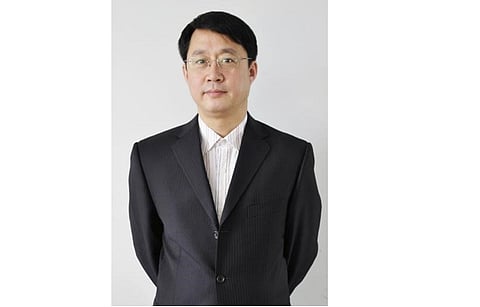
TaiyangNews: What was it that attracted Huasun to HJT?
Wenjing Wang: The first driver is our technical background; both our operation and R&D teams have a solid background in HJT. On the finance side, the capital market in China is encouraging for new and next-generation technologies and HJT fits into these requirements. A similar trend can also be seen in Europe where most of the companies focused on bringing manufacturing to Europe are involved with HJT in one way or the other.
TaiyangNews: Could you please brief us on your current production capacity and your future plans with HJT?
Wenjing Wang: We want to establish ourselves as a leading supplier of HJT in China as well as worldwide. In the first phase, we have a 500 MW cell and module line, which is already up and running at full capacity for some time now. Now, the second phase of the capacity expansion is in progress and close to completion, totaling 2 GW in capacity. We also have plans for a third phase, the discussions for which have already begun. Our ultimate plan is to reach 10 GW in the next 5 years.
TaiyangNews: For the first phase, it is clear that you have both the cell and module. This integrated cell-module approach, is it going to be a common feature in your next expansions?
Wenjing Wang: We're going to do both — cells and modules — at least in the beginning. However, as we strengthen our roots as a key HJT supplier, we will put more emphasis on cells over modules. To be specific, until we reach a 5 GW capacity, we're going to keep the cell and module capacity closely matched. At that time, with the insights we've gained into the market, we would act as the situation demands.
TaiyangNews: Is our information correct that Huasun is also selling cells?
Wenjing Wang: Yes, but only to limited partners with no conflicting interests and complementing roadmap. For example, if a company has the ability to make good modules without cells, we are very interested in working with such companies. In this way, we can help more module makers start HJT module making, creating a large HJT production base. Making HJT cells is more complex and requires deep know-how, which we have and we can make best use of.
TaiyangNews: Coming to the first item of cell processing, what is your current mainstream wafer size? And what is your roadmap for moving to larger wafers?
Wenjing Wang: Currently, we are using M6, and we will go for G12 with the next 2 GW line.
TaiyangNews: Does it actually make sense to use larger wafers for HJT as the production equipment, especially the heart of the line, which is PECVD, is based on an inline batch setup that cannot benefit from a throughput advantage?
Wenjing Wang: There are definite advantages of moving to larger wafers, but the benefits are not the same as with PERC. For example, the surface area utilization of the wafer is higher with larger wafers compared to the smaller ones. The ratio of dead zone – which does not receive any deposition – to the active area is smaller with larger wafers compared to smaller wafer formats.
And one more important point to note here is edge losses. With the larger wafers, when processed into the complete cells and then sliced, the edge losses are higher with HJT when compared to PERC. However, instead of processing a full cell, we can process half wafers; meaning the wafer is sliced into half before cell processing, which only makes sense with larger wafer formats like G12. Such an approach also takes care of equipment utilization, as a half of G12 is similar to M6 in size. The difference now lies in shape; M6 is now changed to a form with a rectangle-like structure, which just requires carrier adaptation, and there are no more edge losses.
TaiyangNews: What is your take on wafer thickness?
Wenjing Wang: Our current production using M6 is typically processing 150 μm. Our new fab that would process half cells of G12 would initially also start with 150 μm and from then on, we will eventually reduce the wafer thickness.
TaiyangNews: We hear all the time that HJT can support thinner wafers, so what's stopping the to move to thinner wafers, say 120 μm?
Wenjing Wang: There is a drop in efficiency with thinner wafers. If you would like to have high efficiency on a thinner wafer, the passivation on both sides should be of very high quality. That is also one of the reasons why PERC or TOPCon cannot be made on very thin wafers, both of which are specific to superior passivation on the rear side, but the passivation isn't so high in quality on the front. The current amorphous or, the next step, microcrystalline silicon based HJT can both allow thinner wafers, probably not 120 μm directly, but 130 μm without any efficiency loss.
TaiyangNews: In terms of wafer supply, heterojunction requires the n-type. How is the situation with its supply and what is the price difference to p-type?
Wenjing Wang: Right now, we need high lifetime n-type wafers for HJT. We need lifetimes of more than 1,000 μs, and 3,000 μs is our preference. We also like to have high uniformity in wafer resistivity. However, wafer makers are not able to supply such narrow distribution of wafer resistivity.
TaiyangNews: In wet-chemistry, what cleaning process are you employing?
Wenjing Wang: The main choices here are RCA and ozone based, and we have opted for ozone-based cleaning.
TaiyangNews: Who are the equipment vendors you are cooperating with for PECVD?
Wenjing Wang: For the first phase, we have contracted Maxwell and Ideal Sunflower as our PECVD partners. Both companies are part of the second phase of our expansion as well, but their shares are not necessarily the same; Maxwell represents a larger portion of our supply for the second phase.
TaiyangNews: Are there any interesting developments taking place in the area of PECVD?
Wenjing Wang: Oh yes. We are, in fact the entire industry is, working on microcrystalline silicon to replace amorphous silicon. This is only referring to doped layers as the i-layer on both sides is still amorphous. The main benefit of microcrystalline is higher conductivity, which is about 4 to 5 times order of magnitude. Here you don't have to depend solely on ITO for lateral conductivity. Using a microcrystalline doped layer on both sides also leads to high field effect passivation. The microcrystalline Si or SiOx on the front side of n-type can induce more sunlight into the solar cell, which can lead to increasing efficiency.
TaiyangNews: Who are your TCO deposition tool vendors?
Wenjing Wang: For the existing facility, we are using tools from Maxwell and VON ARDENNE. For our 2 GW new line, Maxwell is our only tool supplier and we are happy with them. And PVD is not a very critical process in a way; the performance difference has negligible effect on final efficiency, if any.
TaiyangNews: Any interesting developments in the TCO deposition segment you can share with us?
Wenjing Wang: PVD is also about the costs. Target utilization and replacement of indium are a few topics that are attracting attention. We have been working on alternatives such as AZO, but the process is in the R&D phase and some way away from mass production. That is all the details I can provide you at this time.
TaiyangNews: What is your opinion about RPD?
Wenjing Wang: RPD is a very interesting technology, but it is missing the implementation in the mass production. So far, we have not seen any of the recent companies opt for the technology for mass production. I suppose there are still some issues to be solved before the technology becomes suitable for mass production.
TaiyangNews: Moving on to the next step, metallization, are you doing anything special?
Wenjing Wang: Dual printing is what we are doing. The paste quality is good enough with dual printing and double printing is not necessary. And of course, you can reduce the paste consumption with dual printing, which is very much required for HJT.
TaiyangNews: What is the typical paste consumption and what is the finger thickness you are operating at?
Wenjing Wang: It's about 180 mg for M6 and bifacial, 28 μm opening, and finger width is 35 μm.
TaiyangNews: Since the reduction in silver consumption is key for HJT, what is your strategy there?
Wenjing Wang: What we are using is 9-BB, but if we can use 12-BB, then the paste usage can be reduced further. Another possible improvement can come from paste makers by increasing the paste conductivity. However, a somewhat interesting subject in metallization, especially related to reducing silver usage, is to use a paste containing silver coated copper particles.
TaiyangNews: Have you worked with the silver coated copper particle paste? And what is your impression about the whole approach?
Wenjing Wang: To answer your first question, yes, we have already tested the silver-copper paste. Its conductivity and peel strength are quite similar to silver. The efficiency difference is 0.1% absolute to none, meaning it is not significant. However, the jury is still out for reliability. The reliability test results are not yet available.
TaiyangNews: How is the overall development related to HJT in module production?
Wenjing Wang: As for HJT, the technology development at the cell level is going on at a high pace, but rather very slow at the module level. The know-how is not widespread. So we had to learn it the hard way, experimenting and finding solutions on our own. Some of the early problems were low CTM ratios, especially when you cut the cell into pieces, and also degradations such as LID and LeTID. Thanks to our R&D team, we found solutions to all these issues. For example, we found methods to reduce the dark degradation when the solar cells are treated with light and heat, and how performance loss from the dark degradation and other degradations can be recovered. This is also the reason why we have planned to produce the cells and modules. It is always nice that these two stations work in cooperation. In fact, some degradations can be avoided by optimizing the cell processing. This must continue till all the processes at both cell and module levels are standardized.
TaiyangNews: For interconnection in module making, soldering is the method most employed in China with approaches such as ECA-based in use; what do you think is the better way for soldering?
Wenjing Wang: I have to admit that we have not tried ECA. We think standard soldering is still a cheaper solution. It has been optimized a lot. For M6 and 9-BB, soldering is already good enough. Soldering also works fine for M6 and 12-BB. The CTM losses are quite close to PERC. But beyond this, it is not clear. When we have 25% efficiency cell based on microcrystalline, then perhaps it requires a redesign of the electrode pattern. On the other hand, ECA has also got some issues. It is made of organic material, so the UV and other reliability aspects of the ECA have to be evaluated carefully. ECA is also expensive. In my opinion, ECA will start looking attractive if the cell technology can get rid of the busbars altogether.
TaiyangNews: What is your best efficiency?
Wenjing Wang: The certified best efficiency is 25.26%. In production, the best and average efficiencies are at 25.1% and 24.3%.
TaiyangNews: Finally, if you could comment on the costs of HJT in comparison to PERC?
Wenjing Wang: The price of an HJT module is about 0.2 RMB higher than PERC. It is like 10% higher, however, in certain cases LCOE is comparable to that of PERC at this price level already. But you cannot really compare PERC and HJT today. PERC has a very strong production base of above 300 GW and a well-established supply chain. When HJT is mainstream and market research firms also list the price of HJT along with PERC, that is when the two become comparable.
TaiyangNews: Thank you for the interview.
The interview is an excerpt of TaiyangNews' Heterojunction Solar Technology 2022, which is available for free download here