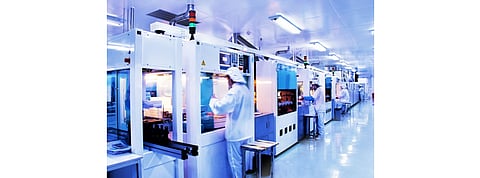
The thinner the better, that's the suggestion of researchers at the Massachusetts Institute of Technology (MIT) and the National Renewable Energy Laboratory (NREL) for silicon cells that will eventually result in lower costs of solar panels. Through their research, they argue the thickness of silicon wafers from the current level of 160 micrometers should be brought down to 100 micrometers and gradually further down to 40 micrometers or less ensuring less silicon in a panel. In the future, the thickness could even be brought down to 15 micrometers.
As a result, it would cut down the cost of individual panels and allow for rapid expansion of solar panel manufacturing capacity.
For their research, the team assessed the efficiency at different thickness levels of four variations of cell architecture including PERC cells and other advanced high-efficiency technologies. They found little decline in performance down to 40 micrometer thickness, using improved manufacturing processes.
Silicon crystal ingot factories where wafers are sliced real thin can start reducing wafer thickness at the source level to deal with the issue but the next step is ensuring huge solar panel manufacturing plants to adapt to thinner wafers, which will be a capital intensive process. Yet, MIT's Zhe Liu says the benefits can far outweigh the costs.
Current manufacturing plants with existing technology can at most bring down wafer thickness to 100 micrometers and ensure 'significant savings' but further technological improvements will be needed to develop necessary equipment and procedures to allow for the thinner material, according to the scientists. Among new technologies, Liu suggests growing thin wafers of silicon crystal directly rather than slicing them from a larger cylinder that could enable further thinning.
MIT professor of Mechanical Engineering Tonio Buonassisi explains the study would be most helpful for those who may be planning expansion in solar manufacturing technologies. A change of this magnitude would require different key industry players to come together to lay out a specific set of steps forward and agreed-upon standards. "There is a path. It's not easy, but there is a path. And for the first movers, the advantage is significant," added Buonassisi.
Wafer holds the key
Detailed research process and findings of this study have been published in the journal Energy and Environmental Science. The researchers call their approach as technoeconomic, meaning economic considerations are as important as those related to technology to further make the solar panels affordable. This is especially true at a time when avenues to bring down the cost of solar panels are being exhausted. The cost of silicon can make a difference, they claim.
However, the focus of big solar module manufacturers is not so much about thinning wafter but rather on enlarging the size of the wafers as it leads to better power conversion and thereby also reducing the overall cost of panels. The maximum size an increasing number of Tier 1 players are looking at is 210 mm, much higher than the present standard of 156 x 156 mm. Very recently, Trina Solar of China said it has started manufacturing 210 mm silicon wafer with multi-busbar technology and 1/3-cut design for its large size PV module (see Trina Solar Begins Producing Modules With 210mm Wafer).