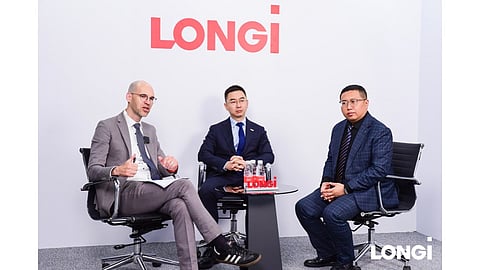
At SNEC 2025, leading global solar technology company LONGi signed a strategic cooperation agreement with TÜV Rheinland to drive quality and reliability in the rapidly growing solar PV sector. LONGi’s Vice President, Dennis She, and Chief Technical Expert for Solar Services at TÜV Rheinland, Dr. Gao Qi, sat down for an exclusive interview with TaiyangNews Managing Director Michael Schmela at SNEC 2025 to discuss the motivations behind the partnership amidst the evolving quality landscape of the PV industry.
They also talk about LONGi's back contact (BC) technology and how TÜV's rigorous testing is setting new standards for the future.
TaiyangNews: LONGi just signed a strategic cooperation agreement with TÜV Rheinland at the exhibition booth at SNEC 2025. As a leading PV company whose core philosophy centers on ‘Steadfast and Reliable’, what is the background and purpose of this collaboration between the 2 parties? How does LONGi view the current development of industry quality standards?
Dennis She: With advancements in solar technology and continuously decreasing costs, the global PV market has experienced rapid growth. According to forecasts by the China Photovoltaic Industry Association (CPIA), global new PV installations are projected to reach 531-583 GW in 2025, with China accounting for 215-255 GW of new installations. The global PV industry has now entered the ‘Terawatt Era’. However, amid this rapid industry expansion, the market has witnessed a significant number of safety incidents and disputes caused by product quality issues, resulting in losses for end customers. Against this backdrop, the establishment of robust quality standards for the PV industry has become increasingly urgent and important.
LONGi has always adhered to the core philosophy of ‘Steadfast and Reliable, Technology Leadership’. We firmly believe that product quality and reliability remain the ‘lifeline’ of the industry's development. LONGi's Back Contact (BC) technology, meticulously refined over 8 years, is now reshaping end-customer value with higher efficiency and enhanced full-lifecycle reliability. LONGi aims to lead and drive the upgrade of industry-wide quality standards through concrete actions.
Dr. Gao Qi: In the rapidly developing field of solar PV, TÜV Rheinland, centered on reliability, innovation, and sustainability, continuously assists the industry in breaking through technological bottlenecks, establishing high-quality industry standards, and driving the high-quality transformation of the global energy structure. TÜV Rheinland and LONGi have collaborated for many years. Their partnership is comprehensive and in-depth, and they share common goals and a shared mission within the PV sector. This strategic cooperation aims to further promote the upgrade of quality standards in the PV industry, reshape the industry's quality ‘cornerstone’, and support the efficient, healthy, and sustainable development of the end market.
TaiyangNews: LONGi's BC products have now entered the large-scale mass production stage. Across the entire value chain – from R&D and manufacturing to deployment and service – how does LONGi ensure the full-lifecycle reliability of its BC products?
Dennis She: In order to safeguard the interests of end customers, LONGi has created BC module products with more reliable value through a series of rigorous manufacturing processes that are higher than industry standards. These are:
LONGi's product life cycle standard: In terms of raw material control, LONGi's material introduction standard, incoming material inspection standard, and material performance monitoring plan are all industry benchmarks. In terms of process quality control, in LONGi's automated intelligent workshop, the 22 manufacturing processes can achieve 338 process controls and 153 quality inspections. In terms of finished product reliability monitoring, LONGi conducts reliability performance tests on a monthly, quarterly, and annual basis. The uninterrupted reliability performance tests will cover every product and every BOM set, fully ensuring the reliability of finished products.
Enhanced Reliability Testing: The Hi-MO 9 product has successfully passed the wind tunnel test with wind speeds as high as 64.4 m/s (equivalent to an 18-level super strong wind), setting a new industry record for wind tunnel testing. At the same time, the Hi-MO 9 also has a strong ability to withstand hail (with a hail ball mass as high as 43.9 g) and has successfully passed the 45 mm hail enhanced test conducted by the international authoritative organization TÜV Rheinland. The Hi-MO 9 has also successfully passed the fire test carried out by the National Inspection Group and has reached the highest Class A level. During the testing process, the modules did not show any self-ignition or detachment, demonstrating excellent reliability.
LONGi's ‘Lighthouse Factory’ Intelligent Manufacturing: As the first ‘Lighthouse Factory’ in the industry, LONGi Jiaxing Lighthouse Factory has taken the lead in the application of automation, Industrial Internet of Things (IIoT), digitalization, big data analytics, and 5G mobile communication technology, which means that LONGi has the highest level of intelligent manufacturing and digitalization in the global photovoltaic industry. The dual protection of the Lighthouse Factory and the ‘LONGi Product Life Cycle Standard’ fundamentally ensures the super high quality and extreme reliability of LONGi's BC products.
TaiyangNews: As an internationally authoritative third-party technical service organization, what is the quality status of the photovoltaic industry that TÜV Rheinland has observed? What issues are in urgent need of the entire industry's attention and need to be improved as soon as possible? How do LONGi's BC module products perform in real-world tests at the terminal?
Dr. Gao Qi: The quality issues in the photovoltaic industry are mainly focused on the following aspects:
Power rating exaggeration: The actual power of the modules is over-advertised or over-rated, with the nominal power being less than the actual power used.
Module quality issues: Such as micro-cracks in the cells affecting the power generation performance of the PV modules, and poor soldering of the electrical module, causing fires.
Counterfeit and substandard PV modules: Using brand names to sell low-grade modules and producing with inferior materials.
The LONGi BC product, Hi-MO 9 modules, underwent strict module sampling supervision under the evaluation criteria set by TÜV Rheinland and experienced a series of complex and rigorous professional comprehensive tests. They successfully won the AQM Award for both PV Module Energy Yield Simulation and PV Module Reliability. Meanwhile, the low-light performance of Hi-MO 9 has also been professionally certified by TÜV Rheinland: the spectral response rate of the HPBC 2.0 product is significantly better than that of the TOPCon product, with a leading ratio of up to 44% at the highest.
TaiyangNews: What value and expectations will the future cooperation between LONGi and TÜV Rheinland bring to the market in terms of product quality?
Dr. Gao Qi: This time, our further cooperation with LONGi will focus on the standard development of BC photovoltaic cells and modules, the reliability research of products, and the quality control in the mass production process of modules. We hope to set a new quality benchmark for the entire photovoltaic industry with high-quality BC products as the anchor point, and bring higher commercial value throughout the life cycle to the global market and customers.
TaiyangNews: Thank you.