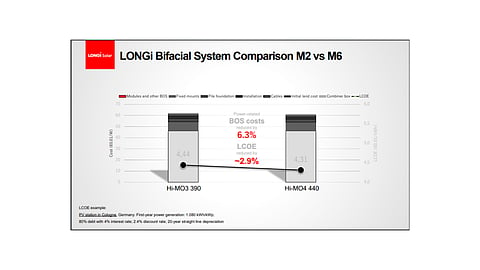
One of the most straightforward and simplest ways to increase module power is to use large cells that in turn means employing larger wafer formats. Indeed, increasing module power using larger wafers is a very hot topic in today's PV module manufacturing world. Though the approach does not involve any technical superiority, increasing the wafer size is a simple trick to boost module power. That is why we included the phenomena using larger wafer formats as one of the seven advanced module technologies in our TaiyangNews Report on Advanced Module Technologies 2019, which can be downloaded for free here.
In November, TaiyangNews also hosted a webinar on Larger Wafer-based Solar Cells and Modules – Solar Industry Trends to Design Modules with Higher Power Ratings. Followed by a brief introduction about larger wafer formats from TaiyangNews based on the Advanced Module Technology report, the webinar featured talks from an industry prospective. Winfried Wahl, Head of Product Management & Chief Engineer at LONGi Solar, a leading module manufacturer and part of the LONGi Group, which is the world's largest monocrystalline wafer manufacturer, presented about the value proposition of PV modules based on larger wafer formats, while Vincent Lau, International Sales Director at Aiko Solar provided insights from the perspective of a leading cell manufacturer.
The trend towards larger wafers started last year
The idea of increasing the wafer sizes is anything but new. A few cell producers made unsuccessful attempts to bring larger wafers to market, including Q-Cells over a decade ago, when they introduced a 200 x 200 mm cell. As a result, wafer sizes remained initially at 156 mm side length and then marginally increased to 156.75 mm for about a decade. However, several module products from various vendors are now available in the market. We observed the trend already in our last year's report on Advanced Module Technologies 2018, which featured four products in our modules listing with power ratings of 325 W and above. Two module series from LG were using 161.75 mm M4 wafers – one was its IBC module called NEON R that had a rated power of 365 W, the other its multi-busbars module NEON 2 with a rated power of 340 W. However, these produces are also based on high-efficiency cell technologies – IBC and passivated contacts. Then, JinkoSolar's Cheetah series using PERC cell technology reached 340 W using 158.75 mm wafers. Even more interesting was Canadian Solar's HiKu module, even though using rather low efficiency multicrystalline bulk material it was able to reach a 335 W power rating. Also in this case, the module design includes other advanced technologies such as multi busbar and half cells, but the key enabler for this module to reach such a high power was its larger wafer size of 166.75 mm, commonly referred to as M6. While in principle it is relatively easy for multicrystalline suppliers to move to larger wafers, as cutting them out of a square multicrystalline block is relatively simple, LONGi, the world's largest monocrystalline ingot/wafer producer, also introduced M6 size monocrystalline wafers. As a result, several companies have started adapting their modules to larger wafer sizes.
Competing with high-tech products
This is also reflected in this year's TaiyangNews Report on Advanced Module Technologies 2019. The lower benchmark set for this year's products power rating listing was at 340 W. Out of 25 module products from leading suppliers qualifying for this power class criterion, 16 models were built with wafers larger than the standard M2 format. This means, increasing the wafer size has enabled module makers with simple cell technology to compete with products based on various advanced cell and module technologies. For example, LONGi's Hi-MO4 series with 370 W rated power is at the same level as Solaria's Shingled and SunPower's "X" series and just one power class lower than REC's HJT module built with smart wire connection technology. PERC based Hi-MO4 is on top of the list if one does not look at very advanced cell and module technologies.
LONGi's Wahl provided more insight into the different wafer formats in his webinar presentation. Changing a 392 W module built with 72 M2-size cells to M4 (161.75 mm) wafers results in a 414.3 W power rating due to of 5.7% increase in surface. In case of M6 wafers, which are sawn from a larger 229 mm diameter ingot, the increase in surface area is 12.21% compared to M2. The power increase should be proportional, however, other improvements such as optimized busbars design resulted in an overall power increase of around 15% with Hi-MO4 and a rated power of 440 W. LONGi's Hi-MO4 series modules are based on this M6 wafer format married with half cell technology. The product range is offered in 60 and 72 cell configurations with power ratings ranging from 350 to 370 W and 420 to 445 W, respectively. According to Wahl, LONGi has started commercial production of Hi-MO4 modules in September 2019 and plans eventually to shift completely to M6 size. The modules are available in bifacial and monofacial variants, which brings the possibility to add a power gain of 8 to 15% when compared to the Hi-MO3 model. The increase in wafer size also enlarges the module size. Doing simple math, a 72-cell module grows roughly 60 mm in width and 120 mm in height compared to M2 wafer-based panels.
The bigger the size, the higher the power: Increasing the size of wafers has a direct impact on power output of the module – the difference in wafer area from M2 to M6 is about 12%. (source: LONGi)
Benefits of big
When it comes to the benefits of Hi-MO4, the rated power increase from 440 W compared to 390 W of the Hi-MO3 series results in savings on several levels in a solar system. According to Wahl, for a 2.75 MW power plant, the Hi-MO4 reduces the number of modules by 11.6%, decreases mounting costs by 6.1% and land use by 2.2%. There are also savings in BOS costs by 6.3% – and finally the change to larger wafers results in a LCOE reduction up to 2.9%, according ot LONGi. With regard to the system configuration, Wahl said that since the modules have the same Voc, no change is required for string length; however, caution needs to be taken that the inverter can handle the higher currents. Wahl finally emphasized that the Hi-MO4 series modules – by combining the benefits of the M6 wafer with mono PERC cell technology and bifacial and half cell technology – provides the lowest LCOE solution.
The story on the cell side
Moving up the value chain to the cell level, Vincent Lau, International Sales Director at Aiko Solar presented the Chinese cell maker's perspective on what it means to move to larger wafer formats. According to Lau, the largest wafers used – thus the largest cell size in commercial production – till 2018 was 156.75 mm, which increased from 125 mm in 2002. Then, as of 2018, his company started promoting cells with side lengths of 158.75 mm and 161.75 mm. From this quarter, the 'M6 era' has started at Aiko. However, Aiko believes that the march to even larger wafers is likely to continue in the future. Larger wafer sizes increase the cell power, which makes the products more competitive in the market. There are currently 6 different wafers sizes that are used in commercial cell production (see graph) and sizes would be dynamic in the coming two years.
Each time changing to a different wafer size requires tedious process of the optimizing the entire production lines accordingly. However, larger wafer not only results in higher power, they can be very advantageous with advanced interconnection techniques such as multi busbars. Lau gave an example – M2 size cells, when adapted for multi busbar modules, have an increased power rating of 5.42 W compared to 5.35 W with 5-busbar layout, a difference of 0.07 W. However, the same approach results in a power gain of 0.14 W on M6 size cells. Due to these undeniable advantages, Lau estimates that the market share of wafers larger than M2 from above 10% in 2019 will quickly increase to 60% in 2020 and 90% by 2021, which is much faster than most analysts anticipated. Aiko believes that M2 wafers will 'fade out in 1-2 quarters.'
When it comes to processing M6 wafers, Aiko Solar says its production lines are designed to handle such changes. According to our research, wafer formats up to M4 can be processed without any change; but M6 requires some modification in processing tools, if not complete changes, at least regarding handling tools. While that could be seen as a barrier for the move to larger wafers, this is not too high – the benefits of larger wafer based modules are simply too big.
The webinar recording and the presentation are available here.