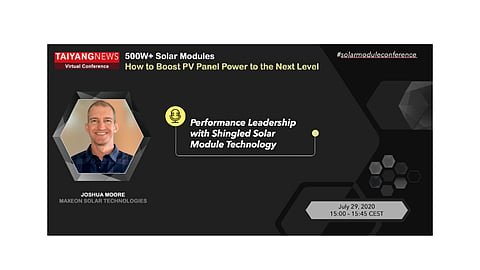
Over the past few months, leading module makers have been in a race to bring higher power modules to the market, raising the bar for utility-scale panel power to 500 W and more. Acknowledging the trend, TaiyangNews organized a virtual conference on the topic: 500W+ Solar Modules - How to Boost PV Panel Power to the Next Level (see TaiyangNews Virtual Conference on 500W+ Solar Modules). All leading module producers that had announced 500W+ modules in H1/2020 took part in the event and presented details of their technologies. We are summarizing the company presentations at the event and also include the Q&A parts—here, for Maxeon Solar Technologies.
Among the pioneering module suppliers announcing 500 W+ modules, Maxeon Solar Technologies is somewhat exceptional. It is the only non-pure Chinese company and the only one that is using advanced shingling technology to reach module powers beyond 500 W as of now. Introducing its Performance series P5 product, shingled modules with up to 545 W output at TaiyangNews 500W+ Solar Modules Conference, Joshua Moore, Director of Product Management at Maxeon, presented the power, performance and reliability aspects of the new modules.
Maxeon structure
As Maxeon Solar is a relatively new entity, Moore introduced some background on the company structure. SunPower, the leading back contacts solar technology manufacturer, announced in Nov. 2019 to spin-off most of its manufacturing businesses into a separate company, Maxeon Solar, a JV with Tianjin Zhonghuan Semiconductor (TZS) (see SunPower To Bifurcate into 2 Public Companies). During its Capital Markets Day in mid-July, SunPower provided details about the Maxeon business strategy and during its Q2 results it specified that the spin-off date will be Aug. 26 (see SunPower Exceed Q2/2020 Revenue Guidance). Maxeon will be managing R&D, manufacturing, and the global sales and marketing portion of SunPower. The soon to be spun-off company is already scaling up its capacity of 2.75 GW. Maxeon will be marketing the products under the SunPower brand outside of the US and Canada, meaning the product names and the brand are going to remain the same. The company has three strategic partners—Total, SunPower and TZS. Being a long-time investor in SunPower, Total brings downstream experience into the venture. TZS, a world leading wafer manufacturers from China and the only supplier of 210 mm wafers, contributes its operational expertise on the manufacturing side besides putting in capital to scale up SunPower's technology. SunPower has been a long-time associate of TZS, in a joint venture under the name of HSPV (now 20% owned by Maxeon), which has been making P-Series shingled modules since 2018 and announced in Feb. 2020 to increase capacity to 8 GW with the goal to become a Top 3 module supplier.
Making shingles reliable
Originally designed by Cogenera, a US technology company acquired by SunPower in 2015, the P-Series is based on shingling technology. It involves cutting the cell into six pieces, and the latest P-Series uses cells with 210 mm side length. These cells are connected like roof shingles with aerospace-grade conductive adhesive. According to Moore, the connection points are stronger than the normal soldering-based interconnection and provide a high degree of resistance to thermal cycling. Moore also showed the results on thermal cycling tests; the P-Series modules registered nearly no power loss even after 800 temperature cycles, while the conventional modules typically lose 5 to 10% power under such test conditions. This is enabled by the flexibility and durability of the cell string formed by connecting small cell strips with conductive adhesive, which Maxeon calls hypercell. Another example of reliability under stress is the 4-point bend test with about 400 N. The EL images of the P-Series showed no power loss, while the conventional panel shows several cracks and dark spots resulting in power loss. Maxeon uses a proprietary encapsulation material that minimizes degradation from moisture ingress.
Less prone to hotspot
The parallel circuitry design of the module makes it less susceptible to shading and hotspot development. "We design the modules to be cooler and safer," said Moore referring to hotspots. The connection circuit design allows the current to flow around the shaded area, preventing the generation of hotspots. In addition to these internal tests, the P-Series has also been subjected to independent testing, one of which is the PVEL and DNV-GL module reliability score card testing. The first generation of P-17 as well as the recent P-19 were the top performers in these tests, according to Moore, while the other generations of P-Series are undergoing these tests.
Performance product
As with the other 500 W+ products, the major ingredient of Maxeon's high-power module is the larger wafer – Maxeon chose the G12 / 210 mm format. As mentioned above, the sole supplier of 210 mm wafers, TZS, is a shareholder in Maxeon and a longtime partner of SunPower in manufacturing shingled modules, so it was not wonder Maxeon favors the 210 mm wafer size. The increase in wafer size also results in an increase in module size. According to Moore, Maxeon is one of the first to initiate the change in module size. While the typical 72-cell module size has remained unchanged for a long time, it the P-17 module series launched in 2015 is longer and more powerful than the typical 72-cell modules. Continuing on the path of innovation, the company introduced P3 UPP, which is wider and longer than standard modules. Now Maxeon is promoting its P5 UPP series that has atypical sizes. Maxeon's latest product is the 5 hypercell version with 545 W rated power, which is based on a 5-string layout. In 2021, the company will be launching the 6 hypercell version in a 6-string layout with a module power of 625 W. Maxeon is offering the bifacial version of the P-Series that comes in dual glass and framed format with a rated efficiency of 21.1%. The shingling technology with parallel circuitry that minimizes losses from shading also enables better and more consistent bifacial power generation on the backside, according to Moore.
Production plans
Maxeon is protecting its technology through patents in several jurisdictions and has built a strong patent portfolio not only covering the design of its shingling technology but also the manufacturing process. Maxeon has started proof of concept with a 400 MW facility in Mexico, where it has produced the P-Series P17 modules. The company has been scaling up the technology over the years and, through its HSPV joint venture, has been demonstrating high volume manufacturing capability of 2 GW with P-19 and P3 modules. The company is now poised to grow faster with plans to increase capacity to 8 GW by next year.
Maxeon is also closely cooperating with downstream system partners—inverter and mounting system suppliers—to ensure that its modules are compatible with their current product offerings. At the same time, this cooperation also makes sure that the future module designs of the company are in alignment with the product development roadmaps of the downstream component suppliers, said Moore. The larger and high efficiency module also helps in reducing labor and BOS costs. In addition, Moore said that the energy yield advantages of P-Series module comes from the circuitry design leading to reduced shading losses as well as bifacial gain, all of which contribute to the ultimate advantage of LCOE reduction.
The presentation was followed by a Q&A with the conference attendees, which we have listed below (selected questions, edited & summarized):
Question: Can you elaborate a little bit on your partnership with TZS? At the moment, they are the only company offering 210 mm wafers. Can you give us a little more background on this?
Joshua Moore: It's a great partnership. As you mentioned, TZS is leading in the industry insofar as 210 mm wafers are concerned. TZS is a great partner for us in terms of scaling up of our HSPV joint venture, which makes the P-Series modules. TZS supplies the wafers to cell vendors who convert those wafers into cells, and HSPV can work those cells into the P5 modules. We have a nice end-to-end ecosystem there. We are able to work closely with TZS following a long-term technology roadmap, making sure that the module roadmap is aligned with the wafer roadmap. The shingling technology offers unique advantages in terms of using these larger wafers. We can cut the wafer into whatever size we want, shingle them together and then create the module we optimally designed for today's power plant tracking system. It is a nice marriage between going to larger wafers and using shingling to get the ideal panel technology with the right current and voltage. With TZS going to thinner and thinner wafers, shingling technology will be the robust connection, and the flexibility that shingling provides will enable the industry to move to thinner and thinner wafers. So that's the partnership from a technology perspective. And from a manufacturing perspective, TZS has invested in Maxeon, and it is going to help Maxeon scale up both the P-Series technology as well as the Maxeon IBC technology. Their great operational expertise and access to capital will help us become a real world-class company.
Question: You are using conductive adhesives, which brings flexibility. Floating solar is one application that, at the moment, is also becoming very attractive as we are seeing land constraints in the densely populated areas. How would your approach of conductive adhesives work in such an environment?
Joshua Moore: The floating applications present new challenges—more humid and more movements. This is really a great place for P-Series. We have already installed P-Series in a number of floating applications around the world. But the reliability and durability I talked about, they come from the flexibility of the cell connection or the encapsulant we use to prevent moisture ingress. All these make P-Series ideally suited to floating applications. We are excited about the growth and applications of the P-Series.
Question: There is also the question related to varying climates. You have shown that you've installed systems around the world. What is the impact of hot climates and desert areas on conductive adhesives?
Joshua Moore: Actually, talking about the history of the technology can shed some light on this. As we mentioned at the beginning, the technology came from Cogenera, which was making concentrated solar systems. Our focus was on solar cells and we needed something that's really efficient and can withstand high temperature swings, and that's where we started using conductive adhesives. We proved it in much harsher applications than we would ever use now on a single concentration system. We proved it at a 25X concentration, which you can imagine is to get 25 times the sun. The operating temperature gets a lot hotter than it would under one sun. The conductive adhesive as well as the rest of the module design is well-suited to high radiance and high temperature climates. The lower temperature coefficient than the standard module design helps a greater energy yield at these high temperature locations. The extensive chamber tests we have done showed the superiority of conductive adhesives over standard soldered joints in these high temperature applications. It's really the temperature swings that cause the degradation in those modules. The conductive adhesive can withstand rapid temperature swings in either direction, which makes it ideal for such applications.
Question: Can you reveal how much your product weighs?
Joshua Moore: The data sheet will be released soon on our website. It is a pretty thin dual glass module, all within the labor requirements to handle it.
Question: You also showed that you foraying into the world of bifacial. Can you tell us more about why you went there, your experience in testing, and results?
Joshua Moore: SunPower has been testing bifacial modules for quite a long time and even bifacial for IBC technology. We have had P-Series bifacial modules in our test lab for several years now and have also been testing and monitoring those products for quite a long time. We felt like now is the right time for the industry move from a cell development perspective, and we also think it provides the right economics in power plant applications to move towards bifacial. So, this is an opportune time in the evolution of our product roadmap to introduce the bifacial module. The technology is ready, and so is the market.
Question: Why do shingled modules perform better than conventional modules under shading?
Joshua Moore: It has to do with a few things. The parallel circuit of the modules—each of those columns of the cells that I showed, we call the hypercell— operate independently. If you have shade on part of one column, the other 5 columns operate independently and are still producing power. We have divided the module into sections in a way that when the module is in portrait and the leading edge is shaded, we only lose about one-third of the power output, whereas the whole module is shut off if the bottom edge is shaded in the case of a conventional full cell module. In a half cell, it's probable that the bottom of the module would shut off. With P-Series, one-third of the module is shut off, because we have the module vertically divided into three with the diode configuration. Then in landscape, as you shade the leading edge, you only affect that particular hypercell, and the remaining hypercells operate at full power and full voltage. Both are important as operating at full voltage allows the system to stay within the optimum window of the inverter and keeping the whole string at the optimal voltage range.
The other aspect would be, because we have many connection points between each cell, if a very small portion of the cell is shaded, current can flow around that block area pretty easily, not causing much power loss. We have a lot of degrees of flexibility for the current flow though portions of the module are shaded.
Question: You also mentioned you have a strong patent portfolio. Nevertheless, some Chinese products are also based on shingling technology. Any comments on that?
Joshua Moore: I think it's best for me to let our legal team handle these IP discussions. But we are certainly monitoring our competitors' technology and keeping track of patent violations, if any.
Question: There is a question regarding standards. As you are the leader for shingling, are you happy with the IEC standards and do you think they are sufficient to also reflect your unique technology?
Joshua Moore: Certainly, for the industry, it will be nice to see maybe a more stringent hotspot test that showed our module can be much cooler and safer for power plant systems and commercial roof systems. I think, IEC testing is a nice benchmark, but the industry has shown the need for going beyond that type of testing, and a test several times the IEC standard is typically needed to prove the long-time reliability of a product. That is why tests like PVEL scorecard have evolved and become so popular.
Question: It was nice to see the strings in action and impressive how flexible they are in your presentation. What happens in the scenario of a cell break, and also in comparison to a conventional module?
Joshua Moore: If there is a crack in one of the cells in the P-Series configuration, we typically experience less power loss and less risk for the hotspot. There are a couple of reasons. One, the cell is smaller at one-sixth the size of a standard cell and the current of the cell is lower; and if there is any sort of resistance, it is one-sixth of the standard cell. And secondly, because the cell is smaller, if the crack is initiated typically at the end of the cell, it will only travel one-sixth the length of the normal crack. Consequently, the power loss will be smaller. Then instead of having just three, four or five connection points between the cells, we have many connection points along the edge created by the conductive adhesive, providing many pathways for the current to flow around the crack. Typically, less power loss is associated with cracks in the P-Series design.
Question: You also said, you are really flexible in how you configure the modules because it is very small and you can adapt it to different needs. Looking a bit into the future, it looks like the rapid growth in power ratings is only going to continue. Is this the way to go? We have also heard from several presenters today that there are limits especially when it comes to logistics. What are you seeing when you look at your portfolio?
Joshua Moore: We are excited about the 545 W P-Series that we are introducing. We think the industry is ready for that in terms of logistics, shipping, tracker and inverter design. I think there is a nice partnership with the balance of systems providers, based on which module vendors have started introducing larger modules, like we have our 625 W module. We partner closely with tracker system designers to make sure their next-generation trackers are ideally suited for that particular application. I am excited about the innovation that is coming down the pike over the next several years. I think it will lead to even lower cost power plant designs and it certainly seems like bigger module size is leading cost reductions at the moment. I am sure we will hit the peak at some point, but we are not there yet.
Question: What about n-type cells? How is shingling technology suitable for n-type technology?
Joshua Moore: Ironically, the one technology that shingling is not suitable for is back contact, which is our Maxeon interdigitated back contact solar cells. We cannot do shingling there; we need front contact to do the shingling. So, we've worked with n-type TOPCon and heterojunction in the past and it showed that shingling works very well with those technologies, and we think that is where the next separation between the product portfolios is going to come from. We are constantly monitoring the evolution and the cost structure of those technologies as well as long-term reliability. Once those technologies prove themselves on these points, I could see us introducing the n-type version of the P-Series at some point in the future.
TaiyangNews: Thank you for your presentation at the TaiyangNews 500W+ Solar Module Conference.
The Maxeon Solar Technologies presentation of Joshua Moore can be viewed on the TaiyangNews YouTube Channel here.