cold soldering on cells, and glass breakage. If not dealt with, these can negatively impact project returns.
Panel discussion
TaiyangNews Managing Director Michael Schmela engaged the panelists in a discussion on ensuring module reliability in times of record-low pricing.
Joerg Althaus of quality control consultancy Clean Energy Associates (CEA) shared 3 case studies to highlight the main concern area for solar module reliability, dividing these between 3 broad categories of junction box soldering, cold soldering on cells, and glass breakage. He cautioned that if not dealt with soon, these challenges can negatively impact project returns.
Althaus believes it takes time to take something from the lab to mass production. There are learnings along the way, but as newer technologies roll in with increasing competition from several players, some companies may end up compromising with the use of materials. This negatively impacts module reliability and thereby overall project economics.
Yet, there is a growing trend of manufacturers now becoming more careful about the materials they use in terms of encapsulation and packaging since investors are educating themselves and asking for certifications and testing reports. This keeps manufacturers on their toes, which is a step in the right direction.
Hangzhou First’s Bo Jin stressed that even though lowering production costs is a common goal across industries, reliability remains the top-most factor for the PV industry. Manufacturers are also increasing their expectations for raw material suppliers to meet their reliability standards, while the latter are also developing new solutions to meet these demands.
Ingrid Haedrich of Fraunhofer ISE shared the example of backsheet failures in the past to point to the challenges in testing and ensuring long-term module reliability. She explained that in the past even IEC-certified backsheets suffered failures that were not detected under initial testing protocols. A new standard was created after 5 years when there were unexpected failures in the field. Testing is an ongoing learning process as test sequences also improve with customer feedback and the real-time performance of modules in the field.
She stressed that while testing everything would be ideal, it is neither cost-effective nor feasible. Hence, it is important to strategically prioritize testing to effectively identify critical failure mechanisms with help from field data.
AESOLAR’s Dr. Hamed Hanifi sees certification as a big challenge. While general certifications, such as those under IEC, are covered by all, it is the regional certifications that take time. For instance, to install your modules in France, you need a different set of certifications, but the same won’t work in Germany or the US. Bureaucratic problems in some countries extend this timeline. This can be resolved with political will.
Additionally, most research institutes are funded by governments that are also bureaucratic. While new technologies come in at an accelerated pace, the government is slow in enabling research institutes to get access to the latest equipment to test the new technologies and products. So, the market is faster than research institutes and testing.
The presentations can be watched here.
NEXT EVENT: On November 19, 2024, TaiyangNews will host its 1st Virtual Conference on Inverters & Battery Storage -- Technology & Application Trends for the Brain & Mitochondria of Latest Solar Power Systems. Registrations for this conference are open here.