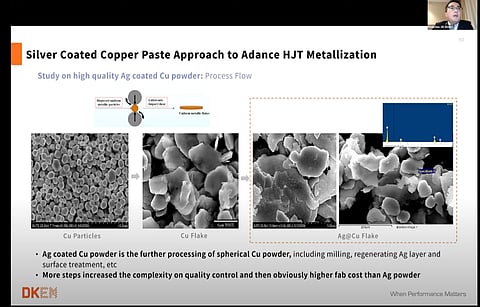
Metallization is a key step in solar cell processing and is quite unique in HJT cell processing. After the recent article on HJT metallization discussed the status quo of HJT metallization including the fundamentals, approaches and key tools supplier, here we summarize the main technology developments within the HJT metallization segment (see Looking Into HJT Metallization).
DKEM's Vice President Of Technology and Marketing Kevin Nan presented a comprehensive review on this subject in his presentation Recent Progress on Industry-Ready and Low Cost Metallization Solutions for HJT Cells at TaiyangNews Conference on High Efficiency Cell Technologies (see the video recording HERE).
The 5 major challenges for HJT, according to Nan, are:
Nan also discussed the methods to address these issues. The company has developed a paste called DK16A that featured the said improvements. Silver powder selection and fine tuning the curing behavior of the organic system can improve the volume resistivity greatly. Featuring these improvements, the DK16A finger paste has low volume resistivity and provides better finger morphology, thus serving as a foundation for reducing silver consumption. "We demonstrated about 0.2% efficiency gain in small testing," said Nan. The properties of silver flakes and, again, the selection of organic curing system influence the printing speed. The DK61A finger paste works well at higher printing speeds of up to 350 mm/s. DKEM has also studied the influence of the printing speed on performance by testing the paste at different speeds. The company took line resistance as the metric for this evaluation and tested the print quality at two different print speeds – 250 and 350 mm/sec. In both cases, the DK16 showed lower line resistance, which was also confirmed at a customer's site. The organic curing system has also led to a considerable reduction in the curing times to about 10 minutes.
As with PERC, fineline printing is the key to improve the aspect ratio and also paste consumption. Lowering the volume resistivity, discussed above, is again the key here. Putting low volume resistivity together with other optimizations, DKEM was able to print through a 22 μm finger opening to realize a finger height of 25 μm and 29 μm width for the solid part, while the complete finger spread was still less than 50 μm. DKEM has also tested its paste with stencil printing, enabling it to reach a total finger width of less than 50 μm. Solderability is what comes next, and that brings the busbar design into the equation. The silver paste used for HJT busbars has a typical silver loading of above 90%, which is 85% in the case of PERC. DKEM's Nan calls for a "reasonable adhesion evaluation method" that would enable the paste vendors to develop low silver content busbar paste for HJT. MMBB is also a ready and robust busbar layout, while SMBB – nothing but increasing the wires to beyond 9 to 12 and more – is the way to go, which also necessitates a modified busbar paste system, according to Nan.
While DKEM is just an example, most leading paste suppliers such as Fusion, Heraeus and Kyoto Electricals are working on these lines and offering their latest paste systems suitable for HJT.
Silver coated copper
In parallel, these companies are working on silver coated copper particles based paste system for HJT, another matter of interest in the segment. The logic is simple: instead of using pure silver suspension, the copper particles are coated with silver. The approach straight away reduces the silver consumption.
With respect to efficiency, it depends on what percentage of silver is preplaced with copper, according to Risen's Yang. "We found that at 60% silver, there is almost no performance loss," said Yang. However, decreasing silver from that point on reduces the electrical attributes proportionately. Even at this 40% silver reduction level, the savings are directly reflected in metallization costs. The performance parity is also acknowledged by Huasun's Wang. Without going into the formulation details such as copper vs. silver loading, Wang said that conductivity and peel strength of the copper coated silver paste is much similar to that of a typical silver paste. "The efficiency is similar or lower by just 0.1% absolute," said Wang. Risen even found that the paste closely resembles its silver counterpart in terms of printing attributes such as screen opening, finger width and aspect ratio.
As mentioned above, every leading paste supplier is working on this approach and at different stages. DKEM has also presented results of its preliminary study on the silver coated copper paste at TaiyangNews High Efficiency Cell Conference. The process in simple terms is as follows: copper particles make up the starting material, converted into flakes, and then coated with silver using a chemical process. The crucial part of the formulation is the quality of silver coated copper powder, meaning coating the copper particles completely, that will impact the reliability of the complete cells and modules., according to DKEM. The company has also introduced a post-coating surface treatment to mitigate the risk of oxidation and silver migration, which adversely affect the performance of such a paste. TOYO is one of the early adopters of the silver coated copper paste solution. The company shared details of its solution at TaiyangNews' session at CSPV China conference in 2021. TOYO is employing plating. "We can coat anything with anything," said Marwan Dhamrin. The company can coat silver, copper, nickel or tin over copper, aluminum or silica. TOYO employs plating for coating, and the specialty of its method is that plating is done while the particles are dispersed to avoid agglomeration. In this way, the core particles are plated individually and covered completely to achieve best results. TOYO found a slight relative efficiency drop of 0.32% when using the silver coated copper paste on the rear side. Several companies are evaluating different configurations and compositions of the silver coated copper. The first results are encouraging, at least on performance.
The next major aspect is reliability. Here as well, a few companies have found encouraging initial results. Risen found no additional power loss after extended IEC tests with copper. TOYO has also conducted TC200 and TC400 tests on minimodules built with cells using silver coated copper paste on the rear side. It also found that the power degradation is not too different from the reference.
Cost reduction is the main goal in any cell processing without reducing the performance. TaiyangNews focus on industrial practices and processes that work on reducing the cost of final product. In case of HJT metallization segment using of silver coated copper and adopting to SMBB are a few approaches that are intensively evaluated.
DKEM will present about Reducing metallization paste usage as key factor to reduce manufacturing costs for HJT cells in the upcoming TaiyangNews Virtual Conference on High Efficiency Solar Technologies from November 23-25, 2022. For Free Registration, Click here.
The text is an excerpt from 3rd edition of TaiyangNews' Heterojunction Technology 2022 report, which provides an overview on the most recent HJT developments as the technology is entering the GW scale production level and can be accessed free of charge here.