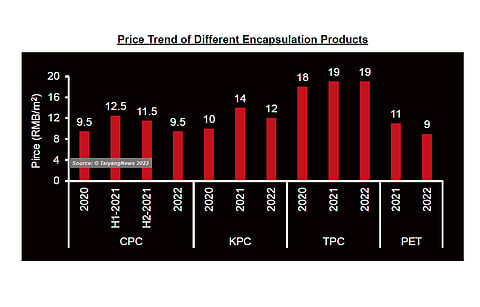
The encapsulation solutions for solar panels are increasingly becoming cell and module technology specific, and then also side specific. That means, the type of polymer used primarily depends on the cell technology – PERC, TOPCon, HJT –, module technology – monofacial or bifacial –, and the side of the module – front or rear. Sometimes, the encapsulation material selection is also influenced by the backsheet type. This is also nicely summarized in a slide from Cybrid's presentation at the TaiyangNews Reliable PV Modules Design event (see Stephen Gong's presentation: Innovations In Solar Module Wraps).
This may not be new, but with more and more cell technologies entering the mainstream, the prominence of differentiation is more obvious. If the developments associated with encapsulation materials are to be expressed in one sentence, it is compatibility with advanced cell technologies such as TOPCon and HJT. Below, we summarize the important trends in encapsulation materials categorized according to the cell technologies. However, we will also outline updates in TPO and silicones that are not mainstream.
Encapsulation Material Price Development If there is anything beyond cell technologies in the encapsulation segment, that's price, and in a good way. The price for EVA resin has fallen considerably from an all-time high of 300,000 RMB/ton in 2021 to 15,000 to 20,000 RMB/ton, and this downtrend is expected to continue further. While we do not have a reference, the price of the POE resin was around 330,000 RMB/ton during the end of 2022, according to Cybrid's International Marketing Director Eric Yang. Overall, the prices of encapsulation materials have dropped compared to H1 2021. As can be seen from the graph, the prices for all varieties of encapsulation materials are back to their 2020 levels. A note here that while the prices of 2020 and H1 2021 are taken from the previous edition of our survey, the H2 2021 and H2 2022 prices are from a partner who wants to stay anonymous, and thus the source remains unidentified. As a consequence, these prices may not be accurate, but can serve as reference.
The prices at the end of 2022 were as follows:
Encapsulation Solutions for PERC Modules PERC is still the current state of the art cell technology, and the encapsulation solution depends on the module technology – monofacial or bifacial. Irrespective of the module technology, the front side encapsulation is always transparent EVA for PERC, which still provides the best cost performance ratio. While the price of the EVA resin did increase quite a bit, it also came down at the same pace to become cost competitive again. As for the rear side, white EVA has nearly become the standard for monofacial modules. The white EVA increases the light reflection from the cell gaps in a finished module, resulting in power gains. Replacing transparent EVA with the white variant on the module's rear side boosts the power output by up to 1%, whereas it could be up to 2% when using bifacial cells in monofacial modules. White EVA is even more effective with half-cell modules due to a relatively lower packing density of cells in such modules. Modules based on M6 and larger cells, which are the mainstream in today's market, are almost exclusively based on the half-cell configuration. With the price of EVA resin decreasing, the white EVA has also become very cost effective. The price difference between the white EVA and transparent variant is only about 5%. All this explains the clear dominance of white EVA on the rear side of the monofacial PERC modules with more than 80% market share.
On the other hand, the white EVA is slightly different from the transparent EVA, in that it is a little harder. This hardness creates stress at the cell edges and busbars during lamination. According HIUV's Senior Marketing Manager Peter Peng, some module makers are also facing low yields with the white EVA due to an overflow of the white pigment. To avoid this, HIUV is promoting a 2-layer structure of transparent EVA and white EVA; however, the company still characterizes it as white EVA. (see: Peter Peng's presentation: Reliable Encapsulation Of TOPcon & HJT Modules). Other leading encapsulation suppliers are also offering such products.
As to the solutions for the bifacial glass-glass modules, the shortcomings of EVA, especially lowPID resistance and acid formation, were addressed through the use of POE. Initially used on both the front and rear, POE's application is now limited to the rear side due to higher costs. It makes sense as the rear side of the module contributes the most to PID due to the presence of aluminum oxide on the rear of the PERC cells. However, POE also has its shortcomings – longer processing time, risk of bubble formation, slippingeffect with round wires (MBB) and relatively lower adhesion to glass – all benchmarked against EVA.
To overcome these limitations, encapsulation material suppliers engineered a multilayer construction called EPE, consisting of a thin layer of polyolefin sandwiched between 2 EVA layers, manufactured via coextrusion. The EPE facilitates a middle ground between EVA and POE, especially with regard to processing time and PID, while avoiding bubbles and slipperiness and realizing high glass adhesion. The cost effectiveness of the solution largely depends on the resin price of POE and EVA. In today's context of very low EVA prices, the EPE is a very cost-effective solution compared to pure POE film. Thus, it is more or less a standard rear encapsulant for PERC bifacial glass glass modules. However, when using a transparent backsheet, POE is still the preferred choice. With transparent backsheet, the choice is mainly pure POE. According to Dow's Li, EVA film doesn't offer strict water resistance required for PERC bifacial modules with transparent backsheet, but emphasized the company's ENGAGE PV POE offers 'excellent' PID resistance. The latter also brings down gram weight and cost by 8.2% when compared with PV grade EVA.
The article is an excerpt from the TaiyangNews Market Survey on Backsheets and Encapsulation 2022-23, which can be accessed free of charge here.