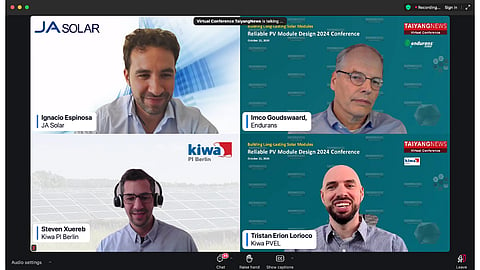
Day 1 of the TaiyangNews Virtual Conference on Reliable PV Module Design 2024 explored concerns and solutions around module reliability
Participants included module manufacturers JA, Astronergy, JTPV, backsheet supplier Endurans, and testing agencies Kiwa PI Berlin and PVEL; NREL presented field test results
The industry is at work conducting in-house and independent tests even as a rapidly changing technological space proves a challenge
Leading module players are looking for technical solutions to deliver high-reliability products as they weather huge price pressure
As solar PV technology rapidly evolves and newer products hit the market at an accelerated pace, industry stakeholders need to remain conscious of the fact that reliability is not overlooked for this commercial product that comes with average performance warranty times of 25 to 30 years.
To understand how manufacturers, suppliers and testing agencies view solar module reliability in times of record-low prices, TaiyangNews organized the 2-day Reliable PV Module Design 2024 Conference on October 21 and 22, 2024.
On day 1 of the conference, Kiwa PI Berlin’s Managing Director Steven Xuereb presented an overview of the testing quality and reliability procedures for solar modules in his keynote address. He shared that Kiwa PI Berlin conducts a thorough module quality assurance (QA) process covering the module’s entire journey from factory to field. This incorporates all the critical phases to ensure module reliability, right from procurement, pre-production, production to post-shipment.
He explained that this is because the same manufacturer may produce equipment with varying quality at its various factories with differences in the bill of materials (BOM), personnel training, equipment maintenance, and operating procedures.
Xuereb shared that even though module makers conduct a pre-shipment inspection (PSI) of their own modules when these come to the end of the production line, there exists a vast difference when an independent agency like Kiwa PI Berlin conducts the same test. For instance, he shared that out of the 774 batches of modules it tested for PSI between 2022 and 2023, the agency found only 10% or 76 batches to have no defects.
Around 25% of the defects were found in the electroluminescence (EL) category with defects like cracks, soldering effects, short circuit cells, damage to the frame, missing sealant, among others.
The tests also include post-shipment and on-site inspections using EL testing to ensure the modules were not damaged during transport as they can lead to future reliability problems post-installation.
Xuereb emphasized on raising the bar for QA of solar modules, especially in current times of increasing pressure on pricing and overproduction in the market so that modules can meet long-term performance standards. For instance, including new stress tests for TOPCon modules that can be prone to UV degradation can minimize risks related to emerging technologies, he said.
JA Solar’s Head of European Technical Team Ignacio Espinosa presented the module manufacturer’s perspective on ensuring quality and reliability while designing PV modules for long-term solar performance.
Pointing to the company’s vertically integrated supply chain, which includes 85 GW production capacity for ingots and wafers each and over 100 GW of cells and modules each, he said this helps control the entire production process from raw material procurement to the final product. This goes a long way in managing the quality, cost and production capacity more efficiently, while also allowing full traceability for the supply of raw materials.
At JA Solar, he explained, there is 100% in-house inspection where an extensive testing process is followed, including EL tests before and after lamination, to identify any defects early on. The company does 100% EL and VIS inspections in-house. There is also a growing use of artificial intelligence (AI) among module companies for defect analysis to ensure high reliability standards for the final product.
A TOPCon proponent, JA Solar expects to fully go TOPCon from 2025 as it has already shifted from producing 30% of these modules in 2023 to 70% this year to match the market demand. However, as more cell technologies come into the market, and also for various applications, manufacturers must invest more in R&D efforts to stay ahead of these technological advancements to maintain market leadership, he suggested. At JA, this is taken care of by increasing the efficiency of the manufacturing processes, strength of materials, and cheaper solutions like zero busbar (0BB), for instance.
Espinosa said that as the company deals with products that are supposed to carry a warranty of several years, it can’t afford to overlook reliability. Hence, the company maintains in-house testing facilities like EL cell test, cell thickness tester, SML, DML, and Hail Tester.
Part of China-based Chint Group, Astronergy’s Product Solution Engineer Sibin Yang presented the company’s TOPCon modules and the features that make these efficient and reliable, with reference to its ASTRO N7 and N7s modules.
A proponent of n-type TOPCon technology, Yang said Astronergy is expected to achieve a TOPCon module production capacity of 76 GW this year, with 85% dedicated to TOPCon. For solar cells, its total production capacity this year will be 65 GW, out of which 59 GW is n-type.
In his presentation, Yang showed a comparison chart of production costs for various cell technologies, including TOPCon, HJT, 0BB and TBC to prove that TOPCon has the lowest production cost compared to its peers. He especially touched upon the ultraviolet-induced degradation (UVID) mechanism to which when the module is exposed, can cause carrier recombination, reduction of open-circuit voltage (Voc), and fill factor (FF).
To protect its modules from UVID, Astronergy uses an optimized passivation film layer structure design that ensures a dense film layer, regulates the hydrogen in the film layer, improves the quality of the AIOx layer, and also regulates the hydrogen in the film layer. Additionally, the manufacturer uses atomic layer deposition (ALD), a high-precision thin-film coating technology based on chemical vapor deposition (CVD).
The use of plate-ALD cells in its high-efficiency modules decreased the UV degradation to 0.93%, thus proving its competence in providing better control over layer thickness and uniformity compared to the more cost-effective tube-ALD that some other manufacturers use. The tube-ALD is better suited for small-scale production.
Sharing an example of its in-house testing process, Astronergy subjected its TOPCon modules to degradation tests under rigorous conditions including UV60, UV120 and UV180. It found that the degradation at UV60 was 0.7%, lower than the industry requirement of ≤1%. Under extremely harsh UV180 conditions, its high-efficiency modules exhibited ultra-low degradation with a rate of 1.5%, according to Yang.
At the cell level too, its TOPCon cells show significantly better resistance to UVID compared to its peers in the market. Yang said it proves that TOPCon is currently the most reliable, stable, low-risk and cost-effective of all new technologies.
Jietai Solar’s (JTPV) R&D Manager Dr. Xinrui An discussed the reliability of high-performance n-type modules from a leading cell manufacturer’s perspective. The Chinese company currently has 40 GW of annual production capacity for n-type cells. He especially focused on the UVID, damp heat (DH), PID, and MSS tests to discuss the key challenges and solutions related to cell degradation and JTPV’s innovative approaches.
To deal with the higher degradation chances under UVID exposure, he said JTPV mitigates the same by increasing the anti-reflective coating (ARC), the refractive index, adjusting the hydrogen content in the ARC, and enhancing the AIOx layer’s cumulative field charge.
Similarly, it uses a silver paste with low aluminum content and acetic acid-resistant ARC films. An claimed that the company’s internal tests show lower DH degradation in modules using JTPV cells. Double-glass modules have inherently fewer DH problems than single-glass ones, he added.
Reflecting on PID challenges for various cell technologies in terms of corrosion were first discovered in p-type modules, An said. For all cell types, the impact is different. At the cell level, it increases SiNx conductivity and adds more conductive surface layers to reduce potential PID and for charges to dissipate. At the module and system level, its solutions include the use of encapsulation materials and backsheets with lower electrical conductivity that are also less permeable to moisture.
For the mechanical stress sequence (MSS) test, An said that his company has developed cell-level solutions to mitigate risks related to cell durability and module reliability.
An also introduced JTPV’s MoNo2 Series cells that incorporate technologies such as gradient index ARC, stack wafer deposition, emitter-metal contact optimization, and super-multi busbar (SMBB) to enhance performance and reliability.
He stressed that thanks to the deposition of a passivation film on half-cut cell edges of its MoNo 2 cells, recovery from laser damage and providing passivation is possible. These also lead to an increase of up to 6 W with HEP for standard 182-72 modules.
The Commercial Manager at US-headquartered backsheet maker Endurans Solar, Imco Goudswaard, talked about reliable and future-proof PV module packaging films while presenting the company’s coextruded polyolefin backsheet and encapsulant.
He said that with the price pressure, the thickness of traditional PET-based backsheets has reduced over time, impacting module reliability. Endurans, on the other hand, uses future-proof and cost-effective PV packaging film in the form of coextruded polyolefin backsheet and encapsulant that delivers on cost, availability, sustainability, and reliability.
Endurans is also coming up with new packaging films, namely Endurans HP – a transparent backsheet for bifacial modules, and Endurans ME – with multilayer encapsulants.
Endurans HP uses HPO technology that provides glass-like protection, but has no glass, no mesh, is low-carbon, and provides 3% more power generation compared to conventional transparent backsheets. On the other hand, Endurans ME has high adhesion, low WVTR and easy flow, and incorporates the properties of both EVA and POE.
The global testing, inspection and certification (TIC) company for the downstream solar sector, Kiwa PVEL’s VP Sales and Marketing, Tristan Erion Lorico, shared the testing results of different modules as ascertained in its 10th edition of the PV Module Reliability Scorecard released in June 2024. US-based PVEL, like Germany-based PI Berlin, now belongs to Kiwa, the Dutch certification company.
Several leading manufacturers participate in PVEL’s Product Qualification Program (PQP) which comprises comprehensive lab and field tests that aim to assess the long-term performance potential of the latest PV module designs.
Lorico’s presentation listed several testing trends across various cell technologies, including thermal cycling (TC) which helps identify cell soldering and metallization. According to the latest PVEL scorecard, updated for the third quarter, between Q3 2021 and Q3 2024, some TOPCon modules failed at 600 TC due to metallization issues, while only 1 PERC module failed. This shows that TOPCon modules may have a slightly higher failure rate under these conditions.
For hail resistance tests, glass-backsheet modules were seen to perform better than glass-glass modules. These results can help a buyer in hail-prone areas make an informed choice, he said.
Similarly, mechanical load tests showed that modules with thinner aluminum frames fail due to frame deflection. However, modules with thicker frames will be better suited for projects on tracker mounts or in areas prone to high winds.
He also touched upon the UVID issue that is known to impact module lifespan and energy output. However, he stressed that mechanisms behind UV-induced degradation are not yet fully understood, and that research is ongoing to address these issues.
Overall, the key takeaway was also that encapsulant and material choice significantly affect module performance under various stress tests, as PID tests show that 3 modules from the same manufacturer had different encapsulants, resulting in various degradation levels. Hence, the consistency of materials is an important factor in reliable module performance.
US National Renewable Energy Laboratory (NREL) Research Scientist, Silvana Ovaitt, shared field results showing the performance and degradation of bifacial solar modules. This was part of a 5-year study that compared the performance and degradation of bifacial and monofacial PV modules to stress the importance of field data.
Ovaitt said the research work shows an apples-to-apples comparison of the 2 technologies installed side-by-side over multiple years. According to the results, bifacial modules were initially advertised to yield up to 20% gains, but field data shows an average gain of around 5%.
Bifacial modules were also found to experience higher degradation rates compared to their monofacial counterparts with some exhibiting performance loss rates nearly double those of monofacial modules.
According to Ovaitt, it is important to distinguish degradation rates from performance loss rates as the latter is also influenced by environmental factors, such as soiling and tracking errors. High degradation rates significantly impact project economics, leading to lower yields than expected, and increasing costs over time.
She did add a caveat that this study is limited to a single location. It is important to cover field data from diverse environments for a holistic understanding of module durability and degradation.
Panel discussion
Moderated by TaiyangNews’ Head of Technology Shravan Chunduri, the panel deliberated on the relevance of the current solar module testing frameworks to ensure long-term reliability.
Tristan Erion-Lorico of Kiwa PVEL believes that the degradation rates are higher these days. While manufacturers quote their own degradation data, it needs to be corroborated with actual field data, but this authentic data is not available as the industry is moving very fast.
Steven Xuereb of Kiwa PI Berlin pointed out that there is a difference in the quality of modules even for the same manufacturer as several dynamics are at play here in terms of various manufacturing locations, different equipment, and staff skill-set. Hence, a lot of learning happens on the job. Testing results also vary for various new technologies.
Representing the module manufacturing segment was JA Solar’s Ignacio Espinosa who shared that the challenge is that tests and their results take time for innovative PV technologies before manufacturers undertake production. The industry is willing to do it and collaborate though.
Imco Goudswaard of Endurans agreed with the other panelists when he said that having field data on various technologies is ideal to ensure solar module reliability, but it becomes irrelevant when the technology changes so rapidly.
The videos of the presenters can be watched on our website.