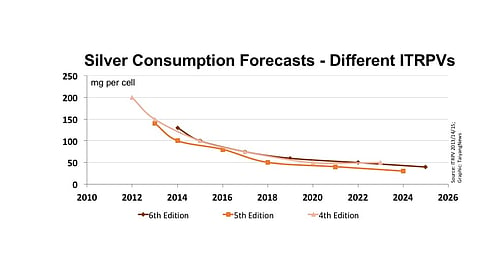
The assumptions for silver consumption in solar cell processing seems to has taken a "U" turn and back to a place it has been in earlier times. The International Technology Roadmap for Photovoltaics (ITRPV) has once again revised its estimation on usage of precious metal, the major constituent in most metallization pastes. This time the roadmap is more on the conservative side and the changed estimations are not just for the long term, but even for current consumption.
Silver is not only the major part in metallization, it also adds a lot to the bill of the cell part. After the wafer itself, the metallization pastes are the most expensive process consumables in cell processing, currently contributing about 10% of the non-silicon part of the cell's price. Thus reducing the silver load per solar cell is and has been one of the top priorities for the PV industry. Indeed, a tremendous effort from paste suppliers has resulted in remarkable reduction in the usage of paste – and thus silver.
Back to 2013 estimates for silver usage
The 6th edition of the ITRPV's roadmap, which was released in spring 2015 and updated in the summer, estimates that 100 mg (post firing) of silver is currently used per cell, while last year's edition was a bit aggressive with its estimate that 100 mg level had already been attained in 2014, which would be reduced gradually further in coming years. In fact, the 5th edition already considerably revised the 2013's projection for silver usage. The 4th edition's projection was actually considered and criticized for being too conservative for its estimation of 150 mg of silver usage per cell in 2013 and improvements to 100 mg in 2015, which apparently became the level indicated in the current version.
Like silver consumption, the drive to reduce contact finger width has taken a back seat. In addition, the 6th roadmap discusses the status and prospects of several other aspects of metallization, mainly under materials and process subsections of the document.
When looking beyond 2015, the roadmap indicates that from the current level of 100 mg of silver used per cell, consumption would go down close to 80 mg in the coming 2 years and 40 mg per cell within 10 years. However, the 2014 roadmap was expecting to attain the same level 4 years earlier, by 2021. The 5th release expected that by 2024 the silver usage would be as low as 30 mg, which is beyond scope of the current forecast. In fact, the 2013's projections are more inline to the 2015 edition. The 4th edition of the roadmap depicted the silver usage per cell would be 100 mg in 2015 and would fall to about 75 mg in 2017 and reach a saturation point of 50 mg in 2020.
Lead free very soon?
The 6th roadmap also made an interesting estimation regarding a component in cell contacts that hasn't received too much attention in the recent years – its heavy metal content. It is about making metallization pastes, especially the front contacting pastes, lead-free. Paste makers have been coming up with such formulations on and off, but the topic never caught fire – simply because performance was worse and regulations didn't force cell manufacturers to go that way. However, the 6th roadmap emphasizes that the lead-free front contacting pastes are expected to be "widely used in mass production beginning in 2017." ITRPV did not explain what´s the driver. In Europe, the guideline on the Restriction of Hazardous Substances Directive (RoHS), which enforces using heavy metal free materials, is likely to be revised in 2021 – and could then include solar cell contact pastes as well. But the European market is small, the solar market elsewhere. And as long as the efficiencies of lead-containing cell will be higher, the move to the green alternative rather seems like wishful thinking.
Role of copper unchanged
Like lead free pastes, the process to apply copper via plating has been known for several years, but the technology has never become part of mainstream manufacturing. ITRPV has not changed its stand on the role of copper in metallization. In line with the previous forecast, the 6th edition also anticipates that copper has no chances of entering into mass production before 2018, and would eventually win a market share of 30% by 2020. This delay is due to the lack of developments in plating technologies and continuous improvements for the screen printing process.
Finger-width reduction taking a slower pace
Indeed, screen printing has been evolving so strongly that it has become a synonym for the cell metallization process. The top topic in the screen printing arena is reducing the width of the applied fingers. According to the current roadmap, the development here is taking slower pace. With 50 to 60 mm finger widths already possible in production, below 30 mm level is expected to be attained in the next 10 years. The 5th edition's estimates are nearly the same: from the level of about 65 mm in 2014 the finger width was anticipated to reduce to 30 mm in 2021 and stay still from then on. Eliminating the busbars can accelerate the finger width reduction move, but implementation of this approach has more implications on the interconnection process of module making. By and large, the prospects of busbar less cells approach mainly depends on the developments in the interconnection process, where several interesting processes have been developed (see article on cell interconnection).
Double vs. dual printing
On the other hand, reducing the finger width would have a negative impact on line conductivity. But innovative printing concepts, such as double and dual printing, can compensate this shortfall. Double printing means that a print is added on a print, which requires a second printer and demands high alignment accuracy. The current roadmap foresees alignment accuracy of 10 mm (@ +/- 3 sigma) will be required from 2019 onwards, 3 years postponed from the timeline set in the previous version. There is also no update on the current status in the present document. If last year's value still holds good, the current printing technology can support alignment accuracy of 20 to 30 μm.
Double printing also requires a second printer, but the approach is less demanding for alignment accuracy, because, it actually decouples printing of fingers busbars. It also opens up the possibilities to use different pastes for fingers and busbars, such as less silver containing formulations for busbars. The dual printing also facilitates using stencils instead of mesh screens for application of fingers. Stencils can inherently facilitate transformation to thin fingers without loosing on performance. Last year's roadmap has also provided the share of these two techniques with respect to single printing, which is still the dominating technology. According to the 5th edition, in 2014, single printing had a lion's share of about 80%, while double printing and dual printing shared the remaining space, with the former having a slight upperhand. In 2018, dual printing was expected to succeed double printing with respective shares of 30 and 20 percent. Finally, in 2024, all three variants of screen printing were expected to share the printing space almost equally.
Stencil printing has bright chances
The 2015 roadmap, shifted its focus to the macro level – instead of concentrating on screen printing alone it provided an analysis on different metallization technologies. Screen printing is still enjoying a monopoly status, but would lose more than half of its share in 10 years. Every other technology is expected to gain from this fall. Stencil printing, though fundamentally the same as screen printing, has been assigned a special status: it is expected to enter mass production in 2017 – one year later than expected in the 5th edition – and get a meaningful share of 20% in 2025. Copper based metallization, which is expected to kick start in 2018 and grow to about 30% in 2020, is obviously also applicable to plating. However, as the technology share graph shows, the total plating share in 2022 is not even accounting for 20%. While this discrepancy indicates that there could be other methods apart from plating that utilize copper as the metallization media, ITRPV has not provided any indication about such a process. Within the plating segment, direct plating, which would take off in 2017, is expected to more than double its presence over the seed and plate approach in 2025.
Synchronizing throughput of front and backend
Since plating tools have not yet entered ITRPV´s radar, the tool level developments discussed in the present document are rather limited to screen printing – or to be precise, to the backend line, which includes printing, testing and sorting. Metallization lines with an hourly capacity of up to 3,200 wafers are available today, while front end lines have a throughput of 3,400 to 3,800 substates per hour. The current roadmap expects a synchronization in front and back lines will be achieved in 2025 capacity at 5,200 wafers per hour using well known batch and inline equipment setup, while 7,200 hourly throughput is assumed for cluster and inline configuration employing new automation concepts. The 2014 roadmap expected that this level would be reached 1 year earlier.
Not just the production capacity increment at the tool level, the overall developments in major areas of metallization are taking a slower pace – often they even seem to stagnate. The PV industry has apparently been focusing on optimizing the existing practices, rather than investing fresh capex in new production tools in the last years. This explanation holds good for the delays experienced by all new metallization technologies including the finger width reduction. Regarding silver consumption – what has been achieved in conjunction to the current silver price is already remarkable, any further effort may not be as rewarding as it was. Moreover, there is a lot of pressure and work on further increasing cell efficiency. The recent improvements have been mainly reached by better contact pastes, despite reduction of silver and thinner fingers. At some point things get more difficult. But would the silver prices shoot up again, the efforts to bring down the silver usage per cell would be probably intensified again, also to hold off copper plating – meaning the technology roadmap would again take a "U" turn, again on to the aggressive side of it.