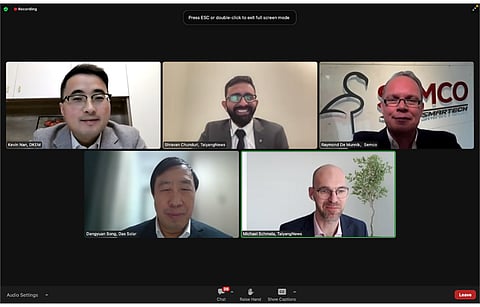
Since the start of 2022, perhaps not a single week goes by when some solar PV technology company somewhere on the globe doesn't come out with some technology update, cell efficiency record, better production methods, and the like, with cell technologies as the center of discussion.
TaiyangNews decided to bring together industry leaders and stakeholders on a single platform to see just where the industry stands today with regard to these various solar cell technologies such as TOPCon, heterojunction (HJT), and beyond, and where it is headed.
A year back during TaiyangNews High Efficiency Solar Technologies 2021 conference, TOPCon was just one of the two contenders to replace PERC in the mainstream.
A year later, TOPCon is clearly leading the race with an estimated capacity of 70 GW, its customer base is also growing with the industry touting 100 GW+ in aggregate orders. So, for our 3-day High Efficiency Solar Technologies Conference 2022, on day 1 we decided to delve deep and look at TOPCon from both the angles—cell and module technologies as well as cell production equipment and materials.
Speaking about the development of industrial high-efficiency TOPCon Technologies in the world's solar manufacturing hotspot China, Yuheng Zeng of Ningbo Institute of Materials Technology & Engineering (CNiTECH), Chinese Academy of Sciences (CAS) said the technology has quickly become popular in the country.
At this stage, LPCVD remains the most widely used deposition technique. Zeng argues that LPCVD can further increase its capacity and significantly enhance its competitiveness if it solves the problem of wraparound. Meanwhile, both tube PECVD and plate PVD need more mass production data to prove themselves, he added.
Even though PECVD is more expensive than LPCVD, in the last 3 months its cumulative order has reached 60 GW, claimed Zeng. It can very well solve the shortcomings of LPCVD route, he said.
JinkoSolar's Deputy General Manager of R&D, Oscar Zhang shared GW scale experiences of mass production of its n-type TOPCon technology that it rolls out in the form of Tiger Neo. The company sees TOPCon cell production technologies as relatively mature with yield matching that of PERC. Jinko was the first of the major vertically-integrated solar companies to jump on TOPCOn mass production and reaching two-digit GW capacities.
Zhang said JinkoSolar has been able to bring down TOPCon manufacturing costs with the help of optimizations in metallization, use of thinner and durable wafers, and capacity optimization, yet sees scope for further improvement as for the end customer as higher power output still remains the most important aspect in a module.
The Chinese manufacturer has achieved a leading 26.1% lab efficiency for TOPCon and 25% in mass production. As per its silicon solar cell efficiency outlook, JinkoSolar sees potential cell efficiency exceeding 26.5% with TOPCon+IBC (TBC) solar cells, and further growing to more than 32% with tandem solar cells, having perovskite on top and TOPCon or TBC at the bottom.
Senior Product Marketing Manager of Trina Solar David Garmendia said large wafer size helps bring down cost while referring to its n-type module. While Trina was one of the early adaptors of G12 wafer size, it recently also came out with a new size called G12R, which is rectangular with 210 mm on larger size and 182 mm on the shorter side, that is expected to combine the benefits of both G12 and M10. Though pure G12 is better from a cost perspective, G12R allows designing modules that have the same width as 182 products, thus helping to standardize modules. The company will offer the modules based on both sizes to fit each project's needs.
Betting on n-type technology, Trina Solar has started taking orders for its n-type Vertex N modules whose annual production capacity it targets to exceed 10 GW by Q1/2023, and wants to expand capacity to to between 20 GW to 30 GW in 2023.
In her presentation, JA Solar Technology's Senior Product Strategy Manager Lida Guo spoke about the challenges and industrialization progress of n-type technology.
Even though TOPCon cell line is compatible with most PERC lines, there remains a high potential for efficiency improvement since TOPCon's theoretical limit is 28.7% and its current mass production efficiency has reached 25%.
Among the challenges that Guo listed were related to realizing selective emitter, thinner poly-Si, use of better materials and better control of process, which also present opportunities to optimize TOPCon. She added that the cost reduction path for TOPCon goes through optimized metallization, scaled up production capacity, Si material cost and use of passivation and doping technology.
These efforts may lead to cost difference between n-type and p-type module to decrease by 55% in 2023 and by 90% in 2024, according to Guo.
JA Solar currently operates a pilot line of its BYCIUM+solar cell, operational since 2021. It will be expanded to a mass production annual capacity of 1.3 GW by Q4/2022 and is planned to be further expanded to 27 GW in 2023, she shared.
Reflecting the learnings of implementing TOPCon on larger wafer formats, Astronergy's Cell R&D Director Sheng He counted higher efficiency, lower production cost and mature technology as the plus points for the growth of TOPCon.
The company was able to increase the R&D efficiency of its Astro n-type cell to 25.3% and mass production to 24.8%.
In the times ahead, thinning of wafer thickness should contribute majorly to TOPCon's cost reduction, according to He, who estimates wafer cost as accounting for 81.1% of the total cost of a TOPCon cell. Currently, the mainstream thickness of 182mm wafer is 140 um and is expected to be reduced to 120 um in 2023.
Jolywood's Product Manager Ma Jiayu shared the company's proprietary plasma oxidation & plasma assisted insitu-doping deposition (POPAID) route of producing TOPCon for utility scale applications. It has helped the manufacturer increase n-type cell efficiency to the record level of 26.1% in R&D lab based on 182mm wafer size using its latest TOPCON 3.0. The key attributes of this upgrade technology are selective emitter and optimized metallization pattern, the crystallinity and thickness of poly layer and ARC coats. Since the technology was developed very recently, the company is continuing with TOPCON 2.0, both of which are based on PVD based deposition.
As for now the company has an average efficiency of 24.8% and module on offer with 570 W rated power for 144-cell confirmation based on M10 format.
The CTO of DAS Solar Dengyuan Song talked about the company's experience with n-type monocrystalline silicon bifacial solar cells for high efficiency and low cost. DAON is the company's n-type monocrystalline bifacial double glass module with a power rating ranging between 410W to 570W.
Song said the current average TOPCon cell mass production efficiency of the company's DAON production line stands at 24.8% while R&D efficiency exceeds 25%. By the end of 2023, it aims to reach 25.5% efficiency, and he sees TOPCon cell technology maturing to an industrialized efficiency exceeding 26% in the future.
Representing the equipment production side, Leadmicro's Chief Scientist (Professor) Baochen Liao reflected on PECVD based deposition solution for polysilicon layer in TOPCon mass production in his presentation.
He batted for PEALD efficiency claiming it to be slightly higher compared to PECVD deposition technology for applying tunnelling oxide of TOPCon process flow, citing PEALD+PECVD technology's ability to not affect the deposition rate with in-situ doping. It is also easy to clean compared to LPCVD.
Presenting current TOPCon cell manufacturing trends was Semco Smartech CEO Raymond De Munnik. French based Semco is a pioneer in TOPCon cell processing and has sold LPCVD equipment already to Korea's LG many years ago. While Semco offers LPCVD and PECVD deposition equipment, De Munnik said his customers prefer LPCVD. He presented a cost comparison for the costs of the TOPCon core process – tunneling oxide deposition, polysilicon deposition, doping of poly and activation – and found that the LPCVD process from Semco as well as from others have the lowest costs.
De Munnik emphasized that TOPCon is a mature technology already in 2022, with a 'big cell line installation boom' going on. Average cell efficiency has reached 24.5% in only a couple of years, and its module costs are similar to PERC.
Metallization supplier DK Electronic Materials' (DKEM) Vice President of Technology and Marketing, Kevin Nan discussed reliable metallization solutions to accelerate mass production of n-TOPCon solar cells. Managing metallization well is key for any cell technology as the material for the contacts are a major cost component. He said boron-doped p+emitter metallization helps with TOPCon efficiency.
Going forward, metallization innovation is what will accelerate mass production of TOPCon solar cells. He also stressed that resistance improvement for the rear-side Ag paste is critical to low-cost processes.
Executive Panel
The executive panel on day 1 of the conference centered around the question of why prime time for TOPCon solar has come. Speaking with TaiyangNews Head of Technology Shravan Chunduri, DAS Solar's Dengyuan Song said it was because of the solar industry being cost driven that TOPCon technology has grown by leaps and bounds in a short time, vis-à-vis heterojunction (HJT) which is expensive in comparison.
Additionally, the increase in efficiency and technological advancements along with the fact that some of the world's major players as LONGi Solar, JinkoSolar, Trina Solar among others taking serious interest in it has also helped it gain confidence.
Semco Smartech's Raymond De Munnik is optimistic of the future when the solar PV manufacturing gets decentralized with countries other than China bring online their own GW scale capacity online as is expected in the US, India, Europe and even the Middle East. Those experiences and advancements will be to watch out for.
DKEM's Kevin Nan added that apart from cost considerations one cannot really place one on the top of the other in terms of TOPCon and HJT. While TOPCon delivers on cost, HJT touts promise of higher efficiency. That can well be left to be seen in the future, but we will try to look into the crystal ball already tomorrow.
On November 24, 2022, day 2 of the High Efficiency Solar Technologies Conference will shift its focus to HJT technology with key stakeholders in this field presenting. Registrations are free and can be done here.