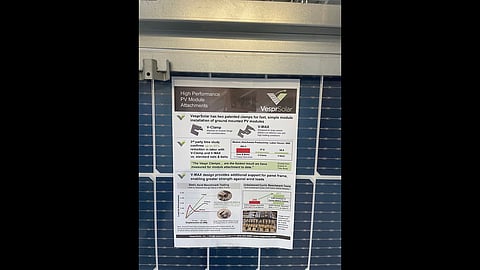
VesprSolar displayed its V-Clamp and V-MAX series PV module mounting clamps, suitable for fixed-tilt and 1P tracker-based installations, respectively, during the show
According to the company, the clamp-based mounting technique reduces labor manhours compared to the traditional nut-bolt-based method
It claims that its clamp-based mounting systems enhance static mechanical loading of the installed modules vs. bolt-based mounting
Traditional bolt-mounted PV installations, requiring precise torque settings, often experience over-tightening or loose clamps due to strong wind gusts or possible poor workmanship during installation. VesprSolar, a US-based company, developed its V-Clamp and V-MAX series mounting clamps, which utilize a snap-in technique, to address these shortcomings.
At Intersolar Europe 2025, the company displayed the 2 products at its booth. The V-Clamp is aimed at fixed-tilt tracker-based installations and the V-MAX series at 1P (1-in-Portrait) applications. Their advantages can be broadly classified into 2 key metrics – cost-effective & installation-friendly and enhanced mechanical endurance.
Designed to be attached along the length of a module frame with standard pliers, these clamps provide mechanical fastening with mounting structures in a short duration compared to nut-bolt-based installations. Instead of yellow-green copper wire-based module-to-module grounding, its mounting clamps, featuring a threaded groove design, ensure equipotential bonding between the anodized aluminum frame and mounting structures. The company said that this clamp system reduces installation times compared to the nut-bolt-based method. It further shared an independent third-party time study report to quantify its claim. The results showed 37.8 and 38.9 manhours for V-Clamp and V-MAX systems, respectively, compared to the nut-bolt-based mounting’s 104.3 manhours for a 1 MW project.
According to VesprSolar, these mounting clamps, when paired with mounting structures, improve the module’s rear-side mechanical loading capability. Typically stemming from wind load, rear-side mechanical loading can be both static and dynamic in nature. The company conducted a static axial benchmarking test on a 665 W PV module, evaluating the maximum displacement (in mm) of different mounting clamps integrated with the module’s aluminum frame under increasing static axial load. In this test, the aluminum frame is tested for the maximum static axial load until it breaks. The test results showed that the V-MAX clamp-based PV frame could withstand up to 4.45 kN of axial force, compared to 3 kN for the V-Clamp and 2.6 kN for an M8-bolt-based variant. The company also conducted a benchmarking test to assess module failure under unbalanced dynamic cyclic load conditions, typically common for utility-scale tracker installations. The test, comparing a V-MAX clamp-mounted 665 W module to a bolt-mounted module, showed that the former endured 887 unbalanced load cycles, against the latter’s 245, before failure.