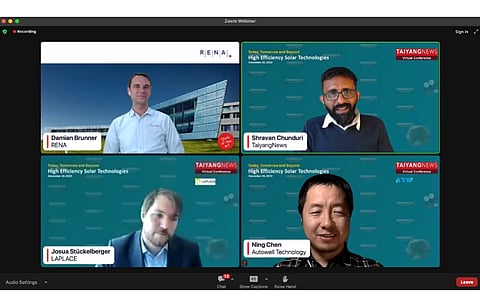
After day 1 and day 2 of TaiyangNews High Efficiency Solar Technologies Conference on TOPCon and heterojunction (HJT), day 3 of our annual flagship event continued the discussion on the fastest growing solar PV technology today, TOPCon.
Day 3 of the conference on December 19, 2023, had leading solar module manufacturers as well as production equipment suppliers in attendance.
In his keynote, the Steering Committee Chair of ITRPV Markus Fischer presented an overview of high efficiency solar developments. He expects around 400 GW of new module shipment volume in 2023 with an average module spot price of $0.12/W. The price forecast dropped from $0.23/W earlier, thanks mainly to the huge module, cell, and wafering capacity in the market.
ITRPV believes shipments will continue to increase continuously while price reduction will also continue unabated. It is clear that p-type PERC as the industry's workhorse of recent years will continue to lose market share while n-type will gain market share faster than expected and become a dominant technology after 2026. TOPCon on n-type is the most promising successor.
Among new wafer formats, M6 will disappear from the market soon while M10/G12 will dominate. Polysilicon consumption/W with regard to different wafer sizes is still being ascertained, but it's clear that its use will come down in the future as manufacturers reduce thickness, kerf loss and go for process optimizations. ITRPV assumes a decrease from over 2.2/W for G12 wafers in 2023 to below 1.6/W by 2033 for average polysilicon consumption in PERC.
As silver becomes more expensive, now at $0.76/W cell, its use in the PV industry will continue to come down. Currently, HJT and TOPCon consume significantly more silver—16 to 20.6 mg/W and 12.3 to 14.6 mg/W, respectively—than PERC which consumes 5.6 to 9 mg/W for tier 1 manufacturers. It can come down by reducing finger width and increasing busbars. Screen printing will continue to dominate while the market can make plating feasible. Fischer shared that the laser-enhanced contact optimization (LECO) technology developed by Qcells and Cell Engineering can boost efficiency by reducing resistance between the contact and silicon. It can contribute significantly to reducing the use of silver in metallization. Fischer, who is also VP R&D Operation at Hanwha Qcells GmbH, emphasized that his company is ready to license the technology to interested parties.
According to ITRPV's forecast for cell efficiency trends, n-mono TOPCon has already reached a level of 25%, growing faster than its anticipated target of 2027. For tandem, the efficiency will reach 27.5% in 2027 and 32% in 2033, paving the way for these to enter mass production after 2025. In terms of module efficiency, tandem is expected to enable over 26% after 2025.
Fischer said single junction cell efficiencies are reaching the practical limit in production.
Sharing the company's experience in adapting TOPCon to rectangular wafer formats, Trina Solar's Product Manager Lukas Chao Ye pointed out that the levelized cost of electricity (LCOE) has come down by 84% from 2009 to 2022. Among the major drivers of this reduction are large wafers, high-efficiency cells, high string power, and the like.
Trina, along with some other leading module manufacturers, is working on a standardized medium module size of 2,382 x 1134, 210 x 182 mm, or the 210R with R standing for rectangular size. Larger modules of 210 x 210 mm follow the 2,384 x 1,303 mm size.
The 'founder' of the rectangular 210R cell and medium-size module, Trina has shipped over 15 GW of these modules and has a total capacity of 30 GW.
According to Chao Ye, the total production capacity of rectangular solar cells of tier 1 manufacturers had grown to 84 GW in 2023, while these companies rolled out 14.5 GW capacity. In other words, over 80% of the new TOPCon capacity is rectangular cells today. In 2024, he expects the combined capacity to grow to 420 GW with actual output between 200 and 300 GW, which will ensure it is now a mainstream module size.
Taking a long-term view through to 2027, 210 large wafer technology will cover PERC and TOPCon, and also dominate the technical path of HJT, said Chao Ye.
Trina produces solar modules with up to 710 W output with its i-TOPCon technology. In the future, it aims to bring the i-TOPCon Ultra/Tandem configuration. It targets a full frontal passivation contact i-TOPCon cell technology of over 27% efficiency, along with i-TOPCon+ tandem cell technology with a cell efficiency of over 30%.
The Chinese manufacturer says it will exit 2023 with a cell production capacity of 75 GW, comprising 40 GW of n-TOPCon capacity, 50 GW silicon wafer and 95 GW module capacity. Further investments are being planned to expand from here.
Tongwei Solar's Director of PV Module R&D Department Jason Xia discussed the downstream technology development of the world's leading silicon producer with 420,000 tons/year of polysilicon production capacity. Currently, it has an annual capacity of 15 GW of monocrystalline wafers, 90 GW of solar cells, and 55 GW of PV modules. It plans to expand its module capacity to over 100 GW in the future.
Staking claim to having developed the industry's 1st large wafer size PECVD polysilicon technology route, Tongwei started its Tongwei n-type passivated contact cell (TNC) cell research in 2020. At the end of October 2023, it achieved an average cell conversion efficiency of 26.1% from a mass-produced TNC cell, corresponding to a module power of 585 W based on M10 72-cell based panels.
It has also launched a 620 W G12R TNC module with up to 23% efficiency. These, according to Xia, can bring down BOS costs by over 1% compared to G11L. Tongwei is also present in HJT technology. Its latest HJT product is the THC module 730 W G12-66 series with no silver use and up to 23.5% efficiency. It uses its in-house copper interconnection technology to replace silver for the HJT cell.
DAS Solar's Overseas Technical Support Manager Alex Chen discussed the company's experiences in commercializing TOPCon technology. With 30 GW each of TOPCon cell and module production capacity, the manufacturer aims to exit 2023 with an average mass production cell efficiency of over 26% for its DAON cells with mainstream module power of 72-cell modules exceeding 595 W.
With a strong TOPCon product portfolio, Chen said the 3 key technologies that the manufacturer uses for its DAON 4.0 portfolio are electrode shaping, zero busbars (BBZ), and high-throughput carrier injection. It uses dual POE packaging to ensure a reliable product with aging, water, insulation and PID resistance.
DAS Solar's technology roadmap targets to achieve up to 27% TOPCon cell efficiency for its D-TOPCon 4.0, while the target is to reach up to 28% cell efficiency for TBC.
Like most leading cell and module companies, DAS Solar also plans to enter the tandem domain with over 30% efficiency for silicon and perovskite combination along with carrier-selective passivating contact solar cell (D-CSPC) efficiency of between 27% and 28% by 2025.
SolarSpace's Director Jeremy shared the characteristics of the company's bifacial TOPCon cells during his presentation. Having ventured into module manufacturing only in 2021, SolarSpace, one of the global leaders in cell manufacturing, supplies 182 and 210 wafer and rectangular wafer TOPCon cells to leading module makers with its 50 GW annual cell capacity.
It launched a 182 TOPCon cell with 24.8% efficiency in 2022, followed by a 210 TOPCon cell with 25.87% efficiency in 2023. Compared with the 70±5% bifaciality of PERC cells, for TOPCon cells it is higher at 80±5%.
For a TOPCon cell, a good cell binning method after flash and well-designed EL/VI criteria will help prevent defects such as dark spots, poor etching, cell pollution, cell cracks and cell fire marks, added Jeremy.
Jolywood Solar's Senior R&D Director Keng Siew Chan discussed efficiency improvement technology of industrial production for TOPCon solar cells within the C-Chinese company that's known as a pioneer and very early adopter of n-type technology.
A proponent of the PVD deposition technique for TOPCon cells due to its in-situ doping, low-temperature deposition and no wraparound characteristics, Jolywood initially started with LPCVD for its J-TOPCon 1.0. Later, for J-TOPCon 2.0, it used sputter deposition for the poly-Si layer.
It has also developed a new type of metallization technology code called JSIM using a new paste system. This has improved TOPCon solar cell efficiency by 0.3 percentage points, along with module reliability as per the manufacturer's in-house tests.
Going forward, it aims to achieve over 26.5% cell efficiency for its J-TOPCon new cell while simultaneously aiming for over 27% efficiency for J-TBC with back contact cells, which should be ready for pilot production in 2024.
LAPLACE's R&D Manager, Europe Josua Stückelberger talked about the role of LPCVD and thermal processing tools in the wider deployment of TOPCon. The company supplies turnkey solutions for TOPCon, IBC, TBC and other passivated contact solar cells, and has supplied over 200 GW production lines so far, with 18 GW delivered outside China in Vietnam, Malaysia and the US. It has offices not only in China but also in the US, Greece, France, Malaysia, Vietnam, Hong Kong and Taiwan.
While moving from PERC to TOPCon, one of the big challenges was related to boron diffusion and getting good homogeneities in large batches and reproducibility. Stückelberger said his company's BCl3 as the gas source for boron diffusion could lower the consumption and lower the by-product B2O3, which significantly lowers the maintenance for quartz parts.
"With these 2 effects, we were able to reduce the operating costs for boron diffusion by 70% which was a big driver to make TOPCon possible," explained Stückelberger.
The manufacturer created the double paddle quartz tube to ensure no direct contact takes place between quartz boats and quartz tubes, which improved heat uniformity leading to longer quartz lifetimes, higher throughput and lower OpEx. It also commends itself for pioneering the horizontal wafer placement process for better process uniformity.
In the long term, Stückelberger sees LPCVD as favorable compared to Tube PECVD for the TOPCon process due to better SiOx quality improvements in the quartz lifetime and lower operation costs. Nonetheless, he added that there is little change in process flow between LPCVD and PECVD deposition methods.
The Laboratory Director of PV equipment maker Autowell Technology Ning Chen presented the company's metallization and interconnection solutions for TOPCon cells and modules during the conference. His focus was on screen printing, fast firing, IV testing and sorting, laser cutting and soldering processes for TOPCon cell manufacturing.
Autowell's screen printing line, with its high-speed linear motor and DD motor, is suitable for large-size wafers that are fast gaining market share, shared Chen. It promises a throughput of 9,000 wafers/hour with a cycle time of 0.8 seconds.
Chen introduced the company's new products for both p-type as well as n-type cells – a firing and passivation furnace that increases efficiency and leads to stable performance that's free of LID and LeTID effects.
Citing front-side related losses as the bottleneck for the efficiency of TOPCon cells, Chen introduced his company's laser-enhanced metallization (LEM), claiming it can improve the front contact resistance and contact recombination leading to efficiency improvement of 0.2% abs~0.3% abs on TOPCon cells, mainly from Voc and FF gains.
Germany-headquartered wet chemical solutions provider RENA Technologies GmbH's Senior R&D Manager Solar & Battery Damian Brunner presented an overview of wet-chemical solutions for n-type cell processing.
Brunner called wet-chemistry one of the key technologies, especially for TOPCon since 5 out of 15-18 steps of its production are related to wet-chemicals (wafer and cell processing). He said optimizing the interconnections can reduce OpEx and gain performance for this technology.
The manufacturer says most of its products and processes are demonstrated to perform at efficiency levels surpassing 25%. It is now getting ready to launch additive solutions comprising customized texture and cluster additives.
Executive Panel
Moderated by TaiyangNews Head of Technology Shravan Chunduri, the executive panel discussed the learnings with regard to the perfect design for TOPCon cell and module manufacturing lines.
Damian Brunner of RENA Technologies said when preparing for TOPCon production, the effort shouldn't be all in the direction of improving efficiency alone. Bringing down costs is equally important which can be managed by focusing on reducing electricity and maintenance costs. These, he believes, hold a significant potential to lower overall costs for TOPCon manufacturing.
LAPLACE's Josua Stückelberger recalled that the move towards PECVD was facilitated by a shortage in quartz supply. Now, there are customers trying out PECVD but it is not yet a move away from LPCVD.
He sees the LPCVD system offering a more stable, mature and homogenous layer, compared to PECVD where the silicon oxide layer is the most challenging in terms of homogeneity and thickness at this stage.
Autowell Technology's Ning Chen explained the company's rationale for moving into screen printing, expanding from stringer production. Depending on customer needs, the manufacturer wants to be ready to provide all integrated solutions, hence the move. It is also good for the business.
All the 3 panelists were unanimous in their opinion that TOPCon has a long way to go in terms of efficiency improvement. As more technological advancements take place, it will continue to get better and maintain its leading position compared to other technologies. HJT can co-exist with TOPCon, but it will need to prove its competitiveness in economic terms to take over from TOPCon in the future.
Day 4 of the TaiyangNews High Efficiency Solar Technologies Conference delved into back contact (XBC) and next generation technologies. Day 1 focused on TOPCon and day 2 on HJT technology.