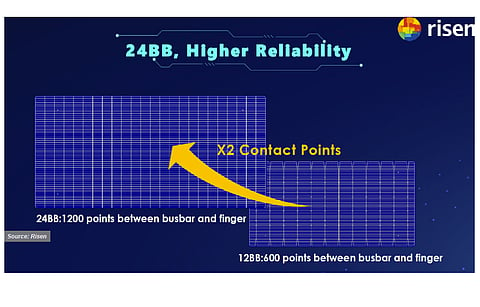
As for the changes required for HJT at the module level, it's more a matter of choice than compulsion. Taking interconnection as an example, HJT is not compatible with soldering in principle. However, most of the leading HJT makers are using optimized soldering, whereas low temperature supporting ECA based solutions are more popular outside China.
The main change required with soldering is a reduced temperature of less than 200 °C, and almost every stringing tool supplier offers low-temperature soldering support. Along with the temperature adjustment, the optimization of soldering material, the composition of the ribbon and the soldering method are just a few examples that require detailed readaptation to HJT, according to Risen. The company has spent a lot of time and effort on optimizing the HJT module making process. The 2 production equipment makers that offer ECA-based interconnection for HJT are Spain's Mondragon and Germany's teamtechnik. The details of ECA-based interconnection along with the optimization required for soldering have been discussed in previous reports and remain more or less the same (see A New ECA-Based Stringer for HJT from Teamtechnik).
The number of busbars topic discussed in the metallization section is implemented at the interconnection station. Risen tops the segment by being ready with a 24-busbar design. In addition to the savings on silver costs due to 'no busbars' and thin fingers, the design also brings a few other benefits. The more busbars, the shorter the distance between the contacts, thereby reducing the current density and power loss. It also increases the cell tolerance to microcracks and finger disruptions. The contact points between the busbar and finger increases by 2 times – 600 with 12-BB and 1,200 with 24-BB – which also increases module reliability, according to Risen's Yang. Huasun is already offering a 15-busbar based module and is evaluating options to increase the busbar count to 18 and beyond.
When it comes to module BOM, hydrophobic HJT requires an encapsulation solution that supports low moisture ingression rate; and equally important is the optimization of encapsulation material from a TCO compatibility standpoint. The polyolefin (POE) and coextruded structure of EVA-POE-EVA (EPE) offered by leading encapsulation material suppliers can meet these demands, especially in glass-glass modules, while a low-cost solution is still under evaluation for glass-backsheet configuration. EPE is currently the most widely used encapsulation solution for HJT.
Then, encapsulation material makers have developed a somewhat disruptive solution, specifically for HJT. To negate the absorption losses in amorphous silicon layers and TCO, especially the UV portion, Cybrid and Hangzhou First, in a coop effort, have developed a wavelength transfer film that converts the UV light into blue or red light. This approach has the potential to increase the module power by about 1.5%. While the technology can be adapted to any polymer base, since EPE is widely used, the solution is predominantly offered with EPE, but not limited to.
Within the backsheets segment, suppliers are increasingly bringing in high WVTR barrier products without using aluminum. While inserting a sheet of aluminum was a practice used to reach high barrier properties in the past, backsheet makers are now offering aluminum-free high barrier backsheets which can also be opted in transparent variants to be compatible with bifacial technology. Italy's Coveme, for example, launched one such product in mid-2022, while a few others are also offering similar polymer compositions. The encapsulation and backsheet solutions suitable for HJT are being discussed in detail in the latest TaiyangNews Market Survey on Backsheets and Encapsulation Materials 2022/23, which can be downloaded for free HERE.
For more details on HJT, download the TaiyangNews report on Heterojunction Solar Technology 2023 for free here.