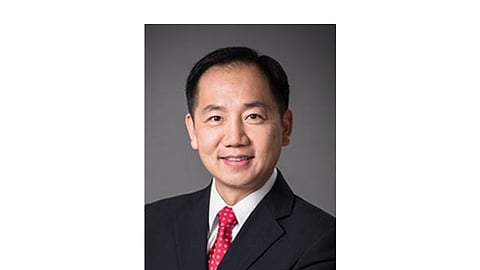
While the first bifacial solar module products displayed at trade shows use glass-glass structures, there are many reasons to stick to the well proven glass-backsheet design used for monofacial module products for decades. DuPont has introduced during the SNEC 2018 show in Shanghai a new transparent backsheet film for bifacial modules. TaiyangNews talked to Mark Ma, Global Marketing Manager at DuPont Photovoltaic Solutions, about the quality of solar modules, module testing and why Tedlar based transparent backsheets are also the optimal solution for bifacial modules.
TaiyangNews: How long do you think should be the lifetime of a solar module?
Mark Ma: If you ask me, modules should live more than 30 or 35 years; the longer the better. Because the longer a module lives, the lower will be the LCOE. If you look at a grid parity curve, there are two axes – one is module efficiency, the other is module lifetime. If you can increase both – improve efficiency and increase module lifetime – you reach grid parity faster.
Actually, we have already seen in the field that modules can last 30 or 35 years. While the efficiency of these old modules is obviously not so high, the quality of materials used for building those modules has been very high. However, to achieve very long-lasting modules, all module materials require high quality, not only very good backsheet material.
TaiyangNews: There are a lot of tests to check module quality. But basically, any of the many backsheet products on the market rather easily passes these tests. What's your view on current testing norms for module reliability, especially for backsheets?
Mark Ma: The fundamental issue with today's IEC or IEEE testing procedures is that they are single stress tests. They do not really simulate combined aging mechanism in the outdoor environment. For example, PET is similar to the material used in water bottles. If you put that plastic bottle inside a room, it will last for many years. But if you keep it outside, under sunshine, it will start yellowing, then cracks will appear, and finally it will be totally destroyed. So that's why we are saying if you are just testing damp heat and hydrolysis property of PET material, it comes out good. But if you are testing it exposed to UV, temperatures, moisture and thermal cycling together, then you can see if a material is suitable for long time durability. The current IEC test requires different solar module samples for UV, damp heat and thermal cycling to shorten testing time. That's a fundamental issue! Because it is simply not simulating the real aging mechanism of the material, which would require multiple aging stresses for the same module. So that's why we designed the so-called MAST test protocol, which stands for Module Accelerated Sequential Testing and relies on a module going through different types of aging mechanisms.
TaiyangNews: How does MAST work? And can you share any test results?
Mark Ma: Ideally you have one equipment that can simulate all these aging stresses working on a backsheet or module sample together. But that kind of equipment is extremely expensive. So it is not practical to be implemented in the industry. Thus, we've designed this sequential test. It can be easily applied with the current existing testing equipment. Though not perfect, it is much better for simulating the aging mechanism than today's common tests. DNV-GL recently adopted this testing protocol. They bought different modules from the market and tested both full size modules using Tedlar and PVDF based backsheets. Unlike Tedlar, all PVDF backsheets had cracks all along each busbar from the top to the end. This really tells how good a Tedlar based backsheet is.
TaiyangNews: Who is using MAST so far? And what's the next steps?
Mark Ma: Our MAST test has been widely adopted among tier 1 module makers. They are testing their materials with this testing protocol. Interestingly, after starting to use MAST testing they also started to use more Tedlar. JinkoSolar and LONGi have replicated these cracks with PVDF products in their own lab, thus they are now more convinced with Tedlar film.
Next to DNV-GL, other testing institutes are now adapting our MAST test. We are also working together with other testing institutes such as Fraunhofer and Sun Yat-sen university, which is the leading research institute in China for long term durability. We are also working with India's premier institute IIT Bombay on a field study. We've established a test lab together with HHSD (Huanghe Hydropower Development Company), the largest solar farm developer in China, which uses 100% TPT backsheets for their modules and adapted this testing protocol.
TaiyangNews: Due to China's announced 'restructuring' of its solar program, the market will not grow as fast as originally assumed this year. Due to these temporary overcapacities there will be huge price pressure. What are the consequences for the backsheet segment?
Mark Ma: This could cause some consolidation in the industry – not only in module making but also in the backsheet segment. It is actually good for the industry to become healthier in the long run. Companies with high quality products and strong financial balance sheets can survive this challenge and will become even stronger. Big players focus on long term sustainability of their business and tend to use more of our product. We have been in the PV industry for more than 30 years and have been through this several times. For DuPont, solar PV is one of our future business areas. We continue to focus on what we are doing and work with our partners who we believe will become future winners and pass difficult times together with them.
TaiyangNews: In comparison to 10 years ago, there are so many more different backsheet materials and products available now. As a leading backsheet component supplier, how do you see the developments in the different market segments in the backsheet field?
Mark Ma: The backsheet market is also consolidating in terms of backsheet type. At the very early stage, it was only TPT. Everybody was using TPT. Because we didn't have enough capacity to supply Tedlar film, people started to find other solutions. Now there are many different solutions available – PVDF films, coated backsheets, PET backsheets and polyamide backsheets. There was also fluoropolymer based backsheet from 3M and Honeywell. As your surveys on backsheets have shown over recent years, we are seeing fewer types of backsheets now – PVF, PVDF, and a little bit of PET, whereas the PET market is shrinking. The fluoropolymer film based backsheet segment is continuing to grow. However, within the fluoro segment, we see that more and more Chinese fluoro film suppliers are entering. That's how market dynamics are shifting.
TaiyangNews: What do all these products – also other fluoropolymers, such as low-cost PVDF – mean for DuPont's prime product Tedlar and how do you see the competition within the fluoropolymer segment?
Mark Ma: I think this is a healthy competition, which is also required for the growth of the industry. We don't think any of the fluoro film backsheet suppliers will occupy the entire market. However, now the product performance differences are becoming more clear. PVF Tedlar film has been proven for more than 30 years and is the golden standard for customers who really care about long term durability. The price of PVDF is very competitive. Customers, who are willing to take more risk, especially price conscious ones, choose PVDF or PET backsheets.
TaiyangNews: PVDF is becoming so price competitive that it is even giving tough competition to PET. Do you also see that?
Mark Ma: Yes. The price difference between PET and PVDF backsheet, especially products made with PVDF film from China, is quite low and very competitive. However, the consistency in quality is a question here. We've observed lower priced PVDF films from companies that are new to the market with little experience and whose manufacturing process, batch to batch quality consistency and even their formulation still have some issues in aging tests.
TaiyangNews: In the early days, DuPont was strictly controlling the end product associated with Tedlar, which was mainly TPT, then TPE. But now there are some companies, like Jolywood, that are offering TPC products. How come?
Mark Ma: We are actually open to different materials being used for the inner layer. DuPont is doing a lot of aging tests, which are much more stringent than the industry standard. So whatever the inner layer used by our laminator or backsheet supplier, we just want to make sure that those backsheets can pass our stringent MAST tests. That being said, the key attribute of the coated structure is really the thickness of the coating layer. We have seen that there is a large variety of thicknesses in the market. The thinnest is only 1.5 to 2 μm. We are not comfortable with such thin coatings. Because we believe that in order to block 99% of UV you have to have a thickness of about 10 μm. That's why we encourage our laminators to make inner layer coatings with more than 10 μm thickness.
TaiyangNews: How do you see the potential of bifacial technology? And what does that mean for you as a backsheet component supplier?
Mark Ma: We believe that bifacial technology has a promising future. It brings the ability to generate power from the backside and maximize total power output of the module. We believe that in the long run, bifacial technology will continue to gain shares in the market. That's why
we are actively working with our laminators to develop a transparent backsheet. We believe this is the better solution for the bifacial module than the current glass-glass structure.
TaiyangNews: Although the share of glass-glass modules is small, most module companies first think about glass-glass modules when going bifacial – at least that's what they exhibit at trade shows. Why is that when taking into consideration that basically all modules are glass-backsheet modules today?
Mark Ma: Indeed, most of the bifacial module makers are using a glass-glass structure. That's simply because they really don't have a better alternative solution. Conceptually, glass-glass is a good structure, but practically there are many difficulties or bottlenecks. After we've introduced our new transparent backsheet at the SNEC 2018 show, we saw a lot of enthusiasm and interests from module makers. They want to test our transparent backsheet.
TaiyangNews: What are the advantages of transparent backsheets over glass?
Mark Ma: Before going into this I would like to emphasize that a traditional encapsulation system consisting of glass – EVA – backsheet structure, has been working very well over the past 30 to 40 years. It's been proven. By replacing the backsheet with glass, you are changing the dynamic of the encapsulation system of the module. One thing also needs to be taken into consideration that when you want to change the backside, you have to change other things, because it is one holistic system.
For transparent backsheet, there are at least four big advantages. The first is what we call "breathable." EVA degrades over time and releases acetic acid. The moisture will also gradually come into the module from the edge and from the junction box holes. The moisture and acetic are used to be released or pushed out through the backsheet when the module starts to work in daytime as temperature starts to increase. With a glass-glass structure you will seal everything inside the module and it cannot be released. The key issue we noticed in field tests with glass-glass modules is the delamination of the glass from the backside of the EVA.
Intuitively, you would think glass-glass is a very durable structure, but the issue I explained above is one drawback. Another big problem is PID. Bifacial modules with glass
– EVA – glass structure have more severe PID issues as the sodium ion from backside glass could migrate to the backside of the cells. That's why a lot of bifacial modules are made using POE instead of EVA, which is a big increment on cost as POE costs a least double or more than EVA.
The second big benefit for backsheet modules is their lightweight. One person can carry a regular glass- backsheet module, but for glass-glass you need 2 persons to carry it and mount it on the racking system. Moreover, it is much more difficult to transport a heavy glass-glass module. Bifacial modules are often installed with a tracking system, for which weight is a very important factor. For 72 cell glass-glass modules you require a more powerful tracking system if you want to have it run smoothly in the long run, which will increase the BOS cost. The issue is similar for rooftop systems: glass-glass modules are too heavy to be used for such applications.
The third benefit is the frame, which is very important for a solar module. I have seen a lot of glass-glass modules without frame, which will save a module maker quite some of its production cost. But being frameless comes with issues, as installation of such modules is tricky. If you install it properly, the racking and mounting cost of frameless modules is higher. If you install it incorrectly, it will lead to failure in the field. After 1 or 2 years, the module will be bending because of this gravity. It also takes much longer to install frameless modules, resulting in higher labor cost. On the contrary, the benefit of a frame is that both static and dynamic mechanical loading are much stronger. Let me refer again to the test protocol, because every module can pass the dynamic loading test as the frequency of the dynamic loading is so slow, that it is not simulating the real environment. In our MAST test we immediately see the difference with some delamination taking place after the dynamic loading test.
The fourth advantage is from the module maker's perspective. When using a transparent backsheet they can keep using the traditional module manufacturing process. This is a big benefit as the yield rate for glass-glass is lower than for traditional modules with backsheet structure. Moreover, for glass-glass you need to drill holes in the glass, which has potential to generate cracks in long term.
TaiyangNews: But the USP for glass-glass modules is longer warranty times today. At least module makers do offer now 30-year performance warranties for glass-glass products. Can backsheets match that?
Mark Ma: We have proven that modules with backsheet can last more than 30 years in the field. We have been promoting to the industry that extending life time is more effective in lowering LCOE than decreasing module price.
We have done some calculation showing that if you extend the life time of a module from 25 to 30 years, in order to achieve the same LCOE reduction you have to lower your module price by 16 US cents per watt. That's big money to lose, but it is easy to achieve if you use a little bit better material in the module. This is the message we are spreading in the solar industry: Modules with backsheet are field proven, which is the best test. If you use our Tedlar backsheet, it is easy to achieve more than 30 years life time.
TaiyangNews: So do you believe these 30 year lifetime warranted for glass-glass modules?
Mark Ma: In my opinion, this is more marketing than based on solid data support. Glass-glass module suppliers have launched this new product and need to promote it. Longer warranty is one of their marketing tools. When talking to module makers they told me that they have done more stringent damp heat tests and a glass-glass module is performing better. As I mentioned earlier, that's due to the testing protocol, which is just based on one test result. I have not seen any solid data to support this claim.
TaiyangNews: Some say a backsheet at the end is just 'plastic' and will tend to lose transparency. What's your response to that?
Mark Ma: As for transparency, high quality backsheets stay at the same level as in the beginning – around 90%, which is similar to backside glass. That's because backside glass does not have an ARC coating, so the transmission rate is not as high as that of the front cover glass.
However, there is a perception that the transparent backsheet is not durable as much as glass; that's also because of the same experience from your day to day life. The example of the water bottle again fits here. Backsheet, at least the Tedlar backsheet, is an engineered polymer system where we have got great length to ensure that the material will be durable throughout the entire life of the module. Some backsheets have indeed less UV protection. They could turn yellow and suffer from transmission decay. So it is very important to choose the right material, because materials matter. Our backsheets go though the most vigorous testing in the industry to make sure that our materials will stand up to the elements they see outdoors.
TaiyangNews: DuPont has been having a transparent backsheet in its portfolio for years. What's your experience in the market with that product?
Mark Ma: In fact, we have transparent backsheets for 20 years. It has been used in some niche markets for special applications. With our previous generation film, we are able to have a TPT structure. However, the previous generation film was still very expensive. For the new generation, we've improved performance and we've lowered cost. We also have to work together with laminators to develop a transparent backsheet structure using our Tedlar film.
TaiyangNews: What's different with the new product?
Mark Ma: We worked with our backsheet partners and launched both TPX and TPT structure transparent backsheets with new clear Tedlar film. In addition to clear Tedlar film on the airside, the durability of the inner layer is also very important for transparent backsheets. If you think about how a module is exposed, the light comes from the front side, through the glass, through the EVA and when it goes between the silicon cells, it can hit the inner layers. One of the main things we have been doing is trying to figure out exactly what the inner layer has to do so that we can ensure that there are no failures due to the inner layers as well as the Tedlar side of the backsheet.
TaiyangNews: And what about the price performance ratio of your product?
Mark Ma: It is similar to other solutions. We definitely want to make this transparent backsheet very attractive. As we know that price is a key purchasing factor, our pricing on transparent backsheet will be very competitive compared to a glass solution.
TaiyangNews: When will your new transparent product be available commercially and who will offer it?
Mark Ma: Jolywood is the first one. They already have the TUV certification. Other laminators have also made samples of transparent backsheets. We are still testing them. It will be coming to the market in the next couple of months.
TaiyangNews: What are your expectations for the new transparent product and transparent backsheets in the long run when bifacial really takes off?
Mark Ma: Different customers will have different preferences and it is always good to have a healthy competition. For bifacial module makers it is convenient to be able to opt between glass-glass and transparent backsheets. Depending on different applications, both will coexist. It is hard to say which one will be bigger; I think both will have a significant share in the market.
TaiyangNews: Thank you for the interview.
The interview was originally published in the TaiyangNews Bifacial Solar Technology Report 2018, which can be downloaded for free here.