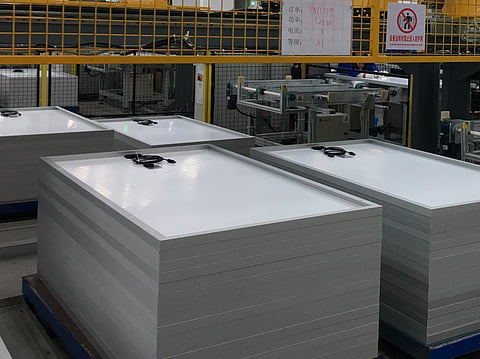
Backsheets are such an established component for solar modules that you would not think that a lot of changes happen from year to year. But this is solar – a hyper-dynamic industry sector that is under tremendous cost pressure, and so are the suppliers of backsheets who have to do both offer cheaper but still very reliable and long lasting products. At the same time, the global solar market is still in its rather early stages with huge growth potential, luring new players to enter as others fold from fierce competition.
We have several suppliers for the first time in the TaiyangNews Market Survey on Solar Backsheets my colleague Shravan Chunduri and I just published. And some them are also newcomers in producing backsheets. Dutch chemical company DSM had extended its solar business activities to the backsheet field early last year with the takeover of a Chinese producer, while Belgium-based materials company AGFA, primarily known for its photo film business, made its first appearance in the backsheet field at last year's SNEC and is now for the first included in our survey. Like DSM, which is the market leader in anti-reflection coatings for solar modules, AGFA also has some solar experience – it is a supplier of polyester, the core layer of almost any backsheet.
Newcomers in the backsheets field often come with new solutions. AGFA, for example, has introduced a non-fluoro PET backsheet product series, which, due to its mono-layer structure is not at risk of inner delamination and also comes with a very high reflectively. ZTT from China – though in the backsheets business for many years and offering mostly traditional 3-layer fluorine-based products with a PET core –, launched a new polyester / polyolefin (PET / PO) backsheet model in 2017.
However, completely fluorine-chemistry free backsheets only own a comparatively small share of the whole pie. Around 85% of the backsheets market was fluoro based in 2017. And this is no wonder – most of the solar market growth took place in China, which absorbed over 50% of global module demand. And Chinese solar developers and EPCs are true believers in fluoropolymer based backsheets. With China continuing to strongly dominate global demand this is unlikely to change.
The two global market leaders – like the years before, Cybrid and Jolywood from China – rely exclusively on fluoropolymer products (although Jolywood offers non-fluoropolymer products through its Italian subsidiary Filmcutter as well). Cybrid offers an interesting main product, where the inner layer facing the solar cell is a so-called fluorine skin, while a PVDF film is used for the outer side. The idea is to cut cost on using the more expensive fluoropolymer on one side of the product without compromising on UV protection.
The backsheet laminators in the fluoropolymer segment still mostly prefer one brand – Tedlar (PVF) from DuPont, which had a 25-30% share in 2017. But overall PVDF based products, which includes many low-price China products but also Arkema's well-known Kynar brand, have increased their share to around 50%.
These low-cost PVDF based backsheets are giving a tough time in particular to non-fluoro PET, which once were considered low cost solutions to the fluoro based products. An interesting segment to look at are coatings. When the coating quality is good, they can help to improve the cost structure for backsheet solutions both in the fluoro-containing and non-fluoropolymer variants as laminator companies try to cater to module manufacturers' different needs. Pure coating solutions certainly have one advantage – no interlayer delamination. Moreover, the technology has potential to reduce production costs compared to a 3-layer manufacturing method, but to play this card demand needs to increase significantly for coatings.
In any case, despite this huge cost pressure, one thing is key for backsheets – that is quality. As one of two outer layers of the solar module responsible for protecting the 'solar power generator' for around 3 decades, quality cannot be compromised on. Even more as the current partner in glass-backsheet module configurations is about to turn into a strong competitor.
With bifacial module technology anticipated to grow from nearly zero today tohuge quantities in the next few years, backsheet proponents need to work hard to avoid losing against sturdy glass. There are arguments for using backhsheets, such as keeping the module light or cost and others. But so far module manufacturers seem to prefer glass-glass designs for their first bifacial products although there are transparent backhsheet products available. DuPont is seeing the sign of times and is working on a new generation of transparent Tedlar film. However, it's way too early to predict what bifacial technology will mean for the backsheet business in the next 10 years.
The TaiyangNews Market Survey on Solar Backsheets 2018 is for download free of charge here.