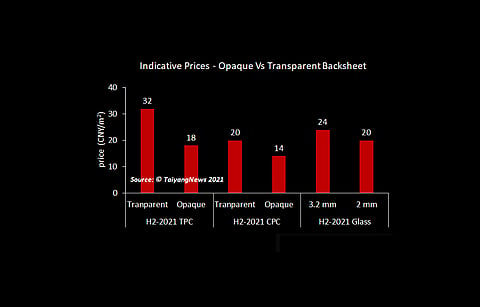
Backsheet prices are very much dependent on the polymer chemistry used for building different layers, also the case with transparent backsheet. And making film-based transparent backsheets requires all components such as the outer protection layer, PET, inner layer if applicable, and glue to be transparent, all while maintaining the same UV protection attributes. All this not only makes for a complex backsheet making process, but it also makes the final product expensive. Film-based transparent backsheets are about 80 to 90% more expensive than their opaque counterparts. For example, the TPC transparent backsheets sold in H2/2021 for about 32 CNY/m2 CNY against 18 CNY /m2 for the opaque one.
Making transparent fluorine coatings based backsheets on the other hand is easy and low cost. Moreover, the base value for opaque CPC backsheets is also low, so making transparent CPC backsheets cost competitive to glass is relatively easy. In H2/2021, the price of a CPC transparent backsheet was pegged at about 20 CNY/m2 while an opaque backsheet of the same configuration costed about 12 to 14 CNY/m2. In comparison, prices for 2 and 3.2 mm glass were 20 CNY /m2 and 24 CNY/m2, respectively, meaning there needs to be a further 15 to 20% cost reduction to make it lucrative.
Still, transparent backsheets make a strong business case in a few markets, according to Cybrid's Marketing Director Xinjun Li. He takes Turkey as an example, where importing glass from China is a costly affair. "For such markets, transparent backsheet is much better," said Li. In addition, Cybrid also sees potential for transparent backsheet in the C&I rooftop markets with flat roofs and moderate weather conditions(see Discussing Solar Backsheets & Encapsulation Trends).
All component suppliers and most backsheet manufacturers are offering solutions suitable for transparent rear covers. Starting with component suppliers, DuPont has been offering Clear Tedlar. Fumotech has developed several generations of transparent PVDF and the product accounted for 20% of its shipments in 2020 and 13% during the first half of 2021. ZTT has started supplying transparent PVDF with its shipments reaching about 1 million m2 so far. DTF has also added a range of ultra-clear products to its Mylar UVHPET portfolio for bifacial applications. The films are designed to be used as outer, inner or mono layers in transparent backsheets.
Jolywood was one of the first companies to offer transparent backsheet products, based on the TPC configuration, but its main product is CPC. Lucky Film was also one of the frontrunners to bring a transparent backsheet to the market, based on Tedlar. And while Cybrid was mainly promoting its famous KPf structure till last year, the company has now shifted its focus to coatings-based solutions for transparent backsheets. For applications in extreme weather conditions, for example requiring high abrasion resistance, the company has developed special abrasion-resistant hard coatings that can be applied on top of the regular fluorinated coatings. This additional 5 µm costs 1 CNY/m2 extra over the base CPC price of a backsheet, according to Li. The main products for Coveme for transparent backsheets are PET and Tedlar based, including an option for primer or coating on the cell side (see So Many Backsheet Structures).
These are only a few examples, as every major backsheet maker is promoting a transparent variant of its leading backsheet configuration. The only exception is Endurans. According to Annet Hoek, Global Communications & Branding Lead, Endurans, it is one of the products in its development pipeline. While it is not difficult to introduce a transparent backsheet for the company, given its polymer engineering background, Hoek underscores that the high internal testing standards take time in order for such a product to be endorsed under the Endurans brand.
Apart from the polymer chemistry, the transparent backsheet has another interesting variant that is actually aiming to alleviate one of the inherent limitations of the bifacial technology, i.e., the front power of the bifacial module is less than that of its monofacial variant. The inter-cell spaces of a monofacial module are white, which reflect the light hitting these spaces onto the active surface, enhancing optical gains. Bifacial, with its transparent rear cover, lets the incident light on these inactive areas to simply pass through, thus missing out on any such gains. To overcome this limitation, backsheet makers borrowed an idea that was initially introduced by the solar glass segment. They are offering a tailored product that remains transparent in those areas where the cell will be placed while the inter-cell spacing area is printed with a white reflector. Such backsheets are referred as "grid" and/or "patterned". This way, a bifacial module looks like a monofacial panel from both the sides and the white reflector assumes the role of reflecting incident light on inter-cell spacing. All major companies are offering such custom-made backsheets tailored to match the different cell sizes and module designs of individual manufacturers. The additional costs for applying grids are about 2 CNY/m2. However, the acceptance for such products varies from company to company. Jolywood, with a share of 70% for grid applied products within its transparent backsheet sales says the industry well received the product. On the other hand, Hangzhou First and Lucky Film have not observed huge demand for such products. Coveme did see an increase in demand in the beginning of 2021, but not so much in the second half.
There is one other variant of the grid backsheet that is getting popular – changing the color of the grid from white to black. This is especially from module makers that are making black modules. Such modules typically employ black backsheets which add to the aesthetics quotient of the backsheet. Since bifacial cells are priced the same as monofacial cells, using a white backsheet is always beneficial versus using black backsheets, as some portion of IR light that passes through the cells can be reflected back when the rear cover is white. Using white backsheet with black grids solves both the purposes – function and form. According to Cybrid's Li, the approach improves the module power by about 4 W.
The Text is an excerpt from TaiyangNews' recent Market Survey on Backsheet and Encapsulation Materials, which can be downloaded for free here.
An overview of the survey was presented during TaiyangNews Conference on Reliable PV Module Design. To learn more about the conference and view the presentations click here.