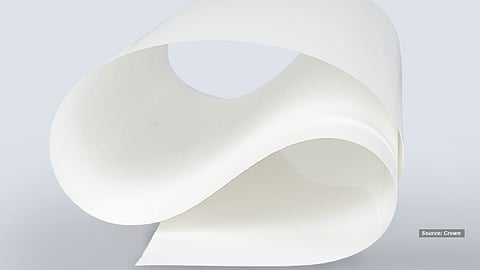
Early PV module backsheets, such as TPT, incorporated polyvinyl fluoride (PVF) layers, with Tedlar from DuPont being widely used
To reduce costs, manufacturers replaced inner fluoropolymer layers with polyethylene (E-layer), leading to the development of TPE and KPE structures
Fluorine-free backsheets like PPE were introduced as an alternative, using UV-stable PET to maintain durability while lowering material expenses
Coating-based backsheets, including CPC and KPC, became widely adopted, while new designs such as all-PP structures from Endurans and Borealis applied coextrusion methods instead of traditional lamination
The story of backsheet structures and their polymer chemistries is quite diverse. These compositions and structures have evolved over time to meet the changing requirements of module manufacturers. The backsheet has 2 key roles – protection from the environment and electrical insulation to provide long-term durability. Polyester (PET) alone can fulfill both, and that too very cost-effectively. However, PET’s UV stability is rather poor, limiting it from becoming a self-sufficient backsheet material. Thus, this core layer of the backsheet is sandwiched between 2 UV-resistant films, leading to the typical 3-layer construction of a backsheet, and UV protection is where fluoropolymers come in.
For some historical context, early PV modules used backsheets based on an FPF structure, with the core PET layer sandwiched between 2 fluoropolymer layers. The fluoropolymer here is nothing but the proprietary polyvinyl fluoride (PVF), commercially known as Tedlar, popularized by DuPont, the well-known US-based chemical giant. Such a backsheet structure was often referred to as TPT, which was also the first backsheet composition used for PV module applications. TPT dominated the backsheet market for many years. PVDF, also from the fluoropolymer stream and used in other outdoor UV-proof applications, has found a footing in the backsheet segment as well. France-based chemical company Arkema developed a special 3-layer PVDF film under its Kynar brand. The backsheets based on Kynar also follow a similar structure as TPT, abbreviated as KPK, which is also a registered trademark of the company (see Transition Of Encapsulation Materials & Structures From EVA To Alternative Technologies).
As module prices declined, backsheet manufacturers faced cost pressures. They realized that using fluoropolymers on both sides of a symmetrical backsheet was a bit of overengineering since the inner film experiences only about 1/10th of the UV exposure compared to the outer layer. During this time, backsheet manufacturers replaced the rather expensive fluoropolymer films with a more economical polyethylene, which is usually referred to as ‘E’ or the ‘Primer’ layer. This initiated the first configuration change in backsheets. All fluoropolymer backsheets then shifted to a polyethylene-based inner layer, leading to new backsheet abbreviations such as TPE and KPE. All suppliers involved in the manufacture of fluoropolymer film-based backsheets then started offering symmetrical variants as well as products with an inner ‘E’ layer.
What also led to this shift to the ‘E’ layer was the fact that Tedlar was in short supply during that period, pointing research in the direction of fluorine-free backsheets. Benefiting from the successful implementation of the polyethylene inner layer and the PET core – both of which are fluorine-free anyway – the only effort needed here was to develop a fluorine-free outer layer. Coveme, the development leader in this field then, as it still is, introduced a UV-stable PET in close cooperation with DTF, which provided the base material. This backsheet configuration is denoted as PPE, which is still Coveme’s main product. The fluorine-free aspect of these backsheets has not only been used to market this product as ‘environmentally friendly,’ but it has also made them less expensive than their fluoropolymer-based counterparts.
Some companies followed this template to redefine the backsheet structure by replacing the films with coatings. Such backsheets are commonly abbreviated as CPC, where ‘C’ stands for coatings of both types – with and without fluorine. Both HANGZHOU FIRST and Jolywood offer fluorine-containing coatings, while Germany-based Aluminium Féron supplies backsheets coated with non-fluoropolymers, and CPC has now become the mainstream and the leading backsheet structure. The TaiyangNews Solar Technology Conference India 2025, on April 10-11, will feature a Day 2 session on "Advancing Solar Module Performance and Reliability Through the Right Bill of Materials." InYoung Suh, Director of Business Development, Hangzhou First and Dr. Khushbu Patel, AGM, Business Development ALISHAN GREEN ENERGY, will discuss innovations in encapsulants and back sheets. Check for more conference details here.
While the inner layer of the backsheet is not exposed to UV as much as the outer layer, the radiation cannot be neglected altogether. Cybrid worked on this idea and developed a so-called fluorine skin, which is essentially a fluorine coating denoted as KPf, which can be regarded as KPC. Cybrid’s inner coating solution fully addresses the UV protection concerns on the cell side. At the same time, it is far less expensive than a fluorine film. The idea sold so well that the then-young Chinese company soon grew to become the segment leader (see Advanced Solar Technologies Drive Changes In Module Materials).
Cybrid’s success with this approach was enough to lure other companies to inner coatings. This move was actually very easy for companies that had already been working on coating-based solutions, such as HANGZHOU FIRST, to use their expertise for cell-side coatings. Eventually, several companies followed suit.
Jolywood, another coating expert and an important laminator for Tedlar-based products, introduced yet another structure called TPC, adapting Cybrid’s template into its proprietary coating technology. For module manufacturers that do not prefer inner coatings, backsheet suppliers such as ZTT and Lucky Film were among the first companies to start offering backsheets with polyolefin as the inner layer, denoted as KPO. Lucky Film started offering a Tedlar variant of this, characterized as TPO. A few companies have developed dual-layer structures with either polyolefin (PO) or polyurethane (PU) attached to PET, called PPO and PPU, respectively (see Solar Encapsulation & Backsheets Adapting To A Shifting Market).
What’s common about all the backsheet structures mentioned above is that they are all based on PET as the core layer, and lamination is the process used to stack different layers. Endurans, taking a different route, developed backsheets that use polyolefins as the core layer – coextruded instead of the typically followed lamination method. While the company employed a polyamide top layer, with a polyolefin inner layer and core with slightly modified chemistries between them, it has now shifted to an all-PP structure, a structure Borealis has also developed.
To summarize, the major backsheet configurations in today’s market are TPT, TPE, TPC, TPO, KPK, KPE, KPf, KPO, PPE, CPC, all-PP, PPO, and PPU.
As India aims to strengthen its solar PV manufacturing industry, TaiyangNews Solar Technology Conference India 2025 will provide a platform for experts to discuss cutting-edge advancements. Taking place on April 10-11, 2025, in New Delhi, the event will feature technologists, scientists, and engineers driving innovation in the sector. Early-bird registrations are on here.
The text is an excerpt from the latest TaiyangNews Market Survey on Backsheets & Encapsulation Materials 2024/25, which can be downloaded for free here.