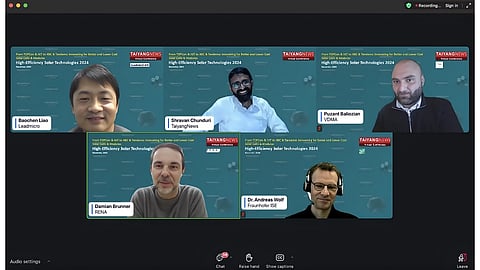
TaiyangNews carried forward the discussion on TOPCon solar technology on Day 3 of the High Efficiency Solar Technologies 2024 conference
Manufacturers discussed the various advancements at their end in TOPCon with most of them confirming tandem in the future plans
Panelists recommended licensing arrangements as a possible solution to the IP related issues that are threatening to slow down the industry’s growth
TOPCon solar PV technology has rapidly taken over the global PV industry in a short span, replacing PERC as the cell technology of choice faster than initially thought. What’s more, manufacturers continue to announce more capacity expansions for TOPCon, which means more innovation can be expected in this field in the near future, both at the materials as well as the process end.
With so much happening, TaiyangNews decided to continue the discussion on TOPCon for one more day before the end of 2024. It picked up the thread on TOPCon solar cell technology from Day 1 of its 4-day annual flagship High Efficiency Solar Technologies 2024 Conference to delve deep into further technological advancements for today’s state-of-the-art cell technology on day 3 (December 10, 2024) as well.
Fraunhofer ISE’s Head of Group Silicon Solar Cells Dr. Andreas Wolf as the keynote speaker, went back to the 1980s to show the evolution of the TOPCon technology calling it a ‘shivering giant.’ Back then, it was known in the semiconductor industry as the silicon insulator silicon (SIS).
He shared that the term TOPCon was coined by Fraunhofer ISE in 2013, following which its industrial implementation started around 2015 by Jolywood and LG.
Since then, TOPCon technology has come a long way to overtake PERC as the leading solar cell technology in industrial use. One of the major contributing factors among several others in its journey is the Laser-Enhanced Contact Optimization (LECO) process.
A game-changing innovation, LECO has been instrumental in increasing TOPCon cell efficiency as it decoupled the contact, and also enabled the use of aluminum-free pastes, zero busbar (0BB) approach, much lower firing temperatures, and very different boron diffusion parameters, said Wolf. Developed by a Germany based start-up, Cell Engineering, the company was fully acquired by Q Cells in 2023, and LECO is now being licensed to other TOPCon cell/module manufacturers.
At Fraunhofer ISE, the effort now is on copper plating contacts to replace silver paste consumption that accounts for a large part of the production costs. Fraunhofer ISE has started with a pilot fabrication of M10 TOPCon solar cells with electroplating using copper. The initial batch demonstrated similar efficiencies as screen printing at 24% each, but with 93% lower silver usage, he shared. Wolf is confident that plating cells will be able to be processed without silver consumption in the future - by using Sn as the capping layer for copper instead of silver.
Passivated Edge Technology (PET), developed at Fraunhofer ISE, helps recover losses by passivating the edges of shingled or half-cut cells. He said it is especially valuable for high perimeter cell area fractions. However, several manufacturers have developed their own methods to achieve these results.
Wolf also talked about TOPCon Rear Emitter (TOPCoRE) technology which replaces n-type by p-type wafers, with no front conductive layer and the efficiency can go up to 26%, as against 25.8% in TOPCon. Its major benefit is that it omits inherent recombination of the front surface which is a limitation for the current TOPCon technology. However, the challenge is related to the alignment of the structures which can be met by industrial production conditions.
In the future, Wolf sees TOPCon cells as forming a good choice for the bottom cell in a tandem structure in a multi-junction configuration.
Trinasolar Product Manager Lukas Ye talked about the advantages and growth of its industrial tunnel oxide passivated contacts or i-TOPCon technology. The tier I Chinese manufacturer recently announced achieving 26.58% of solar cell efficiency for its i-TOPCon cell, claiming it to be the 1st time that n-TOPCon cell efficiency exceeded 26% on commercial size formats (see Trinasolar Achieves 26.58% ‘Record’ N-Type TOPCon Solar Cell Efficiency).
Ye said that this efficiency is based on n-type 210R wafers and is ready for industrialization in the form of its flagship Vertex series. Trinasolar says this paves the way for the company to target to further improve Vertex n module power by 30 W to 40 W using its i-TOPCon Ultra technology, reaching up to 670 W output for its medium sized modules for C&I and utility segments.
Drawing a comparison with TBC, Ye presented case studies to show that its i-TOPCon Ultra excels in low irradiance conditions, achieving 3.2% higher energy yield, and higher bifaciality. Calling it i-TOPCON 2.0, Ye said, the company plans to have 10 GW annual production capacity from Q2 2025.
Going forward, under its i-TOPCon technology roadmap, Trinasolar will continue to stick to it as the technology of choice long into the future. Between 2025 and 2029, it will target to achieve a laboratory cell efficiency of over 27% for i-TOPCon Ultra and a module efficiency exceeding 25% using fully passivated contact cell efficiency. From 2030 onward, it plans to release i-TOPCon with perovskite in tandem, aiming for over 30% cell and 28% module efficiency.
Vertically integrated manufacturer Tongwei Solar’s Regional Technical Service Director Jerry Jiang presented the company’s technology roadmap and advantages in integrated supply chain at the conference.
At of November 2024, Tongwei had 850,000 tons of polysilicon production capacity, 20 GW of ingot of wafer each, 126 GW of solar cell and 85 GW of modules. This vertical integration ensures full traceability and quality control.
Tongwei currently has a presence in all the leading technologies. While PERC is on its way to being phased out, it has GW-level capacities in TOPCon and HJT. For back contacts or XBC and perovskite THC tandem along with TOPCon and HJT, it continues to conduct further research.
For TBC technology, the company has a pilot line that’s capable of producing both p-IBC and n-IBC with a respective cell efficiency of 25.51% and 26.66%.
Under its cell technology termed as Tongwei N-type passivated contact Cell or TNC 1.0, the manufacturer has achieved a cell efficiency of over 25.4%. For TNC 2.0, it aims to exceed 26.5% in cell efficiency by incorporating technologies like EPT, 0BB, poly-layer optimization, advanced paste formulation, etc. It uses this structure for G12 and G12R wafers for various scenarios.
Presenting its MoNo 2 solar cell technology as providing a competitive edge to module makers was JTPV's R&D Manager Xinrui An. Solar cell manufacturer JTPV’s MoNo 2 solar cell technology empowers its customers to compete in the market, according to An as he claimed it maximizes customer ROI and enhances power generation efficiency.
The MoNo 2 cell incorporates advanced metallization, improved edge passivation, and rear optical optimization. Key advancements over MoNo 1 include half-cut edge passivation (HEP), super thin fingers, multi-busbar metallization, among others.
Use of narrower fingers with smaller spacing helps with reduced resistive losses in the grid, and allows for higher emitter sheet resistance. According to An, super thin fingers lead to a 0.1% efficiency gain with optimized contact patterns.
A popular choice of late, HEP is increasingly preferred by module manufacturers to reduce risk losses in modules. An claims that the use of HEP in its MoNo 2 solar cell increases power output by around 5W for both single-glass and double-glass modules.
Another technological advancement it uses is the wave back surface field (WBSF) that reduces parasitic absorption by optimizing rear passivation layer properties. It leads to improved cell characteristics and bifaciality by up to 90%. This works best for various applications including solar farms, and carports.
JTPV currently operates a 40 GW solar cell production capacity in China. It is now expanding overseas with a 5 GW solar cell production in Oman, construction ongoing.
Vertically integrated DMEGC has incorporated changes such as introducing poly-fingers, and defect passivation repair to improve its n-type Infinity solar cell technology, shared the company’s Product Manager for Southern Europe at DMEGC, Alejandro Coll Garcia.
DMEGC currently operates all of its module manufacturing processes with 100% renewable energy and plans to get the same for its cell manufacturing as well as its target to lower its carbon footprint.
For its Infinity RT series of solar cells, DMEGC uses rectangular cells, while for the Infinity series square cells are used. This configuration allows adaptability to different application requirements, explained Coll. DMEGC’s current Infinity solar cell lab efficiency stands at 26.8% which it targets to expand to 27.05% in H1 2025, eventually reaching 28.20% by H1 2028, as per its cell efficiency roadmap.
At the cell level, Coll said his company has incorporated some changes like poly-fingers, defect passivation repair to improve voltage and reduce cell temperature.
At the module level, it integrates anti-glare glass and light redirection films to lower reflection and enhance light utilization. The reflective brightness of its anti-glare Infinity RT series module was found to be 20% to 30% of the conventional module making these useful for installations near airports, urban centers or even parks.
Currently, DMEGC’s highest efficiency double glass module G12T has 705 W output targeted to be improved to up to 720 W by 2026 with further R&D efforts.
Senior R&D Manager Solar & Battery at RENA Technologies GmbH, Damian Brunner presented his company’s GW-scale wet chemical equipment solutions for both TOPCon and HJT technologies. The mainstream n-type TOPCon solution from RENA uses texturing, boron emitter etch and poly etch & clean as the 3 main wet chemical steps, offering a throughput of up to 15,000 wafers per hour. He said the wet chemical edge isolation with RENA tools is available at throughputs surpassing 1 GW TOPCOn solar cells per line/year.
In Q4 2024, RENA launched its new InEtch Side 4+ product, which is a 12/14-lane inline single side glass/oxide etching tool with a length of 4.8m. The German manufacturer touts up to 16,000 wph for M10 wafer size for this tool as it promises ultra-high throughput removal of silicon oxide layers and doped glasses.
Another new feature he threw light upon is the new generation texture additive monoTEX H2.7 that RENA introduced into TOPCon production for a tier I customer. This one enables smaller and pointy pyramids compared to PERC processes. Its post cleaning process after alkaline texture is based on ozone for best cost of ownership (CoO), he added.
Comparing the cost of CoO for typical China made tools with RENA made tools for wet chemistry steps of a TOPCon line, Brunner calculates a 30% difference, RMB 0.59/W for RENA compared to RMB 0.89/W for Chinese tools. While his company’s tools have higher CapEx, he argued that these have lower power consumption, and reduced payback time of a maximum 1 year. He stressed that it is the low OpEx that ‘keeps you in business.'
Senior Manager Marketing for Cybrid Technologies, Anurag Mishra pitched the company’s proprietary RayBo film for TOPCon presenting it as the solution to the technology’s UVID issue thereby improving its performance and financial returns.
Mishra shared RayBo’s origins saying in its original form, it was invented by Dr. Onouchi Hisanari in 2013 and patented by Nitto Denko. Cybrid started developing it further, supported by Nitto Denko. Since 2023, Cybrid has been producing RayBo under exclusive rights for its commercialization from CHOSHU that bought the patents from Nitto Denko for the UV conversion agent and POE film.
According to Mishra, Cybrid devised its RayBo film especially for HJT and TOPCon modules as a light wavelength conversion film, embedded into light-conversion agents into materials like EVA, EPE and POE. The way it works is through an orbital transition mechanism, converting UV light into visible blue light boosting energy generation. This way it offers protection to the solar module from damaging UV rays.
Under damp heat (DH) tests, it has shown less than 10% degradation in its light-conversion ability even after more than 2,500 hours of exposure. This, he said, proves its usefulness in high-humidity environments like coastal areas.
For TOPCon modules, Cybrid said its UV conversion film demonstrates up to 0.53% improvement in energy output, thus proving its ability to withstand environmental stresses.
Mishra claimed that nearly all the HJT makers currently use its RayBo film while the trend is picking up among TOPCon makers as well. In India especially, all major tier I manufacturers are already testing this film for TOPCon production.
Leadmicro’s Chief Scientist (Professor) Baochen Liao addressed the challenges related to UVID in PV devices. Based on comprehensive literature reviews of UVID impact from single dielectric layer to stack layer to emitter surfaces to cell level to module level and the underlying mechanisms, he suggested that UVID issue can be mitigated by changing the composition, density and thickness of the ARC layers. Multiple models are required to further clarify the enabling mechanisms.
According to Liao, contrary to misconceptions AlOx mitigates UV degradation rather than causing it. The literature review shows that modules with AlOx performed stably post-UV exposure compared to SiNx-based modules, which degraded significantly.
Leadmicro’s production equipment for TOPCon technologies focuses on UVID solutions without compromising on efficiency and power generation. Its 5th generation PECVD ToxPoly technology reduces process complexity since a single tube can help with in-situ tunnel oxide, in-situ poly-Si doping, in-situ mask, etc.
This 5th generation PECVD ToxPoly comes with a non-cooling tube/electrode maintenance solution that reduces maintenance time by 500% from 25 hours to 5 hours, and capacity loss by 87%, thereby helping lower the costs. Liao shared that the company already has 2 to 3 years of production data that shows high market share.
Like every other leading company in the PV industry, Leadmicro is also getting perovskite ready.
Moderated by TaiyangNews Head of Technology Shravan Chunduri, the discussion for the panel revolved around the potential for further improvement in TOPCon which is already the leading PV technology in the world today.
Fraunhofer ISE’s Dr. Andreas Wolf said that even though TOPCon took its baby steps at the Fraunhofer lab, the baby has now grown and been nurtured by various players in the industry. It will continue to advance in the future with a bright future as a tandem bottom cell. Its implementation in Europe will have its advantages too, but to compete with the Chinese on cost and close the gap, government support will remain crucial.
Puzant Baliozian Lead Consultant at VDMA, which publishes the International Technology Roadmap for PV (ITRPV), stressed that the historical advancements of PV in Germany and European markets show that the western world has the potential to develop an industrial chain. IP challenges abound which is important to maintain quality and independence, but when it comes to a technology like TOPCon that has undergone various transformations at the hands of several companies, licensing arrangements should break the impasse.
Even though the world is fast moving to TOPCon, in the USA companies wish to start with PERC, according to RENA Technologies’ Damian Brunner. This is not just because it is a robust and proven technology, but also because they want to steer clear of TOPCon patent issues that are mushrooming by the day, he explained. TOPCon is the next step for them once the dust settles.
Commenting on how long is TOPCon likely to maintain its industry leading position in the global PV market, Leadmicro’s Baochen Liao believes that TOPCon should be the dominant technology for the next 3 to 5 years. More innovation can be expected as companies invest in more production lines and R&D. He added that since in mainland China the development of PV technologies is very rapid, its leading position will depend on the growth of the competing technologies.
Conference summaries & presentations
The conference summaries for day 1 (TOPCon 1 focus) and day 2 (HJT focus) are available on TaiyangNews website. Presentation recordings for both these two first days can be found here. For the presentations of day 3 (TOPCon 2) and day 4 (xBC), check here.