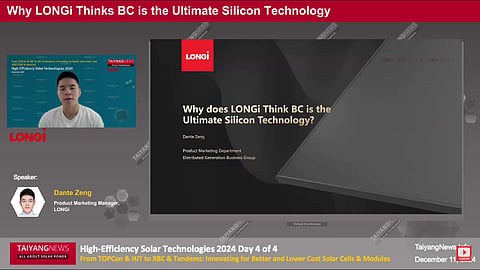
LONGi, poised to fully shift to BC platform-based domestic cell production, has achieved up to 26.6% mass-scale efficiency for HPBC 2.0 cell
The HPBC 2.0 cell design reduces module overheating due to localized shading by bypassing blocked current at the individual cell level
The HPBC 2.0 cell's front-side passivation film, with up to 2% uniformity, exhibits effective resilience against UVID compared to TOPCon cells
Back contact (BC) cell technology, which moves both the front and rear metal contacts to the back of the cell structure, is the latest trend in the industry. With unique features like a shadow-free front surface and superior aesthetics, BC cell-based modules are becoming increasingly desirable for various application scenarios, particularly in distributed generation (DG). Recent technological advancements, such as improvements in bifaciality – a major limitation of BC technology – are making BC modules suitable for utility applications as well.
Dante Zeng, Product Marketing Manager of LONGi, provided an overview of the company’s HPBC cell technology at the TaiyangNews Conference, High-Efficiency Solar Technologies 2024 (see LONGi presentation here). LONGi, a vertically integrated Chinese PV manufacturer, began researching BC technology in 2017, recognizing its potential. After successfully completing R&D and product prototype verification, the company launched its HPBC 1.0 (Hybrid Passivated Back Contact) cell, achieving a mass-scale efficiency of up to 25.5% by 2022. In 2024, it introduced the next-generation HPBC 2.0, featuring advanced wafer and passivation technology, boasting a mass-scale efficiency of 26.6%. According to Zeng, LONGi’s full domestic cell capacity will be migrated to the BC platform.
The HPBC cell structure combines BC and hybrid passivation technology, utilizing wafers textured at the sub-micron level to enhance short-circuit current by absorbing more sunlight, according to Zeng. It also features full-field rear-side hybrid passivation and front-side multi-layer passivation. Additionally, the front and rear surface hydrogen passivation of this cell increases open-circuit voltage (Voc), thanks to an improved charge carrier lifetime. However, the next generation HPBC 2.0 version, featuring the latest n-type TaiRay wafer, bipolar hybrid passivation, and 0BB metallization, boasts a mass-scale efficiency of up to 26.6%, noted Zeng. This upgraded BC cell-based product can be characterized based on 3 key metrics – generation performance, reliability, and aesthetics.
The enhanced power generation of the HPBC 2.0 cell stems from advancements in key areas, including optical and electrical properties. According to Zeng, the absence of any front busbar and finger coupled with multi-layer anti-reflection film maximizes light absorption and increases the short-circuit current (Isc) of the cell. In addition, the absence of shadow generally created by the front side ribbon shielding of multi-angle incidence sunlight improves light absorption by about 2.27% compared to standard non-BC cells. In reality, the daily movement of the Sun from east to west, during both morning and afternoon, over the TOPCon product – featuring gridlines – would create more than 2.27% shading compared to the HPBC product, explained Zeng.
Additionally, the fully high-doped bipolar passivation on the rear side enhances Voc and fill factor (FF), while also enabling passivated contacts with lower contact resistance, ultimately leading to increased cell efficiency.
To mitigate potential power losses from localized shading on the module, LONGi has developed an innovative soft breakdown design for the HPBC 2.0 cell structure, leveraging the BC cell’s low breakdown voltage characteristic. This innovative feature, similar to the built-in bypass diode for each cell, prevents localized heating by bypassing individual cells with high partial resistance from the connected sub-string. According to Zeng, the soft breakdown feature can prevent up to 70% of potential power losses due to partial shading on the HPBC module, compared to the standard TOPCon counterpart. The Hi-MO X10 module, featuring HPBC 2.0 cells with a power temperature coefficient of -0.26%/°C, delivers up to 2.18% higher power generation per-watt at an 85°C operating temperature compared to its TOPCon counterpart, which has a -0.30%/°C temperature coefficient.
LONGi's module, equipped with HPBC cell technology, demonstrated high resilience against extreme environmental stressors such as dust accumulation, heat and humidity, freezing conditions, and strong UV exposure. Zeng explained a few of the major reliability features of its HPBC modules.
The Hi-MO X10 module, equipped with HPBC 2.0 cells and a soft breakdown design, prevents localized overheating caused by shading by allowing blocked current to bypass, ultimately mitigating the risk of hotspots. Zeng adds that this feature can reduce localized overheating in the HPBC cell-based module by more than 28% compared to the standard TOPCon cell-based module, while also mitigating the potential fire hazards of rooftop installations.
Additionally, the HPBC module’s lower hotspot temperature – below 100°C – compared to the standard TOPCon module’s 170°C, ensures long-term durability. Regarding the UVID in HPBC 2.0 cells, the front-side passivation film, with up to 2% uniformity, exhibits effective resilience compared to the uneven front-side passivation layers of TOPCon cells caused by high-temperature boron diffusion. Corrosion of the module's metal contacts in hot and humid environments is primarily caused by a chemical reaction between acetic acid generated by the encapsulant and the lead (Pb) content in the metal electrode's alloy coating, as well as the aluminum content in the metallization paste, explained Zeng. However, the HPBC X10 module’s metal electrode, composed of 1/6th lead content compared to the TOPCon metallization ribbon, showed lower degradation under DH environments.
LONGi's latest TaiRay wafer, featuring up to 16% higher maximum rupture strength and a thickness increase of up to 10 µm compared to mainstream wafers, demonstrates enhanced mechanical strength and reliability. Additionally, the full-back contact one-line welding process reduces cell edge stress to 26 MPa, compared to the higher edge stress of up to 50 MPa in TOPCon cells due to the Z-shaped metal contact soldering process. This ultimately improves the HPBC 2.0 module’s resistance to cell cracking.
Starting mass-scale production of HPBC 2.0 cells in Q4 2024, the company is poised to expand up to 10 GW by the end of next year. Furthermore, the HBC cell structure, BC cell based on HJT cell architecture, has achieved more than 27.3% lab-scale efficiency. This HBC cell, projected to come into mass production by Q1 2026, has the potential to reach 27%+ mass-scale efficiency in the future, says Zeng.