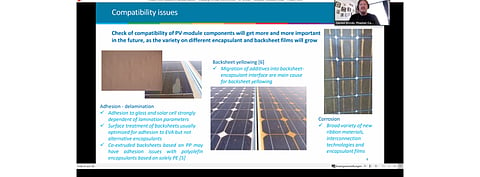
The main purpose behind all new developments in the space of solar PV technology is to finally bring down the levelized cost of energy (LCOE) without compromising on the quality and reliability of the system installed. That's where testing of all the ingredients that make up a solar PV module becomes all the more significant, to ensure it functions well to the end of its life. This was the focus of a presentation that Dr Gernot Oreski of Polymer Competence Center Leoben (PCCL) shared during a virtual conference of TaiyangNews on Reliable PV Module Design held online on October 9, 2020.
The PCCL Division Head of Smart Materials, Oreski stressed on extensive testing of all actual samples of a PV module at every step of the way, be it resins or laminates or even the complete module itself, before these are introduced to the market.
He offered an interesting rationale for this argument. Pointing at the wide array of module components available in the market from a variety of suppliers, Oreski argued, it is important to ensure compliance of these various elements—including encapsulant and backsheet films—with each other to make sure the end product has a strong, durable design to last the module a lifetime. "Design matching of components and materials may reduce degradation rates or avoid certain degradation modes," he pointed out.
It is going to become all the more important in the future as the PV technology market continues to grow. For instance, testing of polymer films can reveal principal chemical, physical and mechanical properties and intrinsic degradation behavior of the polymers, similarly testing of laminates can help give insights into material interactions and compatibility issues as discoloration, corrosion and adhesion. Dr. Oreski did caution that one must test a sample instead of exposing the full product to accelerated weathering test.
Along with polymers, he also pointed out the gains and misses from testing at different levels. For instance, failure of a c-Si PV module is mostly avoidable at module lamination and component selection stages provided the manufacturer conducts extensive R&D, quality and reliability testing. When it comes to the material itself, degradation can be delayed to some extent with proper stabilization. Therefore, testing at every level is crucial.
Testing should be attempted in what he suggested a pyramid model, with material or film supplier testing the raw material at their end. For a module manufacturer though testing should begin with the film being used, work its way up to lamination, mini module and module levels.
Testing process is not just time consuming but also involves a cost which a manufacturer needs to factor in. Oreski did add that of late there is more awareness among material and module producers to expose their products to advanced test procedures to ascertain material interactions and their incompatibilities. Simultaneous combined or sequential stress tests are now offered by agencies as the National Renewable Energy Agency (NREL), and PVEL.
A recording of Dr. Gernot Oreski's full presentation including Q&A during the TaiyangNews conference is available at our YouTube channel here.