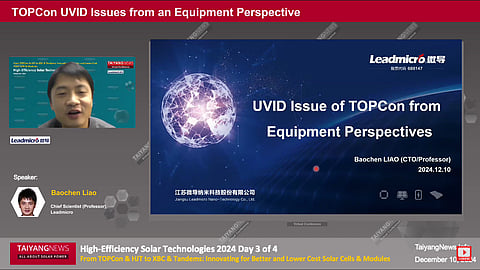
According to Leadmicro, the ALD Al2O3 layer does not cause UVID but rather helps mitigate its impact
Its PECVD ToxPoly (ZR5000X2) tool can deliver throughput of up to 6,800 wafers per hour of 182 mm and up to 5,400 wafers per hour of 210 mm size
Leadmicro's latest PECVD tool significantly reduces maintenance time, capacity loss, and manpower time
A TOPCon module’s susceptibility to ultraviolet-induced degradation (UVID) stems from the weakness of the cell’s front-side passivation under prolonged UV exposure. Understanding this potential failure mechanism under UV exposure requires comprehensive lab-scale investigations at the TOPCon cell level, as well as establishing relationships between different fabrication methods, particularly for front-side ARC and Al2O3 film deposition.
Following a comprehensive presentation by Cybrid Technologies on addressing UVID with an innovative encapsulant in TOPCon modules at the TaiyangNews Annual Flagship Event 2024, Baochen Liao, Chief Scientist of Leadmicro, provided a brief overview of TOPCon’s UVID challenges from an equipment maker’s perspective (see Leadmicro presentation here). The Chinese tool maker also discussed the latest technological progress in TOPCon and its new offerings. Headquartered in Wuxi City, China, Jiangsu Leadmicro Nano-Technology Co. Ltd. is a global equipment manufacturer specializing in the development, design, manufacturing, and service of advanced thin film deposition. The company has developed core competencies in Atomic Layer Deposition (ALD) technologies.
Liao opened his presentation by discussing phenomena observed in the scientific literature regarding the effects of UV at both the cell and module levels. Referring to Paper 1 titled, “The effect of light soaking on crystalline silicon surface passivation by atomic layer deposited Al2O3”, NUS, 2013, the effect of prolonged light soaking and subsequent dark treatment on single layer Al2O3 thin film layer was investigated. Irrespective of the n-type or p-type FZ-Si surface, enhanced passivation after light soaking was observed. However, this passivation was not stable under UV light exposure which reduced the passivation level to its initial level, noted Liao.
The paper titled, “Effect of UV illumination on the passivation quality of AlOx/c-Si Interface”, ISFH, 2016, investigated the effect of UV illumination on single-layer silicon nitride (SiNy) as well as on AlOx/SiNy stacks. Following a firing step, the AlOx layer showed an improvement in surface recombination velocities (SRV) during the UV illuminations due to the increased negative fix charge. However, AlOx/SiNy stacks showed very stable performance, no matter whether on a p-type surface or with the glass or EVA to simulate at the module level. On the contrary, SiNy film experienced degradation after UV illumination, says Liao.
Furthermore, in paper 3, the effect of UV illumination was experimented on front-side emitters with AlOx/p+ type Si as well as on the rear-side SiNy/n+ type Si interfaces which showed stable performance. However, the cell structure, featuring front-side SiNy/n+ type Si interfaces, exhibited performance degradation.
Liao further emphasized that the 2022 SLAC NAL paper, Comparison of UV-Induced Degradation of High-Efficiency Silicon PV Modules with Different Cell Architectures, revealed that the n-PERT cell structure – equivalent to TOPCon's front-side architecture – exhibited varying degradation levels across 4 different module samples under prolonged UV illumination. The higher degradation levels observed in samples C and D, compared to the stable performance of samples E and F, suggest that solutions to mitigate UV degradation exist even at the device level. This result concludes that the degradation differences might be due to variations in the passivation layer deposition steps or the doped profile of the front emitter, explained Liao.
In contrast, a subsequent scientific paper showed that the thickness of remote plasma-enhanced chemical vapor deposited (PECVD) SiNx films, used for passivating the p-type crystalline silicon interface, also plays a critical role. The increase in thickness from 20 nm to 140 nm reduced the UV degradation significantly.
Liao presented a comparison table of photon energy (or optical bandgap energy, in eV) for UV illumination and various passivation materials, including Si-H bonds, AlOx, Si-rich SiNx, and N-rich SiNx. Compared to the UV illumination bandgap energy range of 3.1 eV to 4.428 eV, AlOx has a bandgap between 6 eV and 8.8 eV, while the other materials' bandgap energies overlap with the UV illumination range. These results explain why AlOx reacts minimally to UV radiation compared to the other interfaces with the materials mentioned above.
Leadmicro summarized its conclusions, based on inferences from the referenced papers, as follows: changes in the composition, density, and thickness of the ARC significantly affect the UV dose at the Si interface. Improving AlOx density helps address the UVID issue, and, contrary to expectations, ALD Al2O3 does not cause UVID. In fact, ALD Al2O3 can help reduce the impact of UVID.
Aligning with InfoLink Consulting's February 2024 cell technology report, which predicts that TOPCon cells will account for more than 70% of the market share by the end of 2024, several technological improvements have been made to both the front-side and rear-side of these cells. On the front side, the industry is transitioning from a homogeneous boron-doped emitter to a boron-doped selective emitter. This change is driven by laser-assisted firing technology and laser selective emitter (SE) techniques, which enable higher front-side sheet resistance. Meanwhile, on the rear side, the latest trend in TOPCon technology focuses on polysilicon thinning. Leadmicro notes that this results in a lower laser-assisted firing temperature.
According to InfoLink's August 2024 data, regarding different thin-film deposition routes for tunnel oxide and poly-Si layer deposition, the PECVD route has achieved a market share of 55%. In comparison, the LPCVD and PVD routes hold 41% and 4% market shares, respectively.
Leadmicro also provided a brief overview of its latest offerings, including the 5th generation PECVD ToxPoly (ZR5000X2), the 8th generation KF20000S series ALD system, and the XH10000 series diffusion system. In addition, Leadmicro promoted its newest half-cell series thermal and deposition tools, such as the ALD KF20000S/D-H, PECVD ZR5000-H, and Diffusion XH10000B-H series. The PECVD ToxPoly (ZR5000X2) tool features patented integrated technology, including in-situ tunnel oxide, in-situ poly-Si doping, in-situ mask, and tunable doping levels. It boasts impressive throughput capabilities of up to 6,800 wafers per hour for the 182 mm size and up to 5,400 wafers per hour for the 210 mm size. Furthermore, this tool's innovative non-cooling tube or electrode maintenance solution significantly reduces maintenance time, lowers capacity loss, and dramatically cuts manpower time compared to the earlier version.