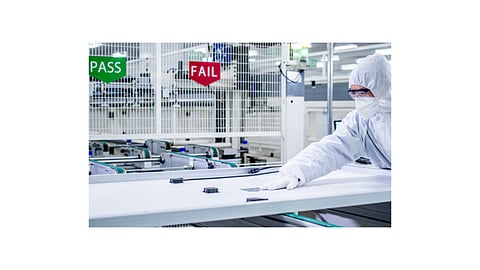
Solar is always good for surprises, indeed – not only when it comes to larger market growth or faster cost and price reductions than anticipated. Even in the field of module technology, where you would think that the development paths are clear and easy to foresee, suddenly things can pop up you would have not necessarily expected.
A year ago, when we published our 2nd Advanced Solar Module Technology Report, the module evolution path seemed obvious – standard modules would mostly adapt 5-busbar technology, while (what we call advanced technologies) half cells, multibusbar as well as bifacial and thus glass-glass would continue its rapid market expansion. Indeed, that has been more or less happening.
However, there were already first signs of a different development – towards larger wafers, a simple way to increase module power ratings, the key metric developers/EPCs use to compare solar panels. Several companies' 72-cell module products exceeded the 400 W level last year primarily for one reason – larger wafers than the 156 mm side length products (so called M0 format) that have been a standard for more than a decade, which was slightly increased to 156.75 mm recently. The first to break out of this 'dimension' was LG, which introduced in 2017 a wafer format of 161.75 mm (M4) for its n-PERT cell technology. In 2018, JinkoSolar started offering its Cheetah module series based on 158.75 mm wafer sizes (M3). When we saw Canadian Solar's multicrystalline product exceeding the 400 W level in last year's edition, we first stumbled, but the reason was the use of even larger wafers with a side length of 166.75 mm (M6). Now, the world's largest mono wafer manufacturer LONGi has jumped on this train, also pushing M6, which has enabled its module subsidiary LONGi Solar to offer a half-cell based bifacial product with a front side power rating of 435 W; that's 25 W higher than last year's edition's most powerful module of 410 W, although the LONGi module uses today's standard cell product PERC, and not any high-efficiency cell technology.
The other surprise is the strong interest in so called paving modules. While most PV related technologies were developed in the western world before they spread to the east, paving is a proprietary technology developed in China. Here it is all about reducing the gaps between cells. In other words, paving could be also described as an intermediate between half cells and shingled modules, that combines the benefits of half cells with the aesthetics of shingled cells, but without the complication of gluing parts of the cells together with rather expensive conductive adhesives. Joy-Tech, the inventor of this technology offers a complete technology pack including stringing machines, although – as is typical in China – other equipment manufacturers have apparently already found 'alternative' ways to produce paving modules. However, although still in a pre-commercial stage, several module manufacturers are already planning to introduce paving products, including JinkoSolar, which calls the technology 'tiling ribbon' and plans to launch a 460 W module that comes with 158.75 mm large PERC cells and combines half cells and MBB.
In our report, we have looked at each of the advanced technologies individually, but such products are less and less available. The huge advantage of advanced module technologies is their ability to be combined with each other (except for shingled and paving technology). Thus, combining these technologies is the recipe for higher power ratings of future solar module designs.
It is still difficult to say what's the winning combination, because that will depend on a vertically integrated manufacturer's cell portfolio and the application. For sure, high-efficiency cells will be combined with multi busbars and half-cells, and as they are naturally bifacial this feature will be generally utilized as well.
If bifacial will stay mostly a glass-glass product or rely on glass-transparent backsheet design is still too early to say. But the 30-year performance warranties now offered by the first module suppliers of glass- transparent backsheet products will back this option. Although in the end, as usual with solar modules, success will depend mostly on cost and price and of course application, because both glass-glass and glass-transparent backsheet have their pros and cons.
We have again listed the top commercial advanced 60- and 72-cell (and equivalent half-cell) modules in tables and graphs (see p.60 and p. 61), with the best modules for this number of cells reaching power ratings of 380 W (REC) and 440 W (LONGi Solar & Solaria), respectively. However, apple to apple comparisons are not possible as companies not only use different advanced module technology combinations for their products but also different wafers sizes. Here, standardization would be helpful (also regarding module dimensions to keep cost as low as possible for everyone in the value chain). But this seems unlikely as Zhonghuan Semiconductor just announced it will introduce next year even larger wafers up to M10, which equals 210 mm side length.
It appears there is only one way to compare advanced modules easily – and that is by module efficiency in combination with power output. This way, REC's half-cell HJT Smart Wire MBB module tops the 60-cell category with 21.7% module efficiency and 380 W power rating. However, in the end it is great that there are so many different paths to increase module power rating levels – and it is happening so quickly all across the board. We are already looking for the next surprises.
This article is the conclusions part of our TaiyangNews Advanced Module Technologies 2019 Report, which was released in September 2019 and can be downloaded for free here.