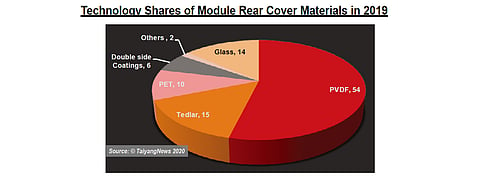
Today's backsheet are available in wide variety of composition and structures. When it comes to backsheet compositions, fluoropolymers rule the roost. Most leading Chinese module makers are using fluoropolymers and have been expanding continuously, all the while increasing their share in global module production. As a result, the prominence of fluoropolymers in the backsheet is also increasing. These backsheets are estimated to command close to 70% of the market share in 2019. In the fluoropolymer segment, there are two most popular constructions—one is a fluorine film on the air side attached to PET core and fluorine coating applied on the cell side, and the other with fluorine based coatings on both sides. However, specially made UV stable PET films based backsheets are also available. When it comes to fluorine films, there is technically a choice between PVDF and Tedlar, DuPont's proprietary PVF brand.
PVDF has the lion's share not only in the fluoropolymer group, but also across all varieties of backsheets. According to Jiajing Wei from the marketing department of leading PVDF supplier Fumotech, this variant of the fluoropolymer film, mostly serving as the outermost protective layer of the backsheet, was used in 70 GW worth of module production in 2019. The business was also good for Fumotech. "We shipped about 30 GW of PVDF last year, which is pretty much the same as in 2018," said Wei. With a production capacity of 50 GW, the company has a good 45% market share within the PVDF segment. ZTT is another important PVDF supplier with a capacity of 200 million m2, which is roughly 50 GW. However, the company itself consumes 50% of its production through its backsheet supply business. Since PVDF became such an important component of the backsheet, some backsheet suppliers are also producing PVDF in-house. Cybrid, the leading backsheet maker, operates a PVDF production facility of 20 GW capacity.
PVF or Tedlar is an equally popular fluorine based protective component. The product is exclusively supplied by DuPont – and two major PV producers—JinkoSolar and LONGi Solar—prefer Tedlar based backsheets in building their modules. Since these PV giants have been expanding considerably, the volume of Tedlar has also been increasing. While DuPont has declined to reveal its shipments data and market shares, our research indicates that Tedlar based backsheets were used in about 20 GW of modules.
PET is another important component of the backsheet. DTF, the proud inventor of polyester films back in the 1950's, naturally offers its solutions to PV backsheets based on PET. Like DuPont, DTF also supplies components of backsheet, but not the final product. However, the company played a major role in commercialization of fluorine-free backsheets in cooperation with Italy's Coveme, which developed all-PET backsheet. DTF offers its PET solutions to the PV industry under the brand name of Mylar, which has two product streams. The UVHPET range is specially designed for enhanced UV barrier and hydrolysis resistance properties to serve as outer layer of the backsheet, competing with Tedlar or PVDF. According to Davies, solar modules worth of 45 GW have been installed in the field using Mylar UVHPET, however, he would not disclose shipments volumes in last year. The company also supplies the Mylar core PET film, which according to DTF has been used since the birth of the solar industry and can complement any outer layers. According to our research, backsheets with a PET outer layer are used in 13 GW worth of solar modules.
For more details on the solar backsheet market, the leading players and its products, please download theTaiyangNews Market Survey On Backsheet and Encapsulation 2020, which can be downloaded for free here.
PVDF Rules Backsheet Market