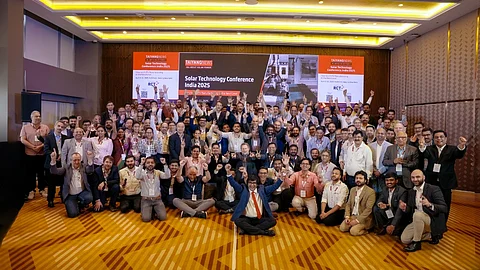
On Day 2 of the TaiyangNews Solar Technology Conference.India 2025, leading global suppliers and experts introduced cost-effective, high-throughput manufacturing tools tailored for the Indian PV market
Advanced technologies like LPCVD, PECVD and ozone cleaning are options available to manufacturers for higher throughput and sustainability
Domestic manufacturing growth is driven by PLI, clean energy targets, and rising voluntary corporate solar procurement
Day 2 of the TaiyangNews Solar Technology Conference.India 2025, on April 11, 2025, took a granular look at the materials and technologies, diving deep into components such as encapsulants, backsheets, metallization paste, and more.
It built on discussions from Day 1 on April 10, 2025 in New Delhi, India, where industry leaders emphasized the urgent need for India to invest in technological innovation, forge strategic partnerships, and cultivate a resilient ecosystem (see TaiyangNews STC.I 2025: Innovation & Strategic Collaborations Key To India’s Solar Manufacturing Success Story).
Dr. Puzant Baliozian, Sector Group Leader of German Engineering Federation VDMA, started the day with a sneak peek into the technology trends and insights from the 16th edition of the VDMA Photovoltaics Equipment, International Technology Roadmap for PV (ITRPV).
Baliozian said that according to the latest edition of ITRPV, global solar module shipments in 2024 are projected to hit 703 GW, with average spot market prices settling around $0.08 per watt. Of this volume, approximately 566 GW is expected to be installed. Crystalline silicon continues to dominate the market, accounting for 98% of total shipments, while thin-film technologies represent the remaining 2%. Among crystalline silicon technologies, n-type TOPCon has emerged as the frontrunner and is anticipated to command a 68% market share by 2025.
ITRPV officially released the 16th edition after the TaiyangNews conference (see Solar PV Industry Sets 703 GW Shipment Record in 2024).
Research Analyst for S&P Global Commodity Insights, Abhyuday Tewari, sees huge potential for solar PV technology growing in India, and also for Indian solar manufacturers to diversify to Europe. Among the various growth levers is voluntary corporate procurement, since no specific mandates exist at present. Their interest is driven by sustainability targets and cost savings. Between 2017 and 2024, corporate power purchase agreements (CPPAs) worth as much as 23 GW were signed for various technologies, led by solar.
This growing demand reinforces the case for domestic solar PV manufacturing, which in turn is supported by Production Linked Incentives (PLI) and cost advantages such as affordable labor. Complementing this are ambitious national targets, including achieving a 50% share of renewables in the power mix by 2030 and net-zero emissions by 2070.
Dr. Josua Stückelberger, Director of Technology – International Business Unit, LAPLACE Renewable Energy Technology Co., Ltd., discussed his company’s manufacturing solutions for TOPCon and other technologies. His presentation featured the company’s proprietary LPCVD technology featuring ex-situ doping. This is designed, he explained, besides the fundamental physical advantages, to help customers navigate the complex intellectual property (IP) landscape for them to accept key export markets like the US and Europe, since most IP-related concerns in the US stem from PECVD processes.
Stückelberger also stressed that the company’s LPCVD deposition system offers double-loading, leading to the highest throughput and 40% lower ownership costs than PECVD tools. He further discussed Laplace’s leading role for equipment for TOPCon plus and XBC cells with the novel TOPCon plus process flow, unlocking a conversion efficiency gain of ~0.45%, which translates into a 9W gain in module power.
Pon Ramesh Chelladurai, Director of Sales and Service at Jinchen Machinery Co., Ltd., presented the company’s advanced turnkey solutions for high-efficiency solar cell manufacturing at the conference. He said that the company’s 3-in-1 tube PECVD technology enables efficient PERTOP and TOPCon solar cell manufacturing by integrating a-Si:H deposition, doped layer formation, and ultra-thin SiOx tunnel layer. It has been successful in production lines, ensuring high throughput and uniformity.
He also offered a virtual walkthrough of the company’s detailed factory layout and outlined readiness for TBC and tandem cell production. Chelladurai also emphasized the importance of collaborating with academic institutions and research centers.
Chinese HJT solar cell equipment supplier Maxwell’s Overseas Sales VP, Peter Stamm, discussed the company’s high-efficiency and low-cost HJT full-line solutions at the conference, including its XDL series. He acknowledged that while silver availability is sufficient for TW-scale production, its cost remains a challenge given the price-sensitive nature of PV. While HJT is known to be a large consumer of silver, Stamm said that HJT offers a cost edge of 0.1 RMB/W in silicon compared to other technologies. Maxwell views HJT as an ideal partner for perovskite in tandem solar cell production due to this economic advantage.
Solar cell metallization manufacturer Solamet’s VP of Technology—Overseas, Kaien Chang, highlighted the importance of frit optimization on PERC and TOPCon rear side fingers, using the company’s proprietary Pb-Te-O chemistry. For TOPCon front-side finger, he said there may be an efficiency compromise of up to 0.05% to 0.1% based on different p+ emitter or LECO process parameters, if we need to consider reliability performance like acetic acid resistance.
He also stressed that module BoM choices, such as double-glass/glass-backsheet with EPE/EVA, significantly influence overall reliability.
Dr. Damian Brunner, Senior R&D Manager Solar & Battery, RENA Technologies, highlighted the company’s ozone cleaning solution as a cost-effective alternative to conventional methods used in China, providing a cost-of-ownership (CoO) advantage.
Unlike conventional pSC1 cleaning (KOH and H₂O₂) commonly used in China, Brunner said that his company’s method reduces the number of cleaning steps from 8 to 7 and significantly lowers the consumption of HF and KOH. While the ozone system entails higher initial capital expenditure, Brunner pointed out that its operating costs are minimal – limited primarily to electricity and oxygen – and it generates no chemical waste, leading to substantial long-term savings and reduced overall operational expenditure.
Manjunath Jyothinagara, MD, UHP Technologies, stressed the significance of utilities in building India’s solar cell manufacturing ecosystem in his presentation. He emphasized that clean rooms are essential for maintaining high-quality standards in solar PV manufacturing. However, he cautioned that projects often face delays when cost-cutting overshadows the need for efficient and timely factory execution, and recommended that companies not sacrifice factory efficiency with their overemphasis on CapEx.
Chen Kin Lee, Deputy General Manager at Jinchen, introduced the company’s latest intelligent manufacturing solutions for India, including a Cell Unpacking Machine, SMBB Scribing & Welding and Stringing All-in-One Machine, and an Auto Layup with an integrated Bussing system. He noted these systems can be retrofitted into existing production lines, as long as sufficient space is available. Chen said these solutions offer competitive advantages of CapEx reduction, low damage rate, and wide compatibility with zero busbar (0BB) and multi-busbar (MBB) technologies to meet evolving industry demand.
The CEO of Mondragon Assembly India, Manu Gaurang, introduced the company’s multi-stack pad-press laminator designed for the Indian market. He highlighted its key features – no bending, delamination, or edge pinching – ensuring high reliability. Gaurang emphasized its long-term OpEx benefits, costing around €2.5 million/GW over 5 years and nearly €8 million/GW over 10 years, and called it a ‘future-proof investment’.
Presenting smart solar stringer machines from ConfirmWare, Dronveer Kaura, Representative of India Market, said these offer high flexibility and compatibility with all 3 0BB routes. According to Kaura, the equipment allows seamless switching between configurations, allowing manufacturers to stay future-ready, reduce costs and improve efficiency. Pioneering tunnel-type temperature control system guarantees module yields and high output, he added.
Encapsulant materials and solutions provider for advanced solar cells/modules, Hangzhou First operates an annual production capacity of 400 GW of encapsulants and 50 GW of backsheets from its 6 production bases in China, Vietnam and Thailand. InYoung Suh, Director of Business Development, Hangzhou First, stressed the significance of choosing the right encapsulant as these play a big role in PV module durability and degradation. Backed by test data, Suh recommended POE for glass-to-backsheet configurations and promoted the company’s high reflective black backsheet (HRBB) as an ideal solution.
Alishan Green Energy’s AGM, Business Development, Dr. Khushbu Patel, discussed the company’s offerings as a budding encapsulant supplier to the Indian solar PV industry. With its 4.2 GW of encapsulant and 3 GW of coated backsheet capacity, Patel called her company one of the largest manufacturers of these components in India. It aims to reach 18 GW production capacity by 2027-28, addressing the 70% demand-supply gap in India’s encapsulant market.
With an annual production capacity of over 40 GW for PV junction boxes, cables and connectors, DhaSh PV Technologies is now scaling up to a whopping 63 GW manufacturing capacity by 2025, which it claims will make the company the ‘largest’ non-Chinese-owned PV junction box manufacturing company in the world. DhaSh PV Technologies CEO Bhupendra Singh Rawat and GM-Business Development Mohammad Asif Patel shared the advancements in PV junction boxes. They especially highlighted DhaSh Trio’s design, ensuring compatibility with high-Isc modules like G12R & G12, and preventing the module’s operating current from exceeding the Junction Box's rated current.
Executive panel
India’s rising status in the global solar PV sector is drawing comparisons with China, the US, and Europe, pointed out the executive panel of Jakson Solar Module & Cells CEO Anurag Garg, Landsmill Group CEO Sandeep Garg, InSolaire Energy Limited CEO Sunit Tyagi, in conversation with RCT Solutions India Sales Director Sukumar Madugula and TaiyangNews MD Michael Schmela.
Industry leaders stressed the need to position solar as a long-term, stable investment for investor confidence. They also cautioned against fueling fears of new technologies disrupting existing setups. They believe that PERC technology still holds value even as TOPCon becomes more common, and newer technologies make their presence felt.
Going forward, there is a need to disseminate awareness and education regarding solar as a business among policymakers to sustain balanced solar growth, the panel noted.
TaiyangNews ran a live blog on both days of the conference which can be reviewed here. High resolution pictures from the event are available on the STC.I 2025 website.