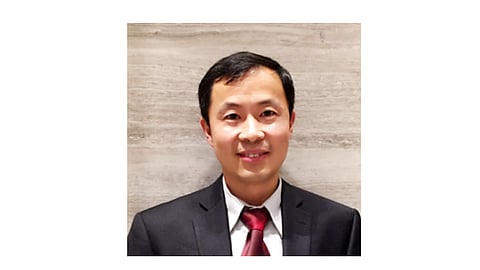
The LONGi Group has been the key driver in pushing the solar market to move towards mono PERC technology within few years. Now the Chinese vertically integrated ingot to module manufacturer addresses the next evolution stage – bifacial technology. TaiyangNews talked to Dr. Hongbin Fang, Director of Product Marketing at LONGi Solar, about recent solar market developments and why mono PERC bifacial is the next big thing in solar system technology.
TaiyangNews: You work at LONGI Solar, a leading integrated and globally active PV manufacturer. How do you see the solar market in general?
Hongbin Fang: The solar market is really expanding. Especially right now, in many places PV is going to become the cheapest energy source in the entire energy mix. With this, PV is going to be deployed more and more widely and increasingly in many areas. We are very optimistic that PV will become the lowest-cost energy source of the world – and everywhere.
TaiyangNews: With China having revised its solar subsidy scheme in early June, many think the world's largest market is done for the year. What's your opinion?
Hongbin Fang: We will see some pressure and some uncertainty in the Chinese solar market. This could indeed have some repercussions across the globe. But if you look at the cost of PV today, it already outcompetes other power generation sources in many places. This trend cannot be reversed. Sure, you always have some hiccups here and there, but on a global level PV will continue to expand in any case. The policy changes in China will be only a short- term setback. And once China has restructured its solar support program, which won't take long, it will come back even stronger. In the short term, with potentially lower component prices, it could accelerate PV adoption in other regions or markets
TaiyangNews: What is the key for solar producers to survive in this volatile market situation?
Hongbin Fang: It is mostly about cost and technology. Realising the lowest-cost technology is very important. A lot of effort has been made to cut the cost to the bare minimum. Going forward the most effective way to cut cost is to improve efficiency, which means increasing both module power rating and output. That will leverage extracting more energy from the same material. You need consistent investment in R&D to improve performance, drive productivity and improve cost.
TaiyangNews: Can you give us concrete examples?
Hongbin Fang: We see that the mono PERC family – including bifacial PERC – is the most viable way to realize lower LCOEs in the next few years. It is about the combination of energy yield, productivity and costs. The p-type mono PERC family has basically similar costs as multi technology, but it offers significantly higher yields. Moving to mono PERC is the right path to become a competitive PV company. And that's why more and more companies will finally implement it.
TaiyangNews: It's not that simple, right?
Hongbin Fang: To a certain extent it is. As efficiency improvement is the most effective way to lower PV cost, consistent investment in R&D to develop new technologies will definitely help companies to win in the end. LONGi is a good example for all this. We have been investing 5-7% of our revenue per year in R&D – that's a lot compared to most other companies. Indeed, we have been benefiting a lot from this consistent investments – our mono PERC cell efficiencies are among the highest in the world, we were breaking the PERC cell world record 3 times between Oct. 2017 and Feb. 2018. Investment in R&D will be rewarding. And companies doing that successfully – combined with a good expansion and marketing strategy will be able to thrive in the solar industry in the long run.
TaiyangNews: Any examples beyond cell and modules?
Hongbin Fang: Another good example is tracker mounting technology. A few years ago hardly anyone was using it after the short-lived boom of 2-axis trackers in Spain about a decade ago. But a few companies have improved the technology a lot, in terms of reliability and cost. Improving system yield significantly, today 1-axis trackers are being installed in most new utility-scale scale projects in sunny areas.
TaiyangNews: Coming back to modules, how important is bifacial technology for LONGi?
Hongbin Fang: Very important. And bifacial is not only important for LONGi, but for the entire industry. In fact, bifacial is a natural extension to PERC technology. Mono PERC is actually a bifacial solar cell. You need only a slight modification in original PERC cell processing and module processing to make it bifacial, which will bring you a roughly 8 to 15% higher energy yield depending on location. This is the additional energy generated just from the back side, which means a big step regarding efficiency improvement.
TaiyangNews: But what about cost?
Hongbin Fang: There is not really a difference. You only have to replace the aluminium back surface field with a grid. Indeed, you basically have similar production cost but will benefit from an up to 15% higher energy yield.
TaiyangNews: If bifacial is so lucrative, when will it really take off?
Hongbin Fang: Short term we need to establish some credit in the market, build a number of projects that generate electricity consistently for some time to validate the limited data we have so far. Let PV developers, owners, financial institutes be comfortable with the technology and its energy yield benefit. From there, the market will go bifacial in a very fast pace, much faster than most people think.
TaiyangNews: LONGi has been the key solar player responsible for the drive towards mono PERC. Do you also plan to do the same with PERC bifacial?
Hongbin Fang: Definitely yes. If you look at mono PERC versus multi, that's alone 10% higher in terms of power output. If you look at bifacial compared to mono PERC, this means roundabout another 10-15%. It is such a big improvement that everyone should take advantage of this in the end. We think bifacial will be the game changer in the next couple of years
TaiyangNews: What's your technology roadmap for bifacial technology?
Hongbin Fang: We will follow for bifacial solar the same route as we deployed for regular monofacial PERC. We have just announced our HiMO3 product. This is a half cut bifacial solar module that we've recently introduced at the SNEC 2018 trade show. We see this as the next step for the solar sector moving bifacial. This alone will bring us to module power ratings of 380 to 385 W for the 72- cell format and 315 to 320 W for a 60-cell panel. Then we will continue to increase cell efficiency to improve power output. On top, we are looking into using shingling, as well as other module power output improvement technology, which can be applied to bifacial as well as monofacial modules. We hope that these technologies will bring us to the next level, reaching the 400 W mark for commercial PERC modules in 2019/20.
TaiyangNews: The success of a technology will depend on investors financing such products. What about the bankability for bifacial technology?
Hongbin Fang: When it comes to bankability of bifacial technology, there are multiple approaches running in parallel. First, we are working with 3rd party test labs and research institutes. We are trying to study the sensitivity of backside gain versus different albedo, mounting height with trackers and fixed tilt. This is about system integration parameters. Some of our customers are also directly working with research and test institutes to collect the data themselves. This data will help to convince financial institutions about the backside gain of the bifacial modules. We are also cooperating with customers to set up test fields in specific project locations. This will build up customer confidence in the technology. Then we are also working with other stakeholders in the solar supply chain, such as tracker and inverter companies, to establish knowhow about the sensitivity of different installation setups. All this will help to optimize system components in order to pursue the optimal development for bifacial technology.
TaiyangNews: What is the reason for choosing PERC as the platform for bifacial technology? N-type cell architectures come with higher bifaciality, especially now that the price gap between n-type and p-type wafer is getting smaller.
Hongbin Fang: We think, right now p-PERC makes more sense and is also the most viable way to deploy bifacial and to deliver the best LCOE. Wafer cost difference between n-type and p-type is just one component, another major criterion is cell conversion costs, which is still higher for n-type than for p-type processes, such as PERC. Moving from PERC to bifacial is a natural progression. Today, PERC represents a huge installed base of 30 to 40 GW, which gives a good foundation to establish the infrastructure to do bifacial mono p-PERC. At the moment, from an economic standpoint, p-PERC bifacial makes most sense.
But even when looking into the near future, we see that p-PERC has very high development potential. Our record cell efficiency for a p-PERC cell has already reached 23.6%. I believe, it will take some more time for n-type.
TaiyangNews: The 23.6% level is indeed incredibly high for a PERC cell. But the floor talk is this is not a production feasible technology and based on some exotic advanced processing steps. Could you please explain how have you attained this efficiency? How far is this technology from entering the commercial production?
Hongbin Fang: We always keep production feasibility in mind. We are not developing something just to create another record. This high efficiency has been demonstrated on a R&D pilot line. It is part of a large number of a pilot production run to produce thousands of cells, with average efficiency about 23%. It may take some time, require extra process and material optimization and some additional hardware to implement in a production line, but this is definitely not a onetime record product just designed and made for demonstration. We are very optimistic that this cell design will be in production in 1-2 years.
TaiyangNews: What are the improvements you have in store for optimization of a PERC cell's rear side?
Hongbin Fang: On the rear side, we mostly look at passivation and doping, as well as metal contact optimization. In fact, this is something our development team has been working on constantly. On the other hand, we are not trying to improve bifaciality at the expense of sacrificing front side efficiency. We always feel that the front side efficiency is the most important parameter to be optimized and back side bifaciality will be improved on this base.
TaiyangNews: So what is the bifaciality you have attained for your p-PERC cell so far?
Hongbin Fang: At the module level we are at 75% right now. In the lab, we have already demonstrated more than 80%. We are looking to implement a bifaciality higher than 80% for the next generation bifacial p-PERC.
TaiyangNews: What's your focus on module level development regarding bifacial technology?
Hongbin Fang: Optimization work for both monofacial and bifacial is running in parallel. As I mentioned above, half cut cells which we have recently commercialized with our HiMO3 product is one important step forward. We are also looking at multi busbars and shingling. There are some other creative improvements we look at for the module envelope – both for glass and transparent backsheets. We keep an open mind and are evaluating many approaches to find the optimum for a low-cost high-quality module.
TaiyangNews: As for the rear cover, glass seems to be the preferred choice, at least when you look at the bifacial products that were displayed at the booths of most module producers during the recent SNEC 2018. What's your view on transparent backsheetss?
Hongbin Fang: Right now, transparent backsheet is not a mature product in the market. But we have been working closely with all backsheet companies to evaluate the latest developments. If we see a high quality product that is suitable and mature for production, we would adapt it.
TaiyangNews: When looking at the whole system, what improvement do you see here for bifacial technology?
Hongbin Fang: There are lot of things that need to be learned at the system level. Key is how to optimize system design to realize the full benefit of bifacial modules. When looking at ground optimization, it is about racking design, trackers and even regular fixed mounting systems. Then there is the inverter, which needs to be able to cope with the fluctuations from backside performance of the bifacial system. Adding DC optimizers could be another area people are looking into for bifacial modules applications. There are a lot of things that are going on right now. In the next 1 to 2 years, we will see many solar system experts experimenting with many different ideas to better understand the sensitivity of bifacial gain versus other parameters, and optimize hardware and software. We are working with the whole supply chain to optimize bifacial system technology.
TaiyangNews: We briefly touched trackers. What's your experience so far with combing trackers and bifacial modules?
Hongbin Fang: In our experience bifacial and trackers are a great combination. We see only upside if you combine bifacial modules with trackers. In fact, it has a synergy effect, something like 1+1 is more than 2. Right now, we are trying to acquire more data to better understand it how exactly it helps in improving energy yield. However, using trackers + bifacial is a two-step development for system technology. Trackers are one step, which enables you to improve energy yield by 10 to 15% depending on location; with bifacial technology you add another 10 to 15%. Combining Bifacial PERC modules with trackers will see 20-30% higher energy yield from PV projects and accelerate progress in lowering LCOE and reaching grid parity around the world.
TaiyangNews: Thank you for the interview.
The interview was originally published in the TaiyangNews Bifacial Solar Module Technology Report 2018, which was released at Intersolar Europe 2018 and can be downloaded for free here.