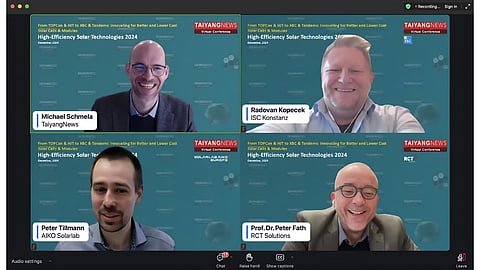
TaiyangNews’ last and final day of the High Efficiency Solar Technologies 2024 Conference focused on BC and next-generation technologies
BC is getting ready to become the industry-leading PV technology before the end of this decade as further advancements boost its efficiency and bring down costs
Europe should use the opportunity to collaborate with the Chinese as the latter face difficulties in the US and Indian markets
IP challenges aren’t likely to lead to any fruitful conclusions, hence the industry should look at partnerships and end the stalemate for the sake of the PV industry
The world of solar PV technology is advancing fast even as you read this, making way for newer configurations to come up. No wonder then that TaiyangNews decided to bring in another high efficiency solar cell technology beyond TOPCon and heterojunction (HJT) to the table for the last day of its 4-day annual flagship High Efficiency Solar Technologies 2024 Conference on December 11, 2024.
Day 4 of the conference was devoted to XBC and next-generation technologies. The keynote speaker for the conference, the Co-Founder and Director of ISC Konstanz Radovan Kopecek, shared his perspectives on the efficiency race for various new-age technologies.
Known as the ‘pusher’ of the back contact (BC) technology, Kopecek sees nPV or n-type wafer-based solar technologies like TOPCon, HJT and interdigitated back contact (IBC) becoming the ‘emperor of energy markets’ 2027 onward when module efficiency will exceed 25% and the levelized cost of electricity (LCOE) will drop under $0.01/kWh.
Among these various n-type cell technologies, BC has the brightest future. “With BC technology, we will reach an average of 25.5% average module efficiency in 7 years from now,” forecasts Kopecek.
He referred to the top 2 commercial module efficiencies on the TaiyangNews Top Solar Module Listing to prove his point since both belong to n-type with BC cell technology from AIKO and Maxeon, both exceeding 24% (see TOP SOLAR MODULES Listing – November 2024).
TOPCon cell technology will no doubt lead the pack till at least 2026, post which Kopecek projects n-type BC bifacial to replace TOPCon from 2027 onwards when its bifaciality reaches 80%, till it incorporates as tandem IBC bifacial from 2036.
The biggest advantages of BC, he explained, are highest efficiencies and low breakdown voltage. Driven by these factors and also further advancements such as lower silver consumption as the industry innovates with copper screen printing, BC will lead the future of the solar PV market. Sustainable development will be the key going forward, added Kopecek, which will lead to cost reduction as well including the change from silver to copper an area where work is currently ongoing.
LONGi’s Product Marketing Manager Dante Zeng called his company a pioneer of the BC technology having introduced it to the market for the first time in 2022. The manufacturer made the technology its own with the hybrid passivation back contact (HPBC) technology.
Having achieved 25.5% cell efficiency with HPBC technology, LONGi reported 26.6% efficiency for HPBC 2.0 generation in 2024 using its TaiRay wafer and incorporating a zero busbar (0BB) structure, among other improvements. It is now inching closer towards the theoretical limit of 29.4% cell efficiency in mass production, pointed out Zeng.
Even though most tier I manufacturers prefer TOPCon or work on HJT, LONGi chose the BC route due to its potential for high efficiency, pleasant aesthetics, and reliability, explained Zeng. It has the highest theoretical cell efficiency among all silicon technologies at 29.1%.
A soft breakdown design structure under HPBC 2.0 reduces shading power loss, allowing blocked current to bypass and prevent localized overheating. At the same time, shared Zeng, its high-doped, low resistance self-developed bipolar hybrid passivation contact layer improves overall cell performance.
Compared to a TOPCon structure, LONGi’s HPBC 2.0 based Hi-MO X10 modules have lower linear decay, which brings an additional power generation gain of over 2.18% over its 30-year lifecycle.
Going forward, LONGi’s cell technology roadmap shows it continuing with the BC platform, but exploring the HBC or heterojunction+back contact route, aiming for a mass efficiency of 27% in 2026. It has a pilot line for HBC, and also an R&D line for tandem.
AIKO Solar’s Product and Solution Manager Mohammad Alshrouf called the all back contact (ABC) technology that the manufacturer adheres to as the ultimate route to achieve the ultimate efficiency for monocrystalline silicon cells. Tandem BC cells are the development direction for AIKO in the future.
The absence of grid lines on the front of the cell in a BC structure, with full passivation at the back, ensures no shading loss on the front and also a higher cell efficiency. Thanks to its low temperature coefficient of -0.26%/°C as against -0.29%/°C for TOPCon, it generates 6% to 10% higher power than a TOPCon module.
Alshrouf stressed that AIKO’s ABC modules have 1.2% lower degradation in 25 years and 1.5% less in 30 years vis-à-vis TOPCon. These are also attractive an option for the residential segment.
For its upcoming INFINITE solar modules under ABC Gen III, AIKO is undertaking more technical measures to improve the module power as well as efficiency. One of these features is the decreased non-cell area by increasing the cell coverage ratio, which alone is likely to increase the output by 8 W. Eliminating the gap between cells will also add 5 W. Getting rid of the busbars will also reduce electrical losses. Overall, these measures are likely to improve the output by 15 W.
In 2025, AIKO will run GEN II and GEN III lines as standard products. GEN III can be expected to be rolled out by the middle of next year.
SPIC Solar, or the State Power Investment Corporation, is one of China’s leading power generation groups. It has installed 238 GW of power generation capacity, including 69.19 GW of PV plants. The company is also active in solar PV manufacturing through its Qinghai Huanghe Hydropower Development Xining Solar Power Branch.
SPIC Solar's Marketing Manager Seki Zheng shared that the company started with a 200 MW IBC solar cell and module production line in 2019 in collaboration with ISC Konstanz of Germany. Today, it operates 200 MW solar module and 1.1 GW solar cell production lines annually.
Having started with p-poly IBC, SPIC currently works with TBC or TOPCon contacts+IBC cell, bringing the best of both worlds as their combination allows the cell to maintain steady improvement in efficiency.
While the p-poly IBC mass production efficiency stands at 25% in 2024, Zheng said the TBC cell efficiency in mass production has reached 26.5%.
These TBC cells carry no busbars on the front side, which improves the light absorption by about 2.3%. Zheng said these are compatible with other technologies as well, including perovskite/BC tandem cells, and hence offer a higher potential for efficiency improvement.
With no busbars on the front, the gap is more pronounced in a BC cell when the module is encapsulated. To deal with this, Zheng said SPIC Solar adopted the BC cell stack-welded interconnection technology that eliminates the gap between cells and improved module efficiency.
With these features, SPIC Solar’s Andromeda 3.0 n-type TBC solar cell modules are suitable for several applications including residential PV, C&I, and large ground-mounted installations, along with flexible, colorful BIPV options, as well as solar tiles and vehicle-mounted PV systems.
Zheng also presented the company’s pure black design module for buildings and rooftops with an anti-reflection coating film and high transmission glass. SPIC Solar says its new textured surface technology for these modules reduces blue light reflection and forges the purest black appearance.
SPIC Solar will continue to focus on TBC technology for the next few years. The future will see it use TBC for perovskite tandem structure to realize 2-terminal output and meet diverse market demands.
Another leading BC technology proponent that has been working on the IBC technology for over 40 years is Maxeon Solar Technologies. Its Principal Engineer Dr. Guangqi Xu threw some light on the technology’s reliability aspect.
The company claims its single-junction IBC cell fares well on the 3 parameters of a successful cell technology, namely high efficiency with the narrowest gap to the theoretical limit, a strong and mature ecosystem, and robust reliability with over 40 years of useful life and 0.25% annual degradation.
Maxeon started with an over 20% efficient commercial solar cell in 2004 as Gen 1 based on the diffusion process. Since 2015, it has been working on the TBC structure. In 2023-2024, it entered Gen 7 achieving a module efficiency of 24.7%. Next year, it plans to launch Gen 8 or Max 8 with a new architecture, a larger wafer size and a higher efficiency of over 25%, announced Xu.
Armed with solid working experience of this technology, Xu stressed that Maxeon modules are highly reliable, affording it to offer a longer reliability/performance guarantee than perhaps anyone else in the market.
Maxeon uses a solid metal foundation that relieves metal stress, thus making its modules durable, unlike conventional cells such as mono PERC, TOPCon, and HJT where metallic wires are mostly used. Bending of the wires due to the temperature can make these wires weak. Citing 3rd party test results, Xu said that his company’s modules performed better than the best TOPCon modules in the market after the damp heat aging test.
For any solar technology to expand, it needs a supportive ecosystem that must factor in both upstream and downstream limits. With this ecosystem assessment of the PV technology, XU believes that moving from TOPCon to BC has less technical challenges than moving from PERC to TOPCon.
Hangzhou First Applied Material’s Overseas Sales Manager Bo Jin presented the company’s encapsulation solutions for BC modules, a cell technology whose market share he said is set to increase in the coming years for its high-power generation and aesthetic appeal. XBC can also adapt to different cell technologies.
In the BC cell structure, the front has no contacts, so a thinner encapsulant can be used. However, since both positive and negative contacts are placed, it needs to be covered with a thicker layer. A white or black film as encapsulant at the back can also boost power generation.
Hangzhou First recommends its POE and thin EPE films for the front side of the XBC cell with their excellent anti-PID performance and high light transmittance. Its EP304 thin co-extrusion film can meet the anti-PID requirements with a POE layer of 110 g when combined with TOPCon cells. Since TBC cells have similar requirements, the EP304 can meet the same for this cell structure, added Jin.
A special high-reflective black-white film F806WH from Hangzhou First has high infrared light reflectivity. The black color on the cell side makes it look aesthetic, while the white color lends infrared reflection, boosting module power. The company recommends it both for glass-glass and glass-backsheet modules with BC cells.
In case of an HPBC cell, Jin recommends using POE or EPE on the front and EVA or white EVA on the back. For a TBC cell that usually uses a dual-glass structure, POE or EPE can be used on the front as well as the back. The HBC, on the other hand, needs high water resistance and anti-UV attenuation because of which Jin recommends POE or EPE or EVA on the front, and POE or EPE at the back.
Hangzhou First has also developed a new insulating ink to insulate the positive and negative contacts of BC cells. Other BC products in its portfolio include black backsheet and a cover strip to cover the wires, among others.
Metallization paste producer DKEM’s New Technology Development Director Fangqing Guo traced the evolution of metallization solutions for the IBC cell technology. Out of the various BC cell structures, from an efficiency and cost-effective point of view, Guo picked n-TBC and HBC as having the highest potential for growth in the future.
Silver paste represents a significant amount of non-silicon cost in PV production, especially for TBC. Right now, the TOPCon silver cost consumption is about 9 mg/W to 10 mg/W. For the sustainable development of TBC cells, it is important to look into the solutions to bring down this cost.
At DKEM, Guo says fine-line printing is one approach to reduce silver costs. For TOPCon front and rear, its customers prefer narrower than 10 microns, but for BC it is still more than 30 microns, thus there exists room for further reduction in the latter. The adoption of 0BB will also greatly reduce silver consumption for TBC as is a growing trend in the industry.
Lowering silver content is another approach, but the long-term approach is the base metal paste. This will involve completely replacing silver with copper or any other metal. This requires further research into the reliability and cost-effective aspects, which DKEM is currently conducting. A lot of data is required to eventually convince the customers to go silver-free, he added.
DR Laser’s Vice President, Sales & Marketing Ben Lee presented the company’s ‘breakthrough’ Laser Integrated Bonding (LIB) technology for 0BB and XBC manufacturing especially as the world enters the era of XBC.
In the journey to 0BB XBC manufacturing, the challenges relate to reliability, module power, manufacturing cost, and bifaciality. This is where LIB comes in. Lee defined LIB as an innovative laser soldering process specially developed for 0BB XBC PV modules. It enables ‘perfect bonding’ between solar cells and ribbons with a single laser process at the module scale, preventing micro-cracks and ensuring non-contact soldering.
Among its other benefits is higher bifaciality as it can increase by more than 10% than reference IR soldering. Further improvement is expected. LIB-backed 0BB can also bring down silver paste consumption by more than 20%, Lee claimed, referring to the results shared by 3 of its customers.
This technology can help reduce silver consumption to 80 ~ 90 mg and enhance the bifaciality of XBC modules to 75%, potentially to 80% or even higher, summed up Lee.
Presenting the company’s SALD technology for perovskite solar cells was Ideal Deposition’s Process Technology Manager Dr. Jun Wang. The company makes production equipment for perovskite solar cells (PSC) with an annual capacity to produce 300 atomic layer deposition (ALD) units/year.
ALD is well-established and widely acknowledged as a deposition technique for solar cell layers. However, Wang said that ALD’s long production process approach limits its power. SALD, or spatial ALD, has a shorter process time, she explained, adding that it is suitable for large-area deposition and mass production. It increases the deposition rate compared to ALD.
Ideal Deposition developed its deposition solutions for perovskite solar cells based on SALD, in which the 2 half reactions are not separated by time but by space, as the substrates move laterally absorbing different precursors separated by inert gas curtains. Wang claimed there is growing interest in the technology in the PSC market.
Executive panel discussion
In a free-flowing conversation with TaiyangNews Managing Director Michael Schmela, the high-level panel discussion had panelists look into the crystal ball to see what’s the next big thing in solar cell and module technologies.
For Peter Tillmann of AIKO SolarLab, the decision to move from PERC cell production to BC was a no-brainer as it found the latter the perfect replacement owing to its highest efficiency potential. While the rest of the world seemed interested in TOPCon for its obvious cost benefits at the production equipment level, being a BC company helped AIKO differentiate from the competition, he added. AIKO’s world will continue to revolve around BC technology in the future as well, stated Tillmann.
When SolarLab was founded 3 years ago, the idea was to bring European PV manufacturing. There aren’t many barriers between China and Europe, says Tillmann.
Prof. Dr. Peter Fath of RCT Solutions agreed with Tillmann when he said that all his clients want to distinguish themselves from the competition. However, other considerations do step in like the cost; for instance, HJT is difficult to sell due to its high costs. The IP issues come into the picture in a market like the US. As the rest of the world moves forward with TOPCon or HJT, there is a trend among some US companies to play it safe and stick to PERC for now.
Indian manufacturers, on the other hand, are acting like the Chinese as they also start with GW-scale lines. For the Chinese, investor push is making them move their manufacturing footprint beyond China, especially to Southeast Asia.
As the US closes its doors to Chinese technology that’s well-established and cost-competitive, Fath believes this is an opening for Europe to use this opportunity to collaborate with the Chinese using its own strengths in innovation and research.
Radovan Kopecek of ISC Konstanz too bets on the BC technology as he shared in his presentation as the keynote speaker. He shared that while manufacturers in India are investing in TOPCon, they are also in discussions to upgrade their TOPCon line to BC.
While he agreed with Fath’s suggestion for more collaboration with the Chinese for the growth of PV technology, Kopecek pointed out an emerging problem for Indian companies. The Chinese are not keen on sharing their ingot and wafer technology with Indians.
Overall, the panelists were in agreement with regard to the next innovative steps in PV technology, especially 0BB, copper paste metallization, and tandem technologies coming in faster now. Overcapacity concerns will ease soon but it will entail ‘survival of the fittest.’ They also believe IP fights are needlessly slowing down the sector. Instead, the need of the hour is enhanced collaboration.
Conference summaries for Day 1, Day 2, and Day 3 are available on the TaiyangNews website. Videos of the presentations on days 1 and 2 are available here, and for days 3 and 4 here.