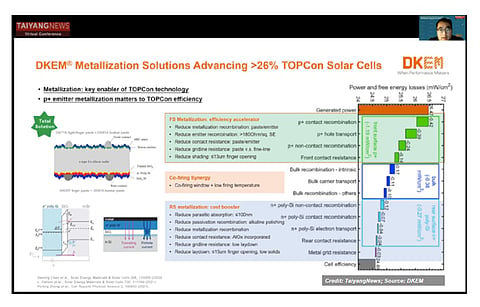
During TaiyangNews Cell Production Equipment Conference, DKEM's Nan presented the key developments in metallization paste solutions for TOPCon (see recording here). He underscored that metallization innovation is a key enabler for the industrialization of TOPCon technology. To be specific, while the metallization on emitter is the efficiency accelerator, the rear is the cost controller.
DKEM uses p+ SE Emitter as a front side metallization that helps achieve lower contact resistance with a >0.3% efficiency gain combined with metallization paste modifications. The metallization of TOPCon's rear is complex, as the rear surface engineering varies significantly with choice of the deposition methods used for forming the tunnelling oxide and poly as well as for the front side passivation. Nevertheless, the latest DK96T silver paste from DKEM with its wide process window supports all types of rear surfaces. He further emphasized that with the integrated metallization solutions, the company is confident to lead the TOPCon efficiency progress to 26% by of this year, or early next year. TaiyangNews has also talked to Weili Shi, the chairman and CEO of DKEM On Key Developments In Metallization Solutions For TOPCon Solar Cells.
Keeping the fundamentals the same, the industry has developed a few advanced screen-printing technologies to help overcome some of its inherent bottlenecks. The standard process has been that all the busbars and fingers on the front side are applied at once. Then came fine-line printing, which is all about reducing finger thickness. The benefits of fine-line printing are twofold – reducing shading and paste consumption – which deliver both on performance and costs.
The side-effect of finger disruptions followed on the heels of fine-line printing. To counter this, double printing was introduced, in which a print-on-print is applied. This not only neutralizes peaks, valleys and interruptions, if any, it also helps build the finger height, thereby safeguarding the performance even when using thinner fingers. In parallel, dual printing (different from double printing) was also implemented, which decouples the printing of busbars and the fingers. It allows for the use of separate pastes for fingers and busbars, which have different functionalities altogether. In either approach, the printing line requires 4 printers per line and a cell maker can easily switch between these printing methods without much effort.
This 4-printer configuration has been the state of the art for a couple of years now. Over 90% of the lines shipped since 2020 have been equipped with a fourth printer to facilitate either of these approaches. As to the preference among the duo, a rule of thumb is that while double printing slightly favors efficiency, it is low costs with dual printing through reduced paste consumption (up to 10%).
Interestingly, the adaptability of these 2 approaches changes according to the market. Double printing was in vogue at the time of publishing our TaiyangNews Market Survey on Screen Printers in 2018, with favorable silver prices and an industry focus on better performance. It is no wonder that dual printing has dominated in subsequent years; with high prices for silver and other materials, saving every possible penny is what matters for cell manufacturers. Dual printing is still the state of the art metallization for TOPCon as well.
Not just pastes, the industry is also working on alternative metallization approaches such as dispensing and rotary printing, which are very close to screen printing, and there is also plating. While we have provided a summary of these approaches in our previous survey, we have not received any updates to report in this survey.
AMAT's Tempo Presto LW production platform – maintaining a best-in-class alignment accuracy of +/- 8 μm and in a dual lane configuration – reaches a high throughput that varies according to wafer size (8,000 wafers per hour for M6, 7,400 for M10, and 7,000 for G12). The tool platform supports even higher throughputs, the only limiting factor being the maximum printing speed supported by the paste. The company is also promoting a lab variant of the printer with nearly the same specifications but in a single-lane configuration. As part of the complete backend line configuration, AMAT has a long list of components such as loaders/unloaders, buffers, flipover, AOI, microcrack inspection systems, paste dispensing, automatic scale, cell lifters, dryers, curing furnaces, inline optical/electrical test, sorter, automatic screen cleaning, screen breakage detection, data management system, and 3D profilometer.
ASYS from Germany has provided data for its printing platform called AIRON. The line with less than 1s cycle time supports 12.5 μm @ 6σ alignment repeatability and that for all relevant wafer formats. It also uses a new concept of moving the wafers on pedals, while still sticking to the stationary print nest philosophy. As a result, the machines are faster, supporting a cycle time of 1 second per wafer. At the same time, enough care is taken so that the wafers are not subjected to additional stress. The dual-lane configuration reaches 7,200 wafers per hour for sizes up to M10, while the throughput drops to 6,000 with G12 wafers.
Maxwell, in addition to the previously listed MX XDLZ, has also provided data for MX-XDL. Both the models use the rotary table design and come with an option of single or dual lane. The main differentiator between these tools is wafer size. The MX-XDL can handle wafers from 158 to 220 mm and 140 μm; however, the printer is optimized to work with 100 μm wafers in case of HJT. The MX-XDL is designed to handle wafer sizes from 166 to 230 mm. The number of printers in the line also differs – 5 and 4, respectively. Throughput is the next major difference. The MX-XDL has a throughput of 8,000 wafers per hour with M10 and 7,200 with the G12 size and above, while MX-XDLZ is rated at 7,200 and 6,900 wafers per hour, following the same order. S.C New Energy has provided data for its printing line solution for the first time. The company's solution, called SCPT6800D, is based on the rotary table platform and mainly designed to handle wafers from 180 to 230 mm. The line platform allows both single and dual lane processing. At a throughput of 8,000 M10 or 7,200 G12 wafers per hour, the printing line supports a production capacity of 500 MW.
The article is an excerpt from the TaiyangNews Market Survey on Solar Cell Production Equipment 2023, which also includes detailed product specs and can be downloaded for free here.