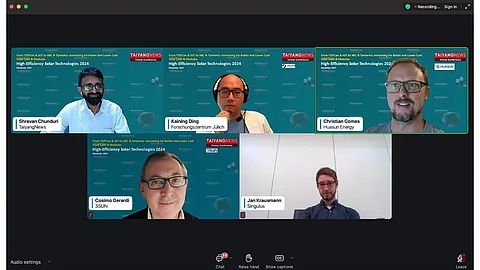
HJT technology was the subject of discussion on day 2 of the TaiyangNews High Efficiency Solar Technologies 2024 Conference
For this annual flagship event of TaiyangNews, key stakeholders invited included module makers, researchers, material and equipment suppliers
They see high potential for HJT even as TOPCon beats it at present at the cost level
In the future, however, HJT is likely to work best in a tandem structure with perovskites than TOPCon or even BC
TaiyangNews High Efficiency Solar Technologies 2024 Conference on day 2 on December 3, 2024 was dedicated exclusively to the heterojunction (HJT) technology. In fact, HJT has seen the highest number of technological innovations. While it is not yet mainstream, a few manufacturers are exclusively focusing on this technology.
Looking at the collective data from the TaiyangNews Top Solar Module Table, TaiyangNews Head of Technology Shravan Chunduri reflected on the growth of module efficiency for HJT technology. The record-high HJT efficiency has improved from REC’s 22.2% in January 2022 to Huasun Energy’s 23.18% in October 2024, showing the technology’s efficiency progress over a period of time.
The keynote speaker, Head of Silicon Heterojunction Solar Cell & Module Department at Forschungszentrum Jülich, Kaining Ding, presented an overview of the current trends in HJT production, including the urgency for manufacturers to shift to zero busbar (0BB) technology to further increase efficiency and reduce costs.
At present, HJT manufacturers use the G12 half-cell format as well as G12R and G10. A wafer thickness of 110 µm is the industry standard, but some manufacturers have started to experiment with 90 µm wafers. Stencil printing with nickel or steel mask has significantly reduced metal consumption. Silver constitutes 40% to 50% of the silver-coated copper paste used, but the aim is to bring it down to 30%. The mass production cell efficiencies range from 25.4% to 25.5%.
At the module level, the manufacturers prefer a bifacial dual-glass module, using reflective stripes on the rear glass. The front glass is textured and AR-coated. A PIB-based edge sealant is the most prevalent option. Commercial module efficiency for HJT modules is more than 23%.
Due to its low-temperature processes, HJT cells can withstand the increased oxygen content due to the process of continuous feeding of polysilicon during ingot production as well as the ingot pullers fed with fluid bed reactor (FBR) silicon, both of which help lower costs.
Manufacturers are increasingly looking at resolving what Ding referred to as dark degradation, which can cost a few watts. This refers to cells losing their efficiency when placed in the dark. It is an issue because the cell is in a dark environment after it is finished and waits to be used in the module. At this point, the module will be made with lower-efficiency cells.
Keeping the cells in nitrogen seems to work as it slows down the degradation. This indicates that the degradation is related to environmental factors like moisture. Most recently, there have been reports of using nitrous oxide or N2O as the oxygen source for the nanocrystalline silicon growth instead of CO2 as a means for controlling dark degradation.
At the module level, there is an urgency to shift to 0BB to further reduce the consumption cost of metallization and increase efficiency. Different concepts are being tested. For example, the most favorable solution now is either to use SmartWire technology by Meyer Burger, or Maxwell’s Integrated Film Covering (IFC) approach to position the wires. Contacting is the same, however, in both methods.
In terms of the market, Chinese HJT manufacturers are willing to become a solution provider for HJT aspirants outside of China. Outside of China, Europe, the US, India, the Middle East, and Turkiye have emerged as the hotspots for HJT production.
He summed up by saying that HJT is already a meaningful case for customers at the system level.
A leading name in the HJT space, solar cell and module manufacturer Huasun Energy has an industry-leading 20 GW annual production capacity. Huasun Energy’s Senior Pre-sales Technical and Product Support Manager Kayn Huang started by sharing the company’s ‘record-breaking’ 768.938 W output and 24.75% efficiency for the Himalaya G12-132 module. The Everest G12R-132 module has also achieved 669.1 W output and 24.77% efficiency.
While these modules are yet to be released commercially, Huang wanted to show the potential for HJT technology for all application scenarios.
Huasun’s transition from traditional busbar design to 0BB using ribbons improves efficiency and costs. Since there are fewer production steps, it reduces production complexity and lowers energy consumption. This makes it a practical choice.
Huasun uses a method where the ribbons are soldered to cells and sticking them to cells using dispensing technology, doing away with the need for a load-bearing film. Compared to the Super Multi Busbar (SMBB) approach, Huang shared that 0BB reduces energy shading by 16.17% on the front and by 27.46% on the rear, thus improving light capture and cell performance.
Moreover, it is compatible with a thinner silicon wafer and uses a thinner ribbon of φ ≤ 0.20 mm, lowering the chances of cracks. Huasun also uses the same paste on both the front and rear of the cell. Huang claims an industry-leading -0.24%/°C temperature coefficient, and a higher bifacial energy yield of 2% to 5% over TOPCon.
The use of these advanced materials enables a significant reduction in the carbon footprint of Huasun modules at 366 gms/W with a wafer thickness of 120 μm. In the future, it aims to further lower it to 300 gms/W with a wafer thickness of 90 μm.
Jiajun Ye, Senior Product Manager at Risen Energy, underscored the company’s unwavering commitment to HJT as the cornerstone of its PV advancements. He emphasized HJT's distinct advantages, including higher efficiency and enhanced reliability, as key factors behind the vertically integrated manufacturer’s strategic choice.
Ye highlighted Risen Energy’s pioneering role in reducing silver consumption, a critical factor in lowering production costs. “We are the first in the industry to bring silver usage below 6 mg/W, compared to the average of 6.6 mg/W for PERC and 9 mg/W for TOPCon,” Ye stated. The company aims to push this even further, targeting 0.5 mg/W. “With this breakthrough, we’ve effectively overcome one of the biggest barrier to the mass production of HJT,” he added.
In addition to silver reduction, Risen Energy has implemented several key technical innovations to enhance cell performance. Among these is the use of an advanced TCO layer deposited with high-mobility target material. This significantly improves electrical conductivity, thereby boosting cell efficiency. The adoption of stencil screen printing technology with unrestricted openings and extended mesh lifespans further contributes to performance improvements. This technique lowers paste consumption, reduces metallization costs, enhances printing quality, and optimizes overall cell performance, explained Ye.
He also touched upon the UVID challenges for n-type modules. Risen Energy addresses this by using UV down-conversion film. The encapsulant converts the UV into the blue spectrum, reducing degradation while enhancing power output.
Risen Energy’s upcoming Hyper-ion Pro module with 730W output and 26.4% cell efficiency will incorporate the above technical improvements when it is available commercially in Q1 2025.
For 2025, the company’s technical roadmap will target 740W with a 26.8% HJT module, followed by a further increase to 760 W and 27.2% cell efficiency. In 2027, it plans to venture into perovskite-HJT.
3SUN, an Enel Group company, is bringing GW-scale solar PV production to Europe with its Catania, Italy Gigafactory. Having started as a thin-film company in 2010, it moved on to HJT in 2018 achieving 24.6% cell efficiency in production 2 years later. Currently, it has started with 600 MW production at what is Europe’s 1st PV Gigafactory in Catania and the 1st to focus on HJT technology. Soon the fab will ramp up to 3 GW annual capacity, all built with Western equipment.
3SUN’s CTO Cosimo Gerardi shared the development of its innovative HJT technology and the future roadmap of the manufacturer during his presentation. This factory with solar cell and module production is upgraded with new tools including PECVD, PVD to produce 800,000 solar cells/day and 14,000 modules/day, translating into 300 million cells/year and 5 million modules/year.
The use of a nanocrystalline silicon layer significantly enhances cell efficiency, said Gerardi. It has been able to enhance cell efficiency with the use of an advanced TCO target material leading to less free carrier absorption, increased fill factor and lower contact resistivities between PECVD/TCO and TCO/metallization.
Quality improvement & cost reduction remains high on agenda for 3SUN. It started with using 60% silver paste, which it now targets to lower than 50% and eventually further down to under 40%.
3SUN’s production also incorporates LED-based light soaking process for in-line post treatment of HJT cells as part of its smart processing. Future process improvements will see 3SUN working on metallization, introducing silver copper paste and 0BB technology, and copper plating as the target is to eventually do away with the use of silver.
Its HJT roadmap targets 27% solar cell efficiency with several technical improvements on the way. However, the future focus of the Italian manufacturer is on tandem HJT and perovskite, achieving 30% efficiency. 3SUN has already achieved a cell efficiency of 29.8% on extended area of its tandem cell in collaboration with CEA-INES.
Responsible for Product Management Solar at SINGULUS TECHNOLOGIES AG, Jan Krausmann shared the German PV production equipment company’s high-throughput HJT solar cell production equipment solutions. All of these, he said, come with a flexible tray design to ensure these are compatible with all wafer sizes, up to G12/G12 half-cut.
Its high-volume equipment for HJT solar cell fabrication covers wet chemical treatment, inline PECVD, inline PVD and PET for edge passivation processes.
SILEC III wet chemical treatment, for instance, is a high throughput tool from SINGULUS with over 8,000 wph for G12 and 14,000 wph for G12 half-cut cells. It has a low wafer thickness adaption and is for texturing and cleaning.
The inline PECVD equipment for a-Si (i,n,p) and nc-Si (n,p) deposition uses IP-protected linear plasma source design for high deposition rates and highly uniform film deposition, he added. It also has a fully automated NF3 cleaning process.
Its inline PVD equipment for ITO deposition has an integrated CRS for double-sided deposition. It offers high accuracy of wafer placement in tray pockets, has high utilization and reduced OpEx.
SINGULUS’ GENERIS PET tool, explained Krausmann, is an industrialized high volume inline solution for the deposition of edge cover layers to realize passivated edges for cells split with laser. Its unique tray design can process all wafer and cut formats with a capacity of 4,800 wafer cuts/tray.
R&D Director of Fusion New Materials, a solar PV paste producer, Jasmine Chen listed cost, efficiency and reliability as the 3 primary reasons for HJT’s higher cost compared to TOPCon, something that the company says it attempts to address with its PV paste solutions.
For HJT, Chen noted that cell manufacturers try to control costs by using narrow screen openings and thinner fingers. To cater to the high demand for such solutions, Fusion has been able to bring down the content of pure silver in its silver-coated copper paste to 55%.
As part of its cost reduction roadmap for HJT fingers, Fusion has developed a new technology with only 20% silver content. Going forward, it targets to lower the silver content to under 10% in its silver-coated copper paste by Q2 2025, and also introduce a pure copper paste.
Chen explained that compared to a 100% silver paste, a 50:50 silver and copper paste leads to around 0.01% efficiency loss, but up to 35% cost reduction. Bringing silver content down to 20% vis-à-vis copper’s 80%, the efficiency loss will range from 0.05% to 0.10% and a cost reduction of up to 50%. Fusion’s portfolio also comprises a perovskite cell paste.
Solar ribbons are made of copper and work like threads joining the individual solar cells and collecting and transmitting current from these. Mengjiao Liang, the Manager of Overseas Market for Suzhou YourBuddy New-type Materials Co., Ltd., discussed the application of ultra-fine low-temperature ribbons in ZBB modules.
For such modules, she recommended using a ribbon with a diameter of 0.18mm and 0.20mm with low-temperature alloys as it offers better yield and high tensile strengths, adjustable solder composition that can be customized, and has excellent wettability and solderability.
Liang pointed out that the low-temperature ribbon used in HJT technology primarily contains bismuth which has questionable reliability but is about 35 times less expensive than indium. Unlike indium, which is sparsely available, China has large deposits of bismuth, accounting for about 240,000 tons out of close to 370,000 tons of the world’s total reserves. According to Liang, in the short term, bismuth production can meet the demand for ZBB modules.
To increase the corrosion resistance of ribbons, YourBuddy recommends adding some rare earth elements like phosphorus, gallium, germanium, and nickel.
At present, the round wire shaped ultra-fine low-temperature ribbon is the most popular, but it will be a triangular ribbon that’s expected to come into wider use since the latter has a thinner diameter, lower soldering melting point, and higher reflectivity, according to Liang.
YourBuddy offers 2 kinds of triangular ribbons, namely ø0.25 mm segmented, and ø0.1mm ultrafine continuous triangular ribbon.
Panel discussion
Moderated by TaiyangNews’ Shravan Chunduri, the panel discussion revolved around the status and outlook for a promising high-efficiency technology. He asked the panelists the reasons why HJT is not part of the mainstream as yet.
Kaining Ding of Forschungszentrum Jülich explained that since TOPCon is a continuation of PERC, it is already a mature technology with a lot more experience, and a lot many people working in the industry, even though HJT is a better technology. Nonetheless, he stressed that the gap is coming to a close now at the system level.
Huasun Energy’s Christian Comes listed economical and technical reasons for the slower movement of HJT compared to TOPCon. The latter is more popular due to volume, but if it is better technology that the customers want in terms of higher bifaciality, better irradiance, then HJT is the way to go.
While TOPCon thrives in China, HJT is gaining traction outside of the Asian giant, especially Europe. 3SUN’s Cosimo Gerardi admitted that the reason the company picked HJT is because it didn’t want to remain dependent for technology. Rather the idea was to be independent with a niche technology, ‘something we will have control over.’
SINGULUS TECHNOLOGIES’ Jan Krausmann added that since HJT has fewer production steps, there is growing interest in the technology in several markets. As an equipment supplier, his company’s strategy is to increase the capacity of each tool to help reduce CapEx. The future, however, will depend on perovskites and tandems.
As a final word, the panelists were unanimous in their opinion that TOPCon will likely remain the industry workhorse for the next few years, while HJT continues to take giant strides too especially with the advent of perovskites. Even though BC is strong as a technology, the fact that perovskites are expected to work better in a tandem structure, BC will see a dead end in terms of optimization 2 years down the line. Hence, being on the HJT side makes better business sense going forward, they summed up.
TaiyangNews will wrap up the 4-day High Efficiency Solar Technologies 2024 Conference on December 11, 2024 when it will bring together PV industry stakeholders to discuss XBC and the future of solar PV technology. Register free here.